High carbon and high chromium tool steel:
With high hardness, high wear resistance and high heat resistance, suitable for manufacturing die, stamping die, stamping die and other high strength and high wear resistance requirements of the die.
Operating points:
Quenching: It usually needs to be quenched to obtain the required hardness and wear resistance. When quenching, the heating temperature and cooling speed should be strictly controlled to avoid excessive internal stress and cracks.
Tempering: The tool steel after quenching needs to be tempered to reduce internal stress and improve toughness and wear resistance. The choice of tempering temperature and time should be determined according to the specific requirements of use.
Grinding and polishing: It has high hardness and wear resistance, so special abrasives and tools need to be used when grinding and polishing to ensure the desired surface finish and precision.
Use and maintenance: During use, it needs to avoid excessive loading and impact to prevent damage and deformation. At the same time, regular cleaning, lubrication and maintenance to extend its service life.
High carbon and high alloy tool steel:
Also has high strength, high hardness and high wear resistance, suitable for manufacturing large die, stamping die, punching die and so on.
Main application areas:
Die: Used for stamping sheet metal, such as auto parts, home appliance shell, etc.
Stamping die: suitable for large-scale stamping operations, such as the production of mobile phone shell, metal containers and other parts.
Blanking die: Used for precise cutting and cutting of sheet metal, such as in the manufacture of precision parts.
Hot die: A die used to press heated metal billets into a specific shape during hot forging.
Hot extrusion die: Used to extrude metal at high temperatures to form strips, rods or tubes.
High temperature gripper: used to grip and position metal billets during hot forging.
Cutting tools: Manufacture cutting tools for trimming and cutting hot metal.
Aerospace: Manufacturing high-precision, high-wear parts, such as engine parts, aircraft structural parts, etc.
Automotive industry: Molds and tools for the manufacture of automotive engines, transmissions and other key components.
Energy industry: Molds and tools for the manufacture of oil and gas extraction and processing equipment.
High temperature alloy steel:
with its high heat resistance and high wear resistance, it is especially suitable for manufacturing high temperature molds, such as hot pressing molds and hot extrusion molds.
Production process (general steps) :
Composition design: Select the appropriate alloy elements according to the requirements of use, such as nickel, chromium, tungsten, molybdenum, cobalt, etc., design the alloy composition.
Raw material preparation: Prepare the required raw materials, such as pure metals, alloying elements or intermediate alloys, and clean them.
Smelting: The raw material is melted in a vacuum or protective atmosphere to obtain a uniform chemical composition and a pure alloy liquid.
Casting: The alloy liquid is poured into the mold to form alloy ingots or castings.
Heat treatment and processing: The ingot is heat treated to improve its structure and properties. Then, the structure and properties of the alloy are further adjusted by forging, rolling, heat treatment, etc., to obtain the desired shape and size.
Machining: Finishing the alloy after heat treatment and processing, such as turning, milling, grinding, etc., to obtain accurate dimensions and surface quality.
Testing and evaluation: mechanical properties testing, chemical composition analysis, metallographic structure inspection of finished products to ensure that they meet technical standards and requirements.
Surface treatment: According to the need, the surface treatment of the alloy, such as spraying, polishing, heat treatment, etc., to improve its oxidation resistance, corrosion resistance and service life.
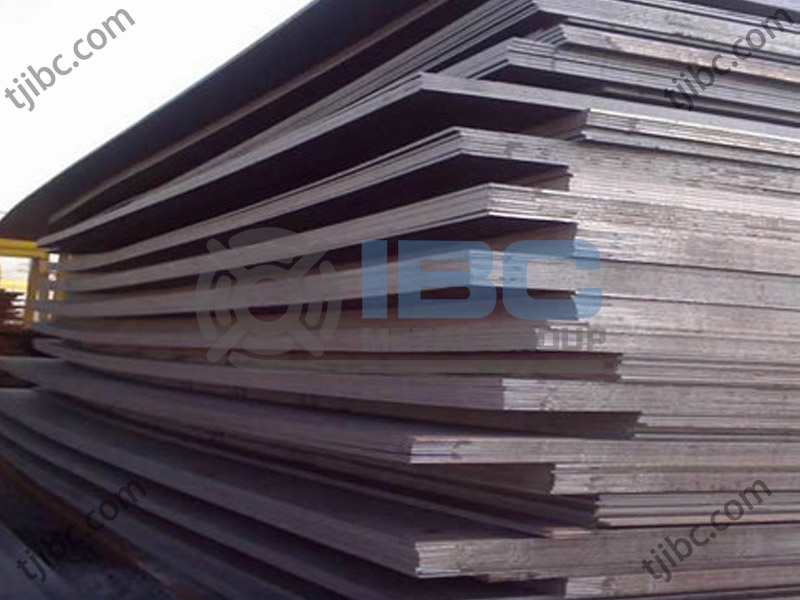
Contact with us today!