The Importance Of Emulsion In Cold Rolling Process
1. Strengthen lubrication in the cold rolling process
Its mechanism is mainly based on the emulsion can form a layer of isolation film, effectively reducing the direct metal contact between the metal strip and the roll. This isolation film not only reduces the coefficient of friction, but also disperses the heat and stress generated during the rolling process. Thus prevent the damage of rolling strip and roll.
In addition, the lubrication of the emulsion also helps to improve the surface quality of the strip. This reduces surface defects such as scratches and pits that occur during the rolling process. Thus improving the overall quality of the final product.
2. Improve cooling effect
The cooling effect of the emulsion is achieved through the liquid film formed on the surface of the roll and the strip. This liquid film can effectively absorb and transfer heat. In the process of high speed rolling, the strip and the roll will generate a lot of heat. If the heat is not dissipated in time, it will lead to thermal damage of the metal structure. Such as overheating caused by grain boundary oxidation and strength reduction.
The cooling effect of the emulsion not only protects the microstructure of the metal, but also maintains the stable operation of the rolling mill. This prevents equipment failure due to excessive temperature.
3. Comprehensive impact
The properties of the emulsion, including its viscosity, pH value, emulsification stability, etc., directly affect the efficiency and quality of the process.
High-performance emulsions provide better lubrication and cooling. This not only makes the metal strip in the rolling process more smooth, reduce production interruption, but also can improve the yield and output. In addition, the high quality emulsion reduces mill wear and maintenance costs. This extends the service life of the equipment and reduces long-term operating costs. By optimizing the performance and application of the emulsion, the economy and reliability of the entire process can be significantly improved.
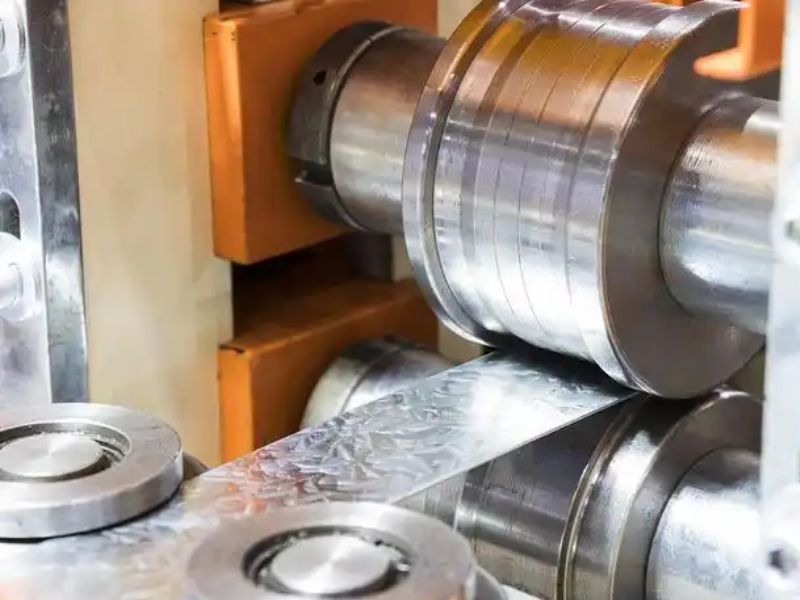
Influence Of Emulsion Performance Parameters On The Surface Quality Of Steel
1. Type and concentration of emulsion
In the cold rolling process, the main function of the emulsifier is to form an effective lubricating film between the steel strip and the roll. This reduces friction and wear caused by direct contact, thereby protecting the surface quality of the steel strip.
Emulsifiers can be divided into three basic types: cationic, anionic and non-ionic. Each type has different lubrication and stability properties due to its molecular structure and polarity.
2. Relation between pH value and steel surface state
The control of pH value is crucial in the application of emulsions. It directly affects the surface state and overall quality of the steel strip. During the cold rolling process, workers should keep the pH of the ideal emulsion at neutral or slightly alkaline. Usually between 7 and 9. pH in this range helps protect steel from chemical corrosion while optimizing lubrication.
When the pH of the emulsion is too low, that is, when it becomes acidic, it may accelerate the corrosion process on the steel surface. The acidic environment causes metal ions on the steel surface to dissolve, forming tiny corrosion spots that not only affect the appearance of the material, but may also weaken the structural integrity of the material.
Steel strips exposed to acidic conditions for a long time are prone to subtle corrosion marks or pitting. It may become the starting point of cracks in subsequent applications, seriously affecting the service life and safety of the material.
3. The influence of viscosity on surface finish
Viscosity is the key index of emulsion performance. It has a direct effect on the formation and maintenance of the lubrication film. And it also plays a decisive role in the surface finish of the steel strip. The appropriate viscosity ensures that the emulsion forms a continuous and uniform lubricating film on the steel surface. This is the basis for improving cold rolling efficiency and surface quality.
Too low viscosity of emulsion will affect the continuity and uniformity of lubrication film. In the process of high-speed rolling, the thin and unstable lubricating film is easy to crack due to friction and pressure. It increases the probability of direct contact between the steel strip and the roll.
This not only causes excessive wear on the roll and steel surface, but may also create scratches or other defects on the surface of the steel strip. This can seriously affect the surface finish of the product.
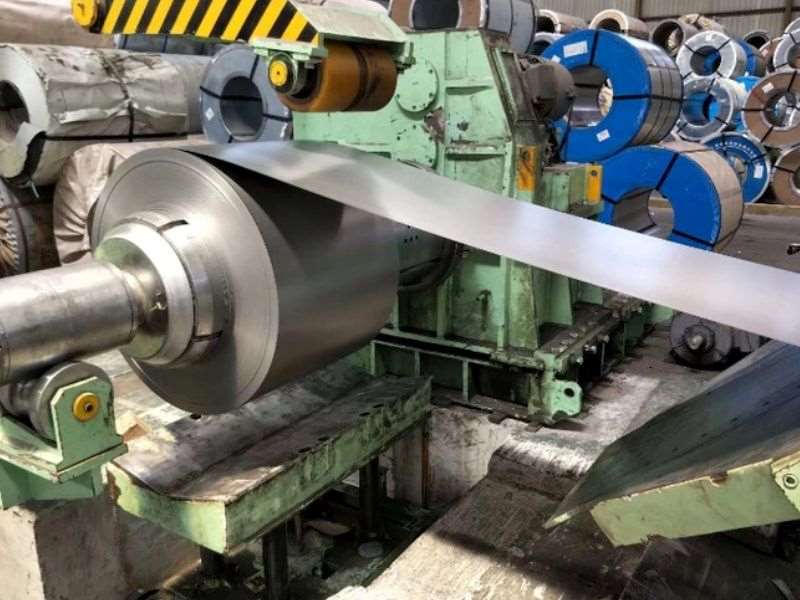
Optimization Of Emulsion Properties To Improve Mechanical Properties Of Steel
1. Improve tensile strength and elongation
Optimizing the formulation of the emulsion can significantly improve the tensile strength and elongation of the steel. In the process of cold rolling, good lubrication conditions can effectively reduce the surface and internal microscopic defects of the material. And these defects are often the main cause of material fracture.
When the emulsion forms a stable and uniform lubrication film on the surface of the roll and steel strip, friction can be greatly reduced. Thus, the tensile and compressive stress of the steel strip in the rolling process can be reduced. In addition, the optimized lubrication effect also helps to complete the deformation of the steel strip under low internal stress. This is essential to improve the plasticity and elongation of the material, allowing the steel to withstand greater deformation without breaking.
2. Improve hardness and wear resistance
In the cold rolling process, the emulsion not only plays the role of lubrication and cooling, but also has a direct impact on the hardness and wear resistance of steel. By precisely controlling the formulation of the emulsion, especially the type and concentration of additives, the surface properties of the steel strip can be significantly improved.
In the rolling process, proper lubrication can effectively reduce the direct friction between the metal surface and the mill. This not only reduces heat generation, but also prevents surface damage and uneven hardening due to high temperature and pressure.
Uniform hardened layer is the key to increase the hardness of steel. Because it ensures the consistency of the overall structure and performance of the material, it enhances its ability to resist deformation and fracture.
3. Enhance fatigue resistance and overall performance
Continuous performance optimization not only affects a single mechanical property, but also improves the overall performance of the steel, especially fatigue resistance. In rolling and subsequent applications, materials are often subjected to periodic loading.
The optimized emulsion ensures stable lubrication and cooling throughout the rolling process. This helps to reduce the formation of microscopic cracks due to stress concentration. Reducing the formation of these microscopic cracks is the key to improve the fatigue resistance of steel. Because these cracks are the main starting point of fatigue failure.
Therefore, by improving the formulation of the emulsion, not only the individual properties of the material, such as hardness and strength, but also its overall durability and safety in complex stress environments are greatly improved.
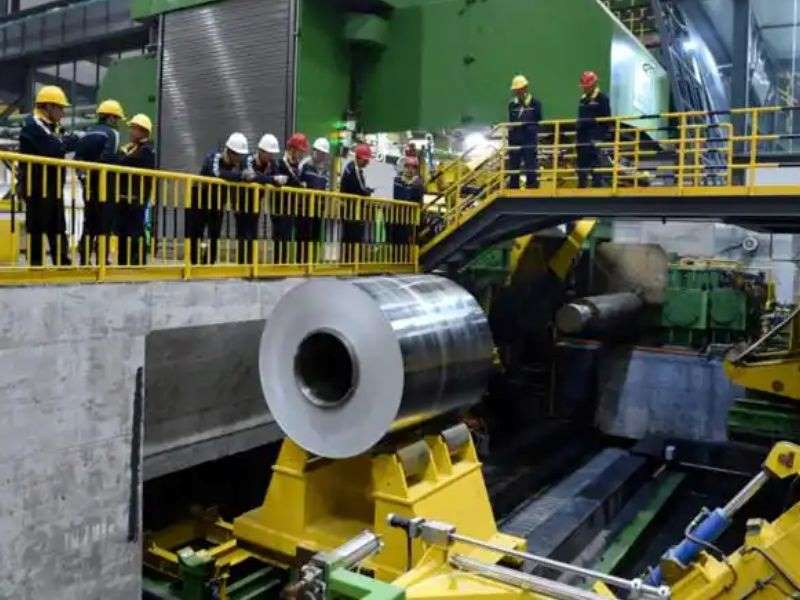
The Future Development Direction Of Emulsion Performance Optimization
1. Develop environmentally friendly emulsion formula
With the increasing global awareness of environmental protection and the strict enforcement of relevant regulations, the environmentally friendly formulation of emulsion has become the focus of future research. Currently, many emulsion formulations use certain chemicals.
For example, some organic solvents and heavy metal additives may have adverse effects on the environment.
Therefore, the development of harmless or less harmful alternative ingredients, such as plant-based and biodegradable emulsifiers, is the key to achieving more environmentally friendly emulsions. In addition, optimizing the production and use of the emulsion to reduce energy consumption and waste generation is also an effective way to improve its environmental performance.
2. Adjust the formula to meet the diverse needs of steel
The diversification of steel production and the improvement of quality standards put forward higher requirements for the performance of emulsion. Different steel types and cold rolling processes have different dependencies and requirements on the lubrication and cooling properties of the emulsion. For example, special materials such as high-strength steel and ultra-thin steel strips pose higher challenges to the shear resistance and thermal stability of emulsions.
For this reason, the formula of the emulsion must be adjusted according to the characteristics of different materials. For example, by changing the type and concentration of emulsifiers or by adding specific performance improvers. This ensures optimal performance in all rolling conditions.
3. Dual challenges of technology and market
In the development process of emulsion, the dual challenges of technological innovation and market demand are inevitable. In terms of technology, the continuous improvement of analysis and testing technology makes the evaluation of emulsion properties more accurate, and also provides stronger data support for the scientific formulation of emulsion.
However, how to effectively translate these technological innovations into market-acceptable products is up to enterprises. Find the right balance between R&D and marketing.
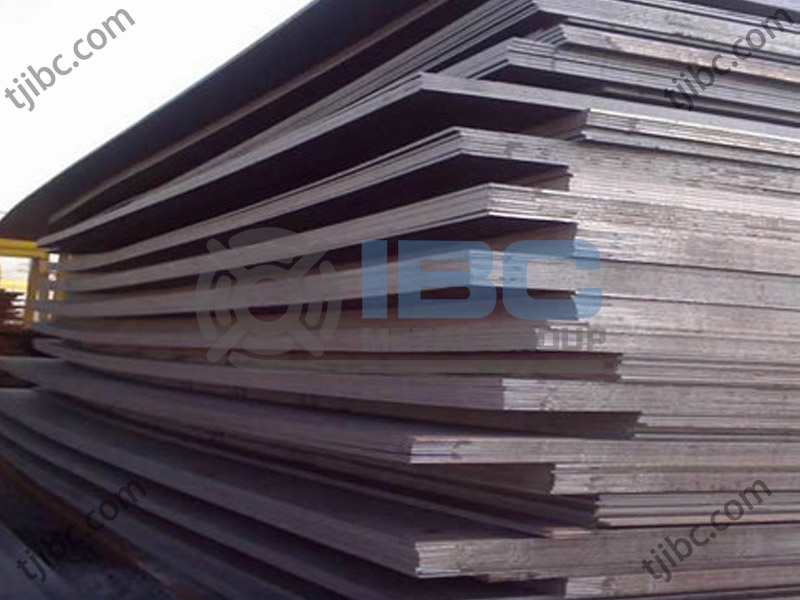
Contact with us today!