The wear resistance of metal refers to the ability of metal materials to maintain the integrity and function of their surfaces under the action of external forces such as friction, collision or wear.
This is a key mechanical performance index of metal materials, which is closely related to many factors such as hardness, strength, plasticity, toughness, crystal structure, temperature conditions, surface roughness and metallurgical defects.
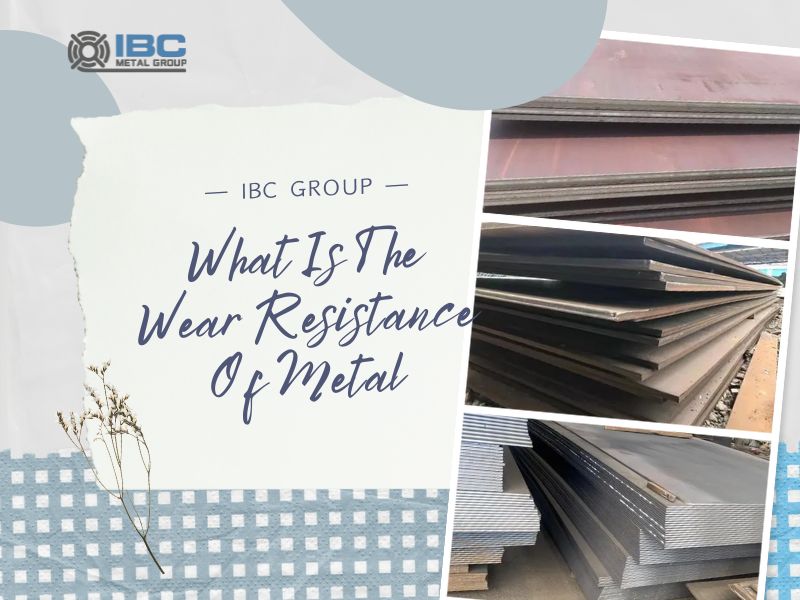
Steps of Metal Wear Resistance Test
1. Choose the right metal materials: according to the use of the environment and friction conditions, choose stainless steel, high carbon steel, alloy steel and other materials.
2. Sample preparation: The selected metal material is processed into a standard sample shape and size for subsequent wear testing.
3. Choose the wear test method: According to the specific test needs, choose the appropriate wear test method. Common wear testing methods include rotary wear, sliding wear, impact wear and so on.
4. Wear test: Wear test is carried out on the sample under the selected test conditions. During the test, the friction coefficient, wear amount, wear depth and other parameters can be recorded for subsequent analysis.
5. Analyze the test results: process and analyze the wear test data, calculate the wear rate, wear life and other key indicators to evaluate the specific performance of the metal.
6. Optimize materials and processes: According to the test results, optimize metal materials and processing processes.
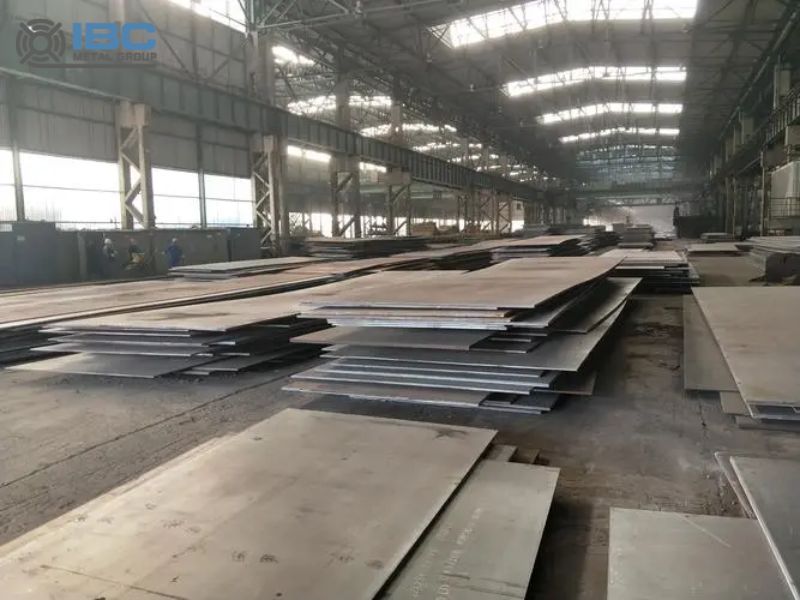
What kind of metal has high wear resistance?
1. Tungsten alloy: with high density, high hardness and good wear resistance, it can still maintain its strength and hardness under high temperature conditions. Therefore, it is widely used in aviation, aerospace and military fields.
2. High manganese steel: such as Mn13 steel plate, has a wide range of applications in mining machinery, agricultural machinery, cement building materials and other fields. Equipment in these fields often need to work in harsh environments, and the good performance of high manganese steel ensures the long-term stable operation of equipment and reduces maintenance costs.
3. Other alloys: such as titanium alloy, nickel-based super alloy and cobalt-based alloy, etc., these alloys not only have high strength and good corrosion resistance, but also show good oxidation resistance under high temperature conditions, so they are widely used in aviation, aerospace, chemical and other fields.
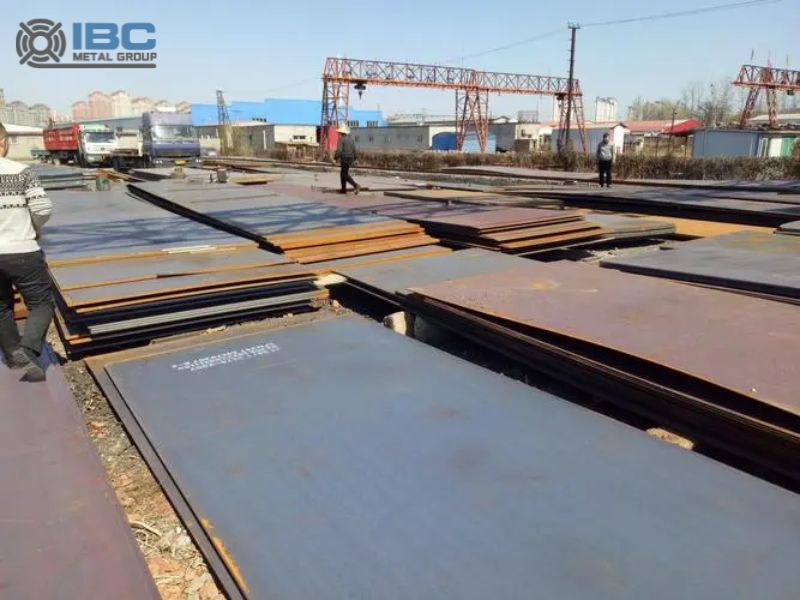
Advantages of IBC Group
1. Supply chain integration ability:
IBC Group has a strong supply chain integration ability to effectively connect upstream suppliers and downstream customers to ensure a stable supply of steel and efficient circulation.
We have established a sound supply chain management system. This allows for transparency and visibility in the supply chain, reducing operational costs and increasing efficiency.
2. Diversified product portfolio:
IBC Group offers a diverse portfolio of steel products to meet the specific needs of different industries and customers.
We also have many types of steel products, including different types of alloy steel, stainless steel, carbon steel, etc., to meet the diverse needs of customers.
3. Market development ability:
IBC Group has a strong ability to expand the market and is able to find new business opportunities and development space in domestic and foreign markets.
We have also established a comprehensive sales network and distribution channels to cover a wider range of customer groups and market areas.
4. Professional technology and quality assurance:
IBC Group has a professional technical team and quality management system to provide high-quality products and services.
Through strict quality control and inspection processes, the Group ensures that the steel products supplied meet the relevant standards and customer requirements.
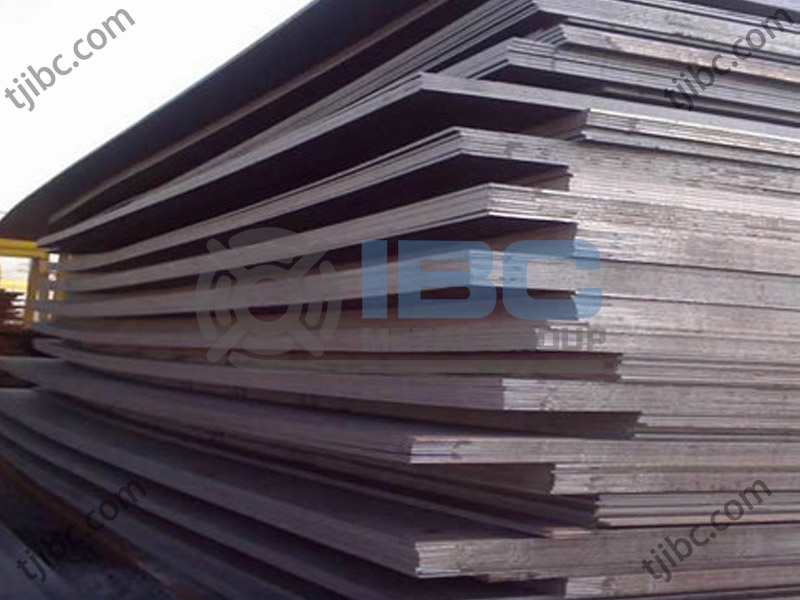
Contact with us today!