Importance Of Heat Treatment Process
The role of heat treatment process in steel production is very obvious, which will directly affect the properties of steel. With a series of operations, the internal structure of the steel can be optimized, and the physical and mechanical properties of the steel can also be optimized.
1. Improve the mechanical properties of steel
Any steel machinery needs to have high strength, hardness and wear resistance. In this way, you can better cope with the harsh work environment. Heat treatment is the focus of improving these properties of steel. Take quenching, for example, by heating steel above a critical temperature and cooling it quickly. In this way, the steel retains sufficient hardness while also having good toughness to adapt to complex and changing working conditions.
2. Improve the chemical properties of steel
In the case of stainless steel, the corrosion resistance of steel can be improved by heat treatment. This ensures that the steel remains stable even in harsh environments. In addition, for magnetic steel, the heat treatment method can enhance its permanent magnetism. At the same time, normalizing is also a heat treatment method, which can refine the grain structure and cutting performance of steel, which is conducive to providing convenience for subsequent processing and use.
Traditional Heat Treatment Process Ⅰ – Annealing Process
Key steps in the annealing process include: First, workers need to slowly heat the steel to a predetermined temperature. The choice of temperature is very important, because it will affect the internal structural transformation and stress release of the steel. Slow heating ensures that the heat inside the steel is uniform, avoiding overheating or undercooling areas. This prevents temperature differences from causing uneven internal stresses.
Secondly, after reaching the predetermined temperature, the worker needs to keep the steel at that temperature for a period of time. The purpose is to allow the internal organization of the steel to have enough time to adjust and restructure. Especially for those internal stresses caused by rapid cooling or deformation during processing, the insulation process allows them to be gradually released and redistributed. At the same time, this stage can also make the internal grain of the steel grow and recrystallize, which can further soften the material.
Finally, the steel should be cooled at a suitable speed, too fast cooling is easy to produce new internal stress. And too slow may make the steel performance difficult to meet the expected standards.
Traditional Process Ⅱ – Normalizing Process
The normalizing process is not the same as the annealing operation. This heat treatment process requires first heating the steel to the appropriate temperature, usually higher than the annealing temperature, but below the melting point of the steel.
After reaching the target temperature, insulation should be carried out so that the inside of the steel is fully prepared. After the completion of insulation, the steel can not be cooled quickly, but should be cooled naturally. This mild temperature transition allows the internal structure of the steel to become more detailed and helps to improve its mechanical properties.
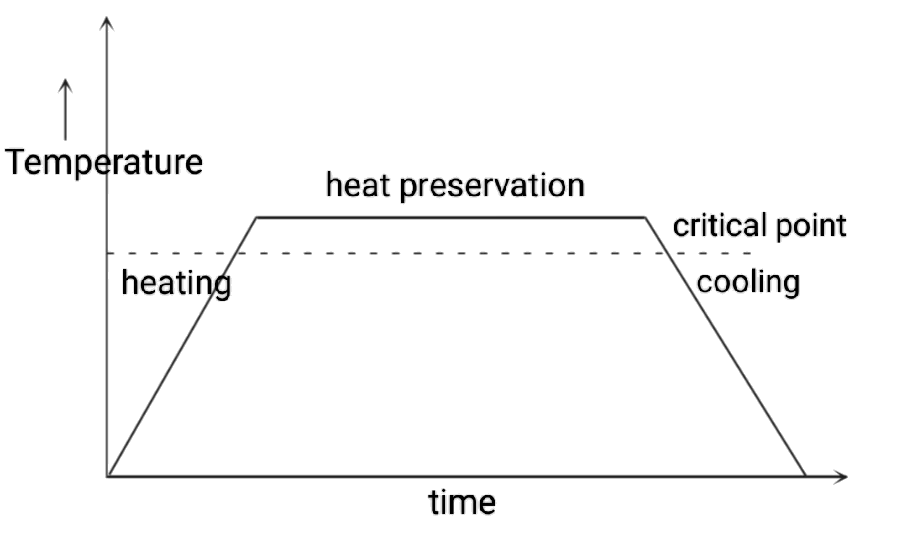
Traditional Process Ⅲ – Quenching Process
In the quenching process, the steel is first rapidly heated above the critical temperature. This critical temperature is the key point for the transformation of the internal structure of the steel, and the microstructure of the steel will change beyond this temperature. This requires a rapid and uniform heating process. It can ensure that the steel as a whole reaches the desired temperature state.
After the steel has been heated above the critical temperature, the next step is rapid cooling. The control of the cooling rate of this link is very important. This requires the relevant staff to accurately control the properties of the quenched steel to meet the expected standards.
New Heat Treatment Process Ⅰ – HVSQ
HVSQ technology is a new heat treatment process that has attracted much attention in recent years. Its unique processing method and excellent performance have attracted wide attention in the field of steel production. At the heart of this technology is a combination of rapid heating and rapid cooling to finely process steel.
In this process, the steel is quickly heated to the desired temperature, followed by a rapid cooling. This sharp temperature change will have a certain effect on the microstructure of steel, so that it forms a layer of ultrafine grain structure on the surface. The ultrafine grain structure has the characteristics of small grain size and uniform distribution. It can improve the hardness and wear resistance of steel. In addition, due to grain refinement, the resistance of the steel to wear and scratches will be enhanced. This can better maintain its original shape and properties, and can extend the service life of the steel during use.
Steel processed by HVSQ technology has a wide range of application prospects in many fields. In the automotive industry, for example, this steel enables the manufacture of more durable engine parts, drivetrain components or body structures. This improves overall vehicle performance and safety. In the manufacturing industry, it can produce high-precision tools, molds and so on.
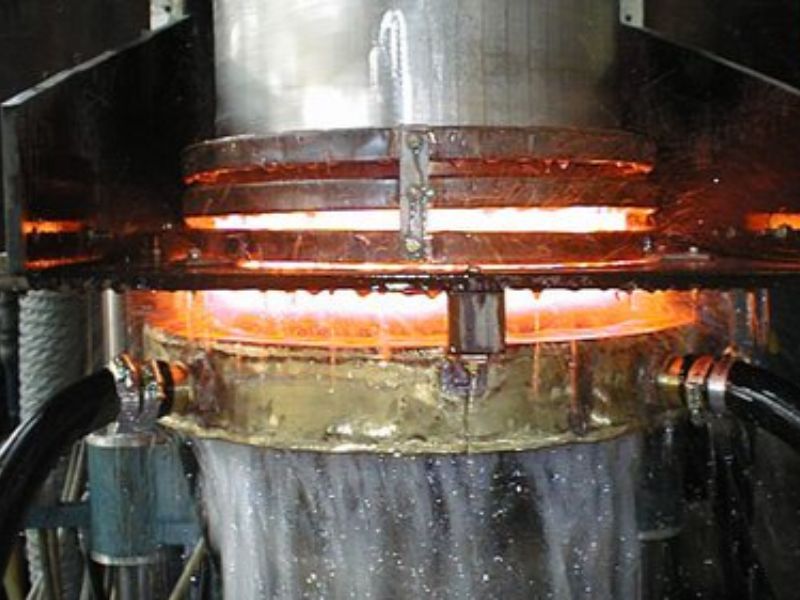
New Process Ⅱ – Laser Processing Technology
Compared with traditional heat treatment methods, laser heat treatment technology can show higher energy efficiency and processing accuracy. Previous heat treatment methods usually required workers to heat the entire steel. This not only consumes high energy, but also easily leads to uneven internal structure and performance of the steel.
Laser heat treatment can focus energy precisely on the area that needs to be treated. This avoids unnecessary heating of the entire steel and can greatly reduce energy consumption. In addition to the advantages of energy efficiency and machining accuracy, this technology can also improve the surface microstructure of steel.
Rapid heating and cooling by laser beam can fully refine the surface grain of steel. Thus, the fatigue strength and crack propagation resistance of steel can be improved. This shows that in harsh working environments, laser heat treated steel can also resist fatigue and crack generation, so as to maintain a longer service life of steel.
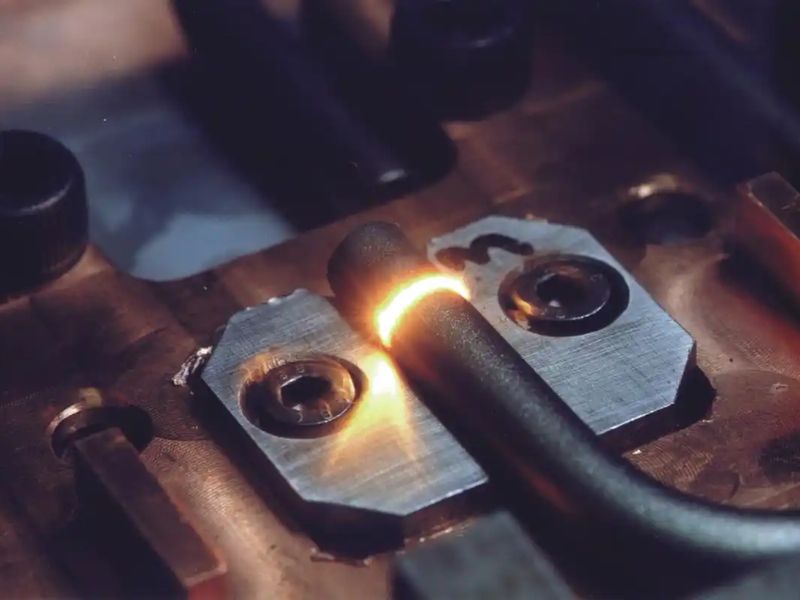
The Development Trend Of Steel Heat Treatment
First of all, green environmental protection is the main development direction of steel heat treatment in the future. On the basis of global climate change and increasingly serious environmental problems, reducing energy consumption and pollutant emissions in industrial production has become a top priority.
Heat treatment is an important part of steel production, which has great potential for energy saving and emission reduction. In future development, the plant should pay more attention to the use of clean energy and optimize heating and cooling methods. Thus reducing carbon emissions in the production process.
Second, the application of intelligent production in heat treatment process. With the rapid development of automation technology and artificial intelligence technology, it has become possible to realize intelligent control of heat treatment process. Through the introduction of intelligent sensors, data analysis and machine learning and other technical means, it is possible to monitor and adjust the temperature, time, atmosphere and other parameters in the hot steel processing process in real time.
In addition, intelligent production can also help steel production enterprises to achieve fine management, such as reducing human error, and then improve the stability of the process.
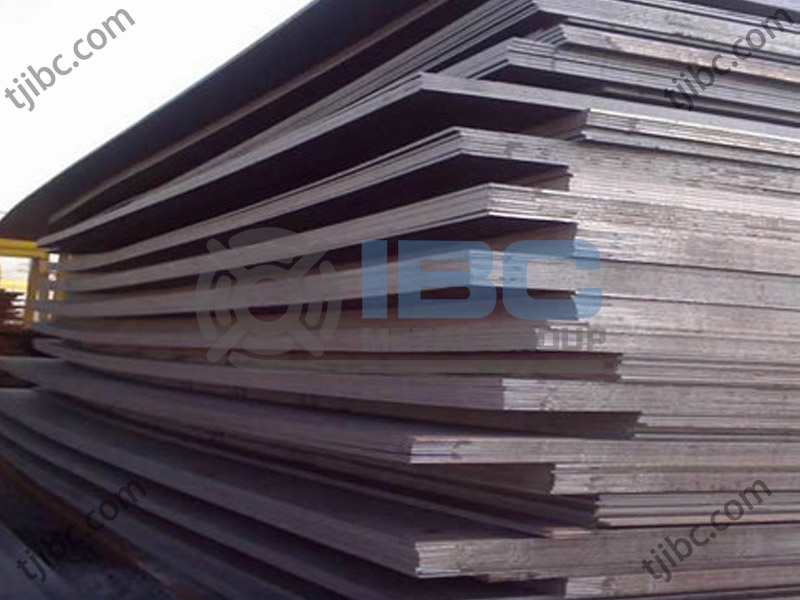
Contact with us today!