The application fields of high tensile plate are very wide, mainly including construction, Bridges, automobiles, ships and machinery manufacturing. In the manufacture of large ships, this steel plate is widely used because of its excellent strength and toughness. In addition, Bridges, power plant equipment, high-pressure boilers, high-pressure vessels, rolling stock, lifting machinery, mining machinery and other large welded structural parts are also often used as key materials.
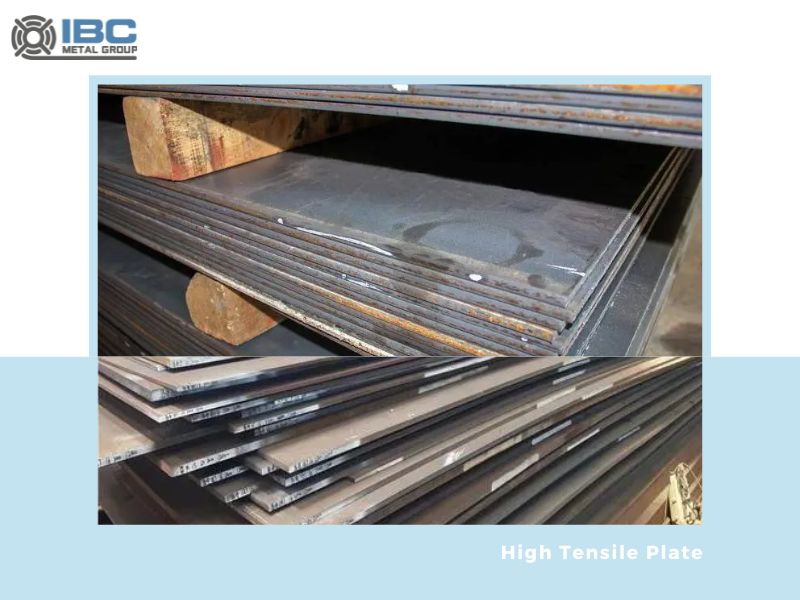
Performance Feature
In terms of mechanical properties, high tensile plate shows good toughness and ductility. Under load, even if the yield limit is exceeded, it can continue to deform and absorb energy, effectively avoiding fracture. This characteristic makes it have better shock resistance and can protect people and building structures.
The steel plate also has wear resistance and corrosion resistance. The specially treated surface makes it resistant to erosion in harsh environments, especially in Marine, coastal and other environments, where corrosion resistance is particularly important. This makes the steel plate has a wide range of application prospects in shipbuilding, petrochemical and other fields.
In addition, it has impact resistance and is resistant to impact and extrusion, providing higher safety performance. Therefore, the automotive field is also inseparable from its figure. It can make car bodies, frames and so on. It can improve the safety and fuel efficiency of vehicles.
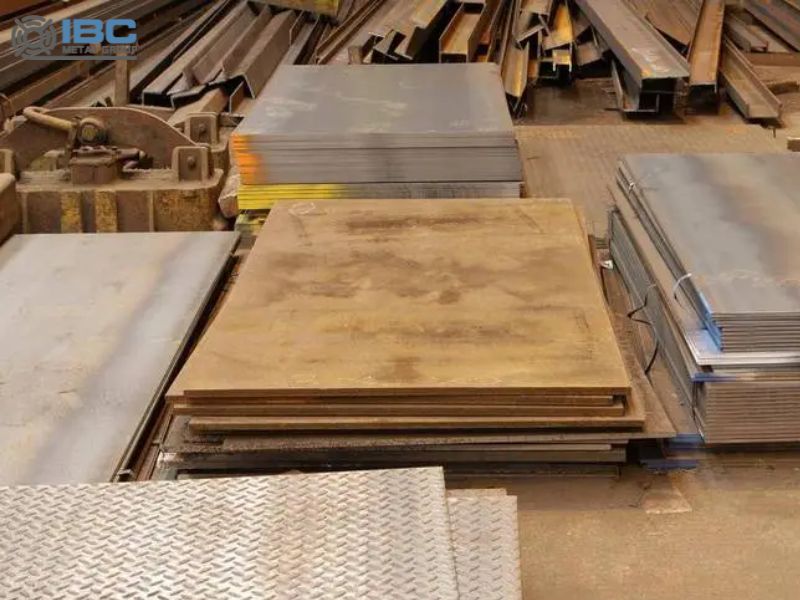
Welding Process of High Tensile Plate
1. Choose the right welding method
Its welding methods are mainly argon arc welding, submerged arc welding, manual arc welding, CO2 gas welding and so on. When selecting the welding method, the worker should comprehensively consider the steel plate material, thickness, weld shape and position and other factors to ensure the best welding effect.
2. Prepare
Clean the surface of the steel plate: ensure that the welding area is free of oil, rust and other impurities to improve the quality of welding.
Select the right welding electrode: Select the right welding electrode according to the steel plate material and thickness to ensure the stability and quality of the welding process.
Preheating: For thick or special high-strength steel plates, it is generally necessary to preheat them before welding to reduce their cold brittleness and reduce cracks and deformation during welding.
3. Welding operation
Set welding parameters: According to the selected welding method and steel plate characteristics, adjust the welding current, voltage, welding speed and other parameters to ensure the stability of the welding process and weld quality.
Welding: During the welding process, maintain a stable distance and Angle between the welding electrode and the steel plate, control the welding speed and temperature, and avoid welding defects. For thicker steel plates, multi-pass welding methods can be used for fractional welding to avoid overheating and brittle fracture.
4. Post-processing and inspection
Post-treatment: After the welding is completed, clean and trim the weld, remove welding slag and splash, and make the appearance of the weld clean.
Inspection: Quality inspection of the weld, including appearance inspection, non-destructive testing and mechanical property testing. It can ensure the quality of the weld meets the requirements.
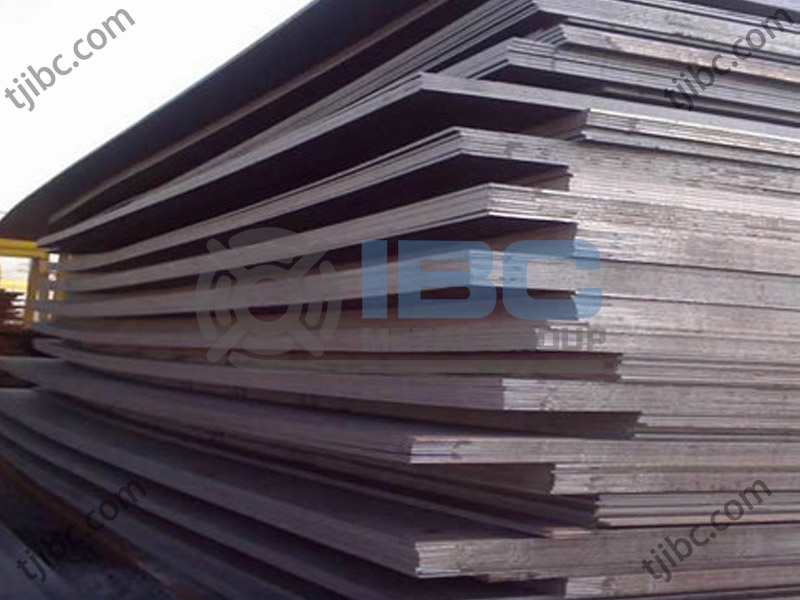
Contact with us today!