Anti-corrosion for steel pipe is very important . We usually use steel pipe for fluid and gas transportation. Pipelines are often buried in the ground or underwater or overhead. Therefore, corrosion resistance of steel pipes is very important. Following, let’s take a look at the anti-corrosion process of spiral steel pipe. The pipeline anti-corrosion method method divided into 3 types according to the application and anti-corrosion process.
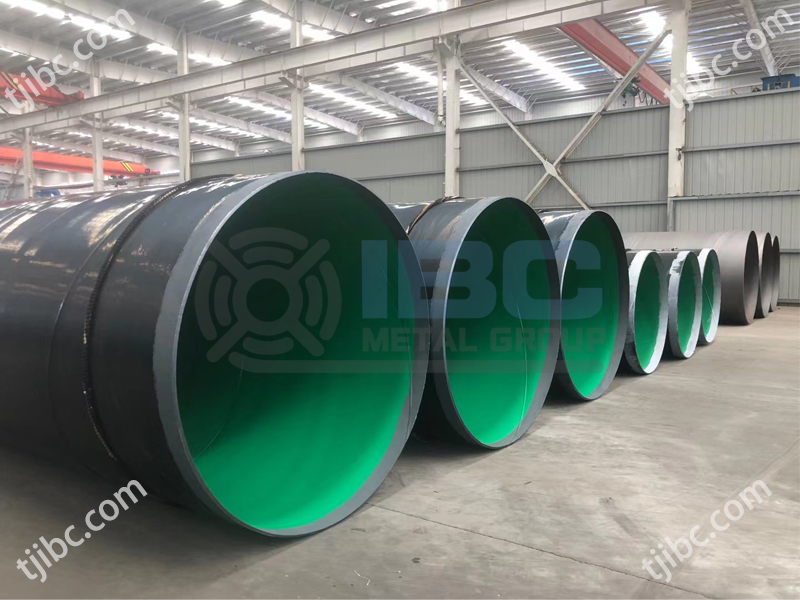
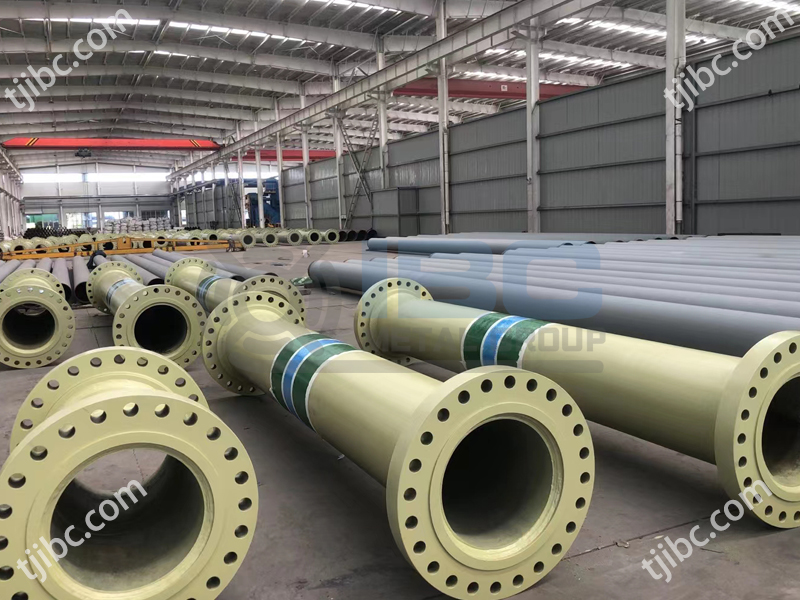
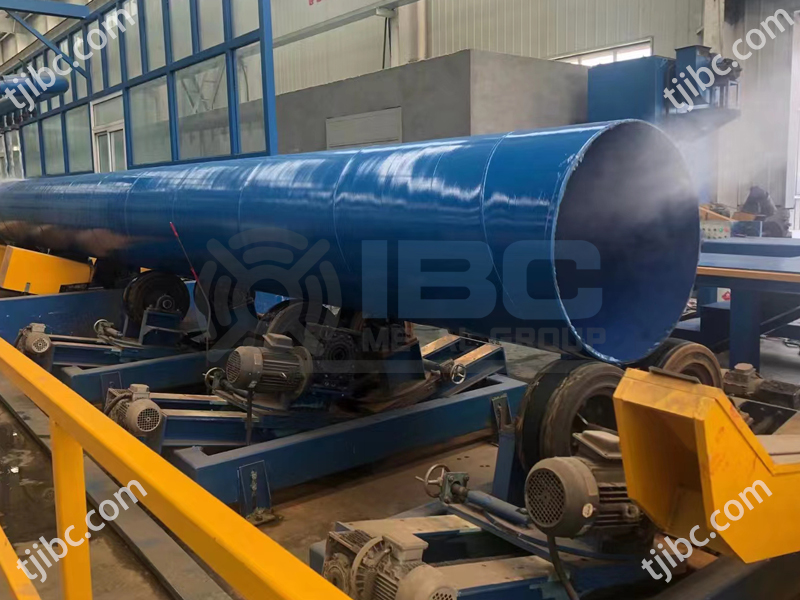
IPN8710 Anti-Corrosion For Steel Pipe
IPN8710 corrosion is widely used for tap water supply and water pipeline service due to its film’s chemical inertness. This anti-corrosion technology is an effective protection against a variety of corrosive media, such as acids, alkalis, salts, oxidisers and water vapour. Additionally, it has a dense structure that provides outstanding resistance to acid salt corrosion; the coating also offers excellent water permeability combined with great toughness and adhesion properties.
Primer of IPN8710
composed of polyurethane, polyethylene, modified epoxy resin, non-toxic anti-corrosion pigments, additives, etc., room temperature curing to form interpenetrating networks, coating structure is dense, acid, alkali, salt, rust resistance, strong adhesion of water supply pipe wall anti-corrosion primer.
Topcoat of IPN8710
composed of epoxy resin, rubber, resin modification, non-toxic anti-corrosion pigments, additives, etc. Excellent chemical resistance, non-toxic, anti-microbial corrosion, anti-corrosion protection of water pipeline wall.
2PE/3PE Anti-Corrosion For Steel Pipe
2PE/3PE anti-corrosive structure integrates the optimum features of the steel plate, epoxy powder electrostatic spraying glue and polyethylene overload winding. As a result, it enhances the entire anti-corrosion quality of the pipeline. It offers remarkable protection from chemical corrosion, cathodic stripping and mechanical damage. 3PE and TPEP are typically found in gas transmission and water distribution systems, yet these two approaches are rather costly due to their excellent results.
Plastic-coated
Plastic-coated steel pipe is the most widely used anti-corrosion process at present. The application fields include water supply and drainage, fire sprinkler and mining, with low maintenance cost and long service life.
FBE epoxy powder corrosion
FBE epoxy powder anti-corrosion structure: electrostatically spraying epoxy powder on steel parts, forming a film. Among the advantages of the coating are its simplicity, cleanliness, good impact resistance, bending resistance, temperature resistance, etc.
Coal tar epoxy anti-corrosion
Coal tar epoxy anti-corrosion structure: made of epoxy resin + coal tar asphalt filler + anti-corrosion coating, coated with glass cloth on the steel surface to strengthen the coating formation, commonly used in the inner wall of the pipeline anti-corrosion. Thickness 0.5 ~ 1.0mm.
High-density polyethylene sheath corrosion
High-density polyethylene sheathing anti-corrosion structure: The outer surface of the pipe is wrapped with high-density polyethylene material, which has high mechanical strength and excellent corrosion resistance, and can protect the steel from damage during transportation, installation, and use by external factors.
A number of factors need to be taken into account when selecting anti-corrosion methods for steel pipes, such as application fields, construction environments, and cost budgets. During the procurement process, you can contact us with any questions you may have regarding the anti-corrosion process. Based on the specific needs of customers, IBC (Tianjin) Industrial Co., Ltd can provide very detailed anti-corrosion solutions.
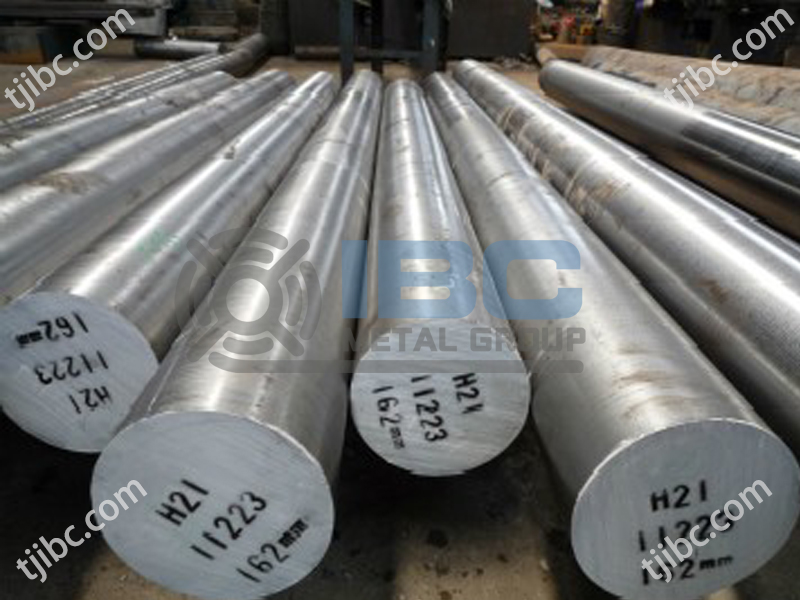
Contact with IBC Metal Group Today!