The automotive industry has entered a stage of high-quality development. IBC Group through the analysis of the organization and performance of high-strength steel materials used in automobiles, it can be seen that ZAM coated automobile plates have higher machinability and corrosion resistance.
High Strength Steel Market Analysis
1. Hot formed steel
Thermoformed steel is mainly used for safety components such as A, B, C columns and internal anti-collision rods of automobiles. Based on the lightweight and high strengthening requirements of automobiles, the amount of hot bending steel parts for automobiles will reach 1 billion in 2025, with considerable prospects.
The current market demand for hot-formed steel is about 1.2 million tons/year. Among them, the coated plate is about 800,000 tons/year, and the bare plate and galvanized plate are about 400,000 tons/year. There are 6 production lines of aluminum-silicon coated hot-formed steel in China, with an annual supply capacity of more than 1 million tons. And the total production capacity exceeds market demand. Hot formed steel specifications are as follows:
The thickness is 0.8mm^2.65mm(some models use pickling hot formed steel, the maximum thickness is 3.5mm). Among them, 1.0mm 2.0mm demand accounts for 90%. The width is.700mm to 1800mm. Among them, the three width specifications less than 1400mm, 1400mm~ 1600mm and greater than 1600mm account for 1/3.
2. Cold-formed advanced high-strength steel
Cold-formed advanced high-strength steel is strengthened by phase change. And there are two phase steel (DP), martensitic steel (MS), compound phase steel (CP), quenched and divided steel (Q&P). Among them, the amount of DP steel is the largest. And the amount of QP steel is less than 100,000 tons/year, mainly cold-rolled QP steel.
Dual-phase steel, multiphase steel, QP steel, martensitic steel with tensile strength above 780MPa and hot-formed steel with tensile strength above 1300MPa after hot forming have been applied in batches.
ZAM Coated Automobile Plates Market Analysis
1. Usage in the automo tive field
Compared with Z100, ZAM70 coating has better formability and better corrosion resistance. Zinc-aluminum-magnesium coating has excellent plane corrosion resistance, notch corrosion resistance, cup corrosion resistance, bending corrosion resistance, atmospheric corrosion resistance, coating performance. In particular, it has excellent resistance to dezinc dust. This can reduce the stamping interruption and loss caused by zinc powder pollution of stamping equipment, and improve the stamping efficiency of automobile plants. Automobile zinc aluminum magnesium paint instead of pure zinc paint, the weight can reduce 1~ 3kg. So it is the next generation of automotive protective coating materials.
2. Requirements of different specifications
IBC Group has the production of zinc aluminum magnesium coating thickness 0.45mm^ ~ 2.3mm, width 900mm^~ 1850mm, our product specifications can basically cover the interior and exterior plate parts for automobiles.
The market demand ratio of different width specifications is as follows:
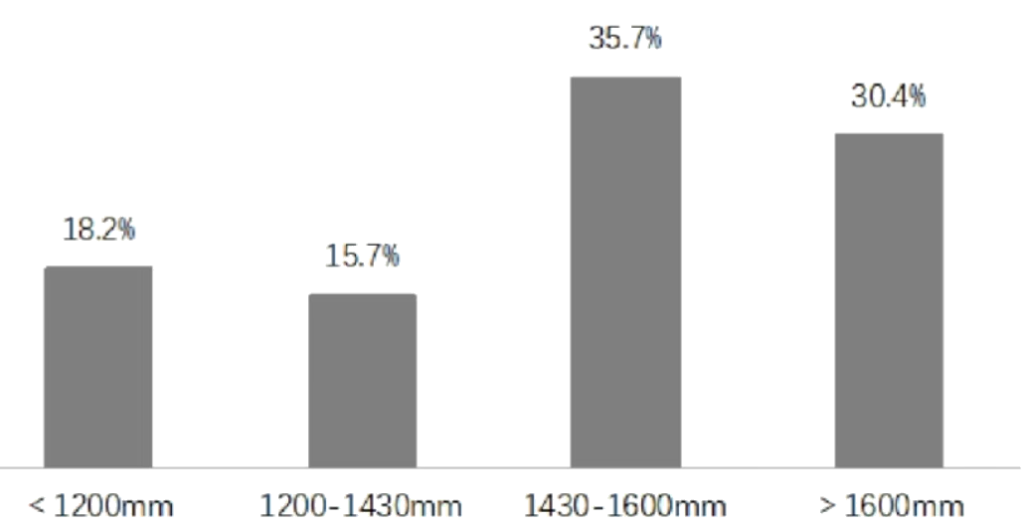
In brief, ZAM coated automotive plate is new type of corrosion resistant steel plate. ZAM coating has stronger corrosion resistance than traditional galvanized sheet. It is generally considered to be the leader in the first generation of zinc aluminum magnesium coating products. Its corrosion resistance is 10 times that of the general hot-dip galvanized coating. And in a strong corrosion environment, its corrosion resistance is 6 times higher than other coatings. ZAM coating not only has strong corrosion resistance, but also has high hardness. Its Vickers hardness is 140 ~ 160HV, and it has better resistance to scratching and repeated friction. These characteristics make ZAM coated automotive plates suitable for extremely harsh application environments.
Factory direct sales, sufficient inventory, support customization, IBC Group welcome new and old customers to consult.
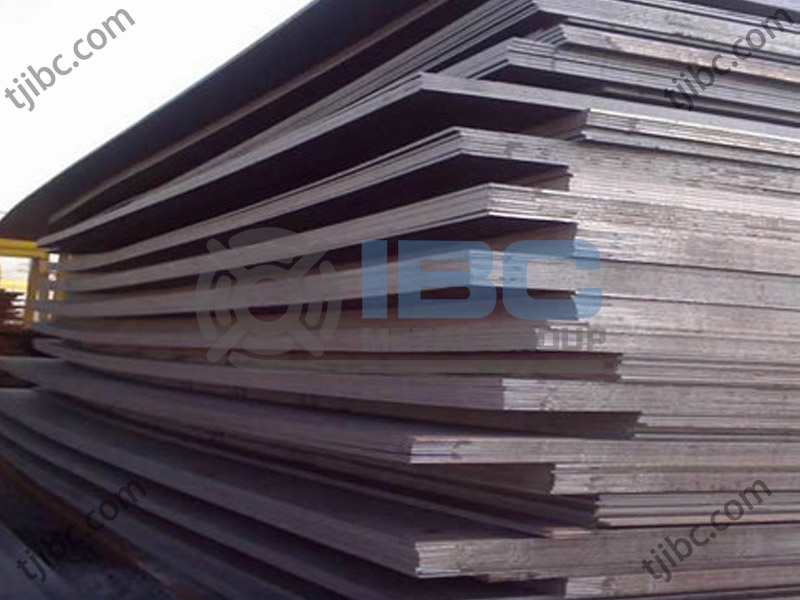
Contact with us today!