The A106 seamless pipe is made of high-quality carbon steel material with good high temperature resistance, high strength and stiffness, as well as excellent corrosion resistance. It can extend the service life under harsh environmental conditions. Its mechanical properties, including yield strength, tensile strength and elongation, meet the standard requirements.
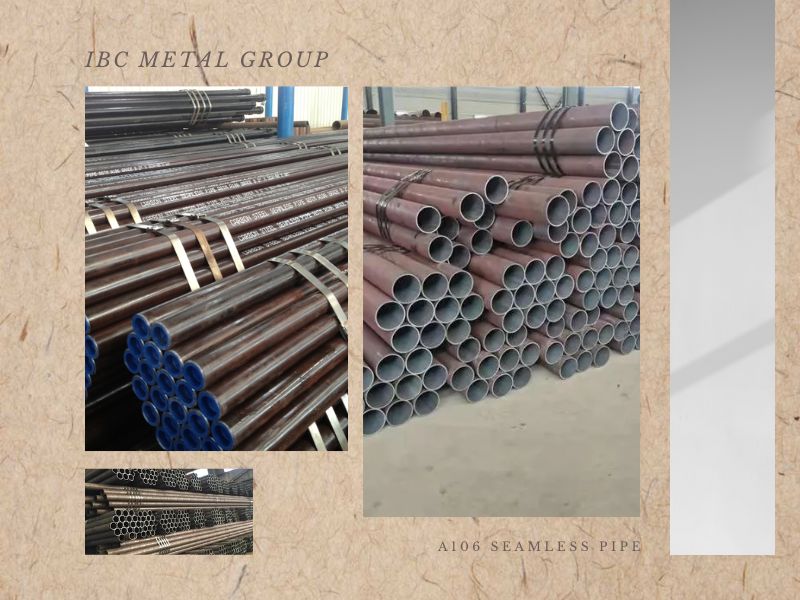
Performance Profile
First of all, this kind of pipe has excellent high temperature performance. And it can maintain stable performance even in high temperature environment, and its maximum use temperature can reach 600℃. This feature makes it ideal for high temperature operating environments.
Secondly, it has strong corrosion resistance and good resistance to most chemicals. This makes it work stably in a variety of corrosive environments and extends the service life of the pipeline.
In addition, the steel pipe adopts a seamless structure. It’s not only improves the strength and life of the steel pipe, but also makes the steel pipe have higher dimensional accuracy. It can meet the needs of various high-precision applications. At the same time, the inner and outer surfaces of the steel pipe are smooth. It is not easy to accumulate impurities, easy to clean and maintain, and further enhance its convenience in practical applications.
In terms of chemical composition, under the premise of meeting the maximum carbon content requirements, every 0.01% reduction in carbon content can allow it to increase the manganese content of 0.06% above the specified maximum manganese content. But the maximum must not exceed 1.35%. At the same time, the total content of the five elements Cu, Ni, Cr, Mo and V shall not exceed 1.00%. It ensures that the steel pipe has stable chemical properties and mechanical properties.
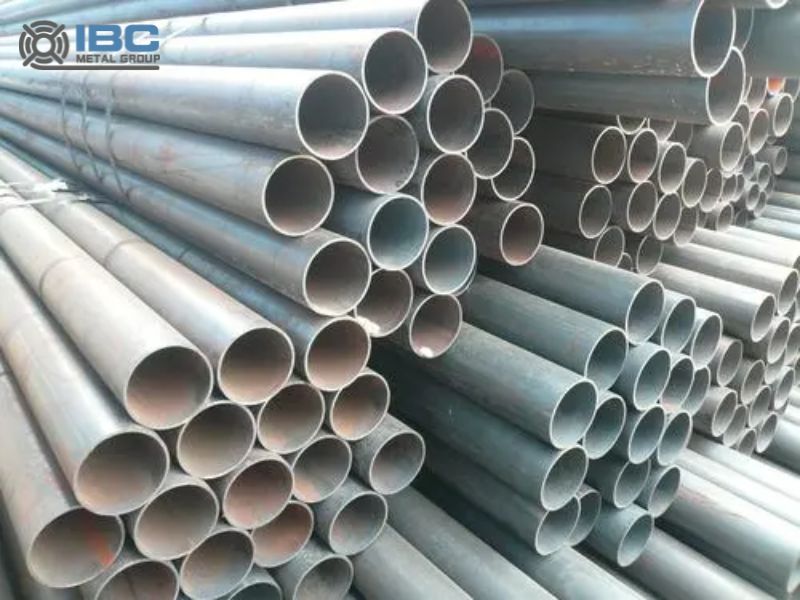
Manufacturing Process
Material selection: First of all, the selection of high-quality carbon steel as raw materials to ensure that the quality and performance of pipeline materials meet the standards.
Cutting: The selected raw material will be cut into the appropriate length of the tube blank, in order to facilitate subsequent processing.
Pre-treatment: Pre-treatment of the cut pipe blank, including straightening, rust removal and other operations. This can ensure the surface quality and accuracy of the pipe material.
Rolling: The pre-treated tube billet is sent to the rolling mill for rolling. And the tube with a certain shape and size is formed through the rolling process of multiple passes.
Sizing: During or after rolling, workers calibrate the outer diameter and wall thickness of the pipe to meet predetermined standards.
Heat treatment: Heat treatment of the pipe after rolling and sizing to eliminate internal stress and improve the mechanical properties and corrosion resistance of the pipe material.
Finishing: After the heat treatment is completed, the pipe is finished to remove the surface oxidation. Burr and other defects to ensure that the surface quality of the pipeline material meets the requirements.
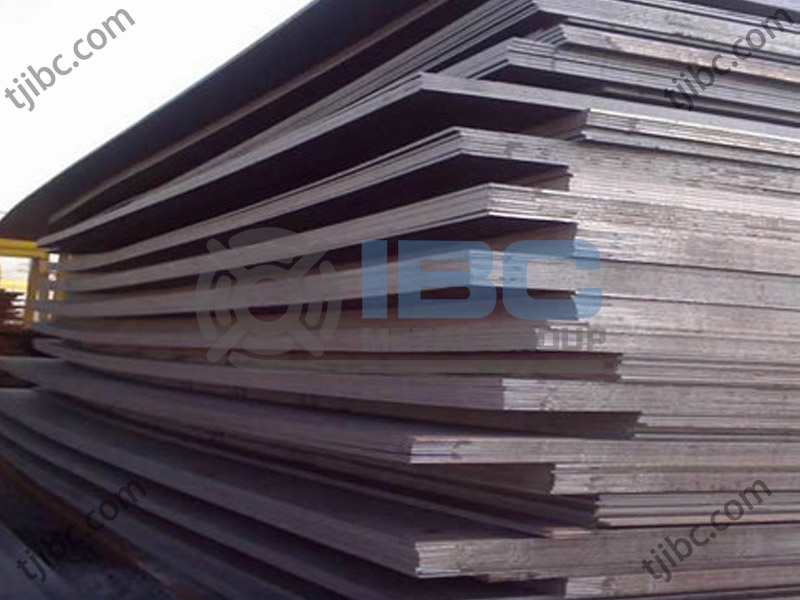
Contact with us today!