The world’s cumulative proven recoverable oil reserves are about 388 billion tons, of which offshore oil reserves account for about 45% of the total. All countries are vigorously carrying out offshore projects to increase oil reserves. Whether offshore oil and gas drilling, or polar and deep-sea exploration, structural steel is an integral part of the relevant engineering.
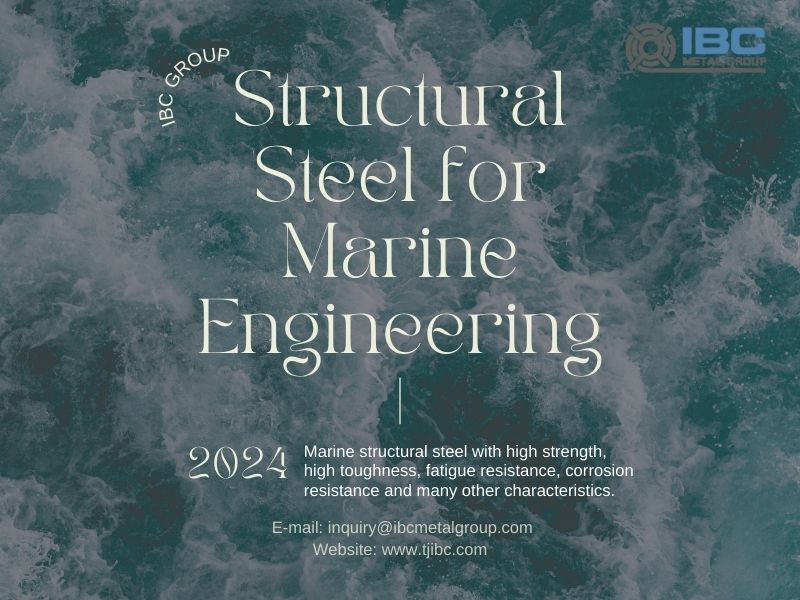
Corrosion and Protection
Marine steel structures include offshore wind turbines, cross-sea Bridges, offshore oil platforms and harbor docks. The atmosphere and seawater corrode these structures for a long time. Therefore, it is particularly important to adopt effective, economical, simple and long-term anticorrosion measures for Marine engineering.
At present, the development of anti-corrosion coatings for Marine structural steel has made great progress. For example, basic epoxy coatings, ethylene coatings, zinc-rich coatings, graphene anti-corrosion coatings, nano coatings, etc. These materials are of great significance in the context of severe Marine anti-corrosion forms.
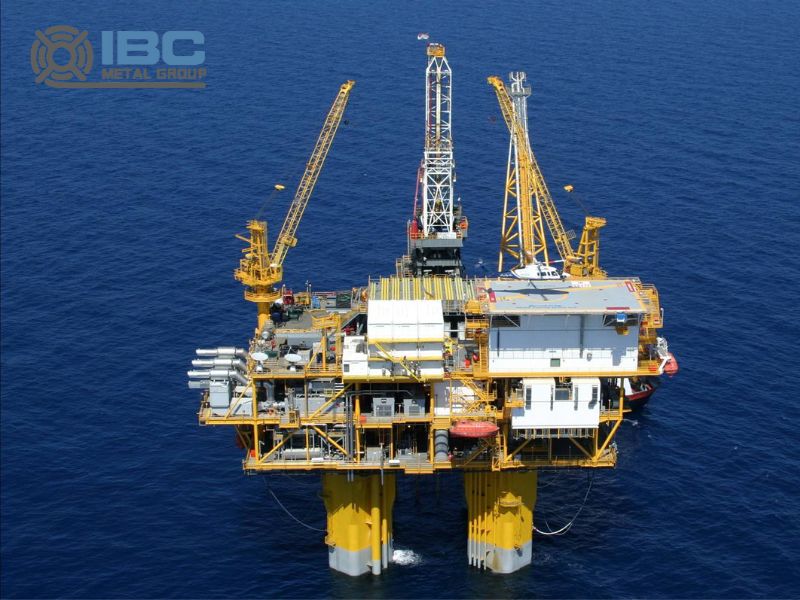
1. Epoxy coatings: It improves the properties of epoxy coatings by adding a variety of filling coatings, additives, additives and modifiers (mainly long-acting chlorosulfonated polyethylene rubber), so as to enhance its adhesion, strength. And it improve the corrosion resistance and permeability of epoxy coatings.
2. Graphene anticorrosive coatings: Most of the current research is to add graphene to other materials as an auxiliary material. Graphene has good chemical stability and thermal stability, which can reflect sunlight in the sea atmosphere and avoid the aging effect of ultraviolet rays on the paint.
3. Zinc-rich anti-corrosion coating: By using zinc powder as the main filler. This kind of coating has excellent rust resistance, better adhesion and lower surface energy. Zinc-rich anticorrosive coating is widely used in Bridges, ships and large steel structure equipment. Zinc-rich anticorrosive coating is an excellent primer. It can occur electrochemical reaction to achieve the purpose of anti-corrosion.
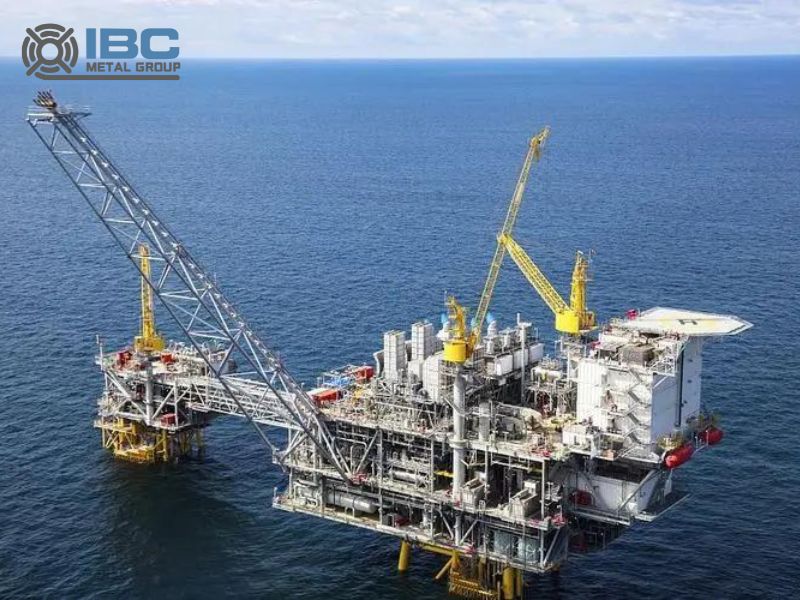
Structural Steel Development Trend
1. Mold casting: Mold casting is by injecting molten metal directly into the prefabricated mold. And then cooling and solidifying to form parts or components. Although the total production capacity of die casting is decreasing year by year, die casting technology is still the lowest cost casting process, with good flexibility and diversity. It can also be used for small-scale production of new steel. So for small batch, special steel production, large thick or extra-thick plate and large round production, die casting technology still has irreplaceable advantages. In addition, the casting technology has a good compression ratio. And the steel ingot produced has good quality and high strength, which is suitable for various high-intensity production or working environments.
2. Continuous casting: Continuous casting technology is a method of continuously casting molten metal into billets or plates, which can be used to produce large and high-strength steel plates, with the advantages of low investment, low energy consumption, high efficiency and environmental friendliness. In addition, continuous casting can also improve the uniformity of materials and performance consistency, through continuous casting technology. It can produce high-strength, high-corrosion resistance of hull structures and components. And it improve the carrying capacity, durability and safety of ships, Bridges, port facilities, while reducing weight, improve facility stability, safety and maintainability.
3. Special smelting: Special smelting technology is to improve the corrosion resistance and strength of the material by adjusting the alloying element content of the steel to meet the requirements of strength, corrosion resistance, wear resistance and low temperature performance. The technology includes vacuum induction melting (VIM), electroslag remelting (ESR), vacuum arc remelting (VAR), etc.
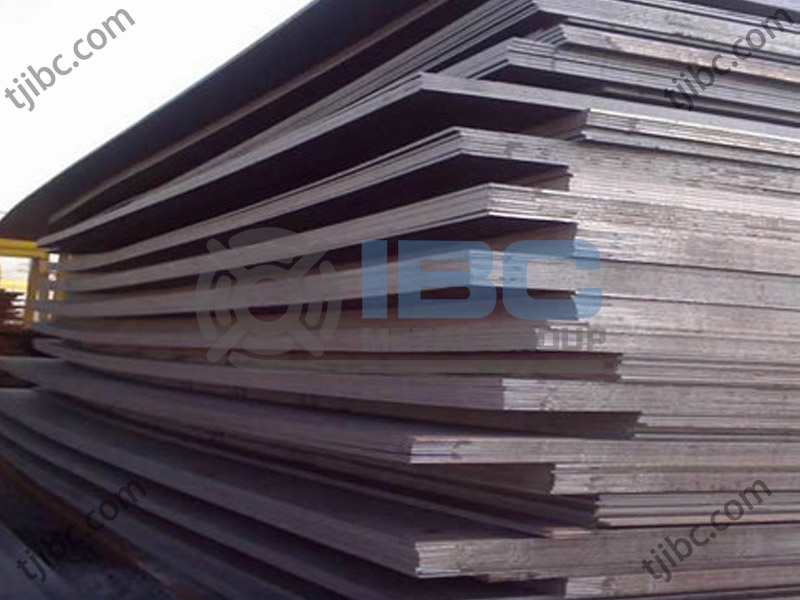
Contact with us today!