DIN1.2080 Cold Work Tool Steel Manufacturer & Supplier & Exporter
IBC Metal Group is specialized in provide DIN1.2080 Cold Work Tool Steel. We supply all kinds of special steel. Not only cold work steel, but also hot work tool steel, Plastic Mould Steel, High Speed Tool Steel, Alloy Structure Steel, Bearing Steel, Spring Steel and so on. High quality together competitive price make them suitable for your projects. IBC could supply cold work tool steel in round bar & flat bar. Specification according ASMT/AISI, EN, JIS, DIN, ISO, etc. For more information please contact with us today!
Supply Range of DIN1.2080 Cold Work Tool Steel
- Round Bar Ø (mm):
- Hot Rolled from Ø12~Ø50;
- Hot Forged: EAF-Ø50~Ø250; ESR-Ø50~Ø650;
- 2. Flat Bar (mm):
- EAF Thickness from 20~200, width from 80~610;
- ESR: Thickness from 20~450, width from 610 max;
Application
Widely used in hot forging die, punching die and making nuts, bolts and other parts of the stamping die. It is also the first choice for forming die, scissors, hot extrusion die, top rod and lower die seat.
Properties:
High temperature resistance, wear resistance, excellent machining performance, strong stability in heat treatment, temperature up to 650℃ still works well.
Forging of DIN1.2080 Cold Work Tool Steel
Pre-heat at 900-950°C then raise temperature to 1050-1100°C. Soak until uniformly heated. D3 tool steel is relatively hard at elevated temperature. Therefore, initial hammer blows must light and the temperature must not allow to fall below 1020°C until the metal begins to flow. Final forging should not be done below 900°C.
Annealing
D3 tool steel supplied in the annealed and machineable condition. Re-annealing will only necessary if the steel has been forged or hardened by the toolmaker. To anneal, heat slowly and uniformly to 900°C. Soak for three to four hours and allow to cool in the furnace to room temperature. Re-heat to 800-1040°C and again soak for three to four hours. Allow to cool in the furnace to room temperature.
Empering
Double tempering recommended. Tempering should do with the least possible delay after hardening, preferably when the tools are still hand warm. Select a suitable tempering temperature, bearing in mind the service requirements. Heat slowly and uniformly. When the component has reached the desired temperature, soak for at least one hour per 25mm of thickness. The second tempering should be a repetition of the first.
Martempering
Martempering is an alternative hardening procedure which may be used when suitable salt bath equipment is available. By this method internal strain, distortion and risk of quench cracking are reduced to the minimum. Pre-heat dry at 300-400°C. Pre-heat in salt at 800-850°C holding in the salt for ten minutes 25mm of ruling section. Raise to the hardening temperature of 950-980°C holding in the salt for ten minutes 25mm of ruling section. Marquench in salt at 230-250°C holding in the bath for five minutes 25mm of ruling section. Cool in still air. Tempering will be necessary.
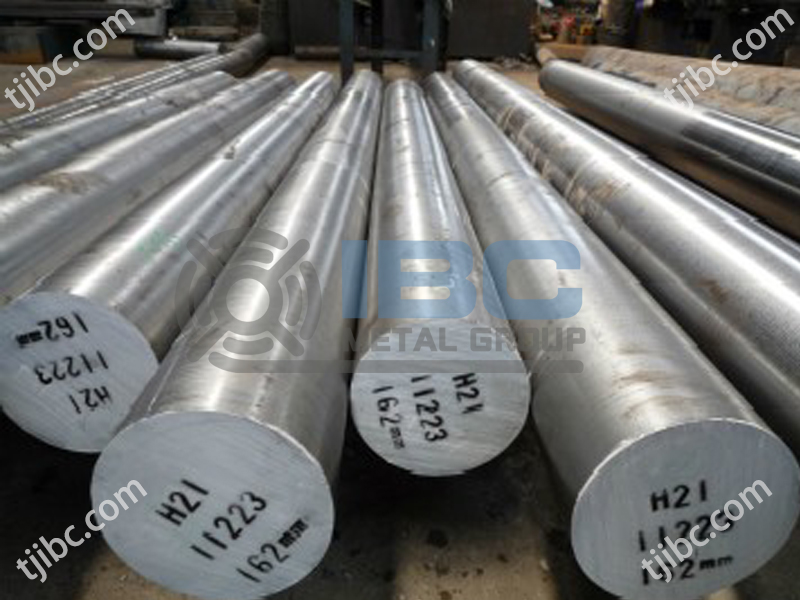
Contact us today!