Product Introduction
Common Aluminum Welding Wire Types:
S301, ER1100 Welding Wire
S331, ER5183 Welding Wire
S5356, ER5356 Welding Wire
S311, ER4043 Welding Wire
Technical data:
Type AWS | Chemical Composition(%) | ||||||||||
Cu | Si | Fe | Mn | Mg | Cr | Zn | Ti | Al | |||
Aluminum Alloy | YH-5356 | ER5356 | High strength, good corrosion resistance ability and commonality, and used for aluminum alloy TIG welding, especially for welding 5083 materials | ||||||||
≤ 0.10 | ≤ 0.25 | ≤ 0.40 | 0.5-0.2 | 4.5-5.5 | 0.05-0.2 | ≤ 0.10 | 0.06-0.2 | Rem |
In addition, depending on the alloy composition, this steel product page can be divided into many types. Such as pure aluminum wire, aluminum alloy wire and so on. Each type of wire has its specific chemical composition and mechanical properties and is suitable for different welding materials and welding conditions. In addition, it has different diameter and length specifications to meet the needs of different welding equipment and welding process.
Production Process | Aluminum Welding Wire
1. Melting and casting
Smelting:
The workers heated the aluminum in a stove and melted it.
They also add alloying elements as needed to adjust the chemical composition of the wire.
In the smelting process, the factory should strictly control the melting temperature and melting time to prevent aluminum oxidation and alloying element burning.
Casting:
The molten aluminum liquid is poured into the casting mold for continuous casting.
In the casting process, workers should control the casting speed and cooling rate to obtain good structure and performance of the casting billet.
2. Drawing and processing
Labal:
The cast aluminum billet is sent into the drawing machine for multi-pass drawing.
During the drawing process, the worker should choose the appropriate drawing die and drawing speed to ensure that the diameter and shape of the welding wire meet the requirements.
At the same time, workers also need to regularly check and replace the drawing die to prevent the wear of the die from affecting the quality of the welding wire.
Intermediate processing:
During the drawing process, workers need to perform intermediate annealing to eliminate the drawing stress and improve the plasticity and toughness of the wire.
The alloy composition and performance requirements of aluminum alloy welding wire determine the annealing temperature and time.
Surface treatment:
Clean the surface of the drawn wire to remove oil and oxide.
As required, the welding wire can be polished or coated to improve its surface quality and corrosion resistance.
3. Quality inspection and packaging
Quality inspection:
Chemical composition analysis, mechanical properties testing, surface quality inspection and diameter measurement of the welding wire.
Record and save inspection results, identify and deal with non-conforming products.
Packing:
The qualified aluminum welding wire shall be packaged according to the specification and quantity.
The packing material should be moisture-proof, rust-proof and damage-proof.
Product Shows Of Aluminum Welding Wire





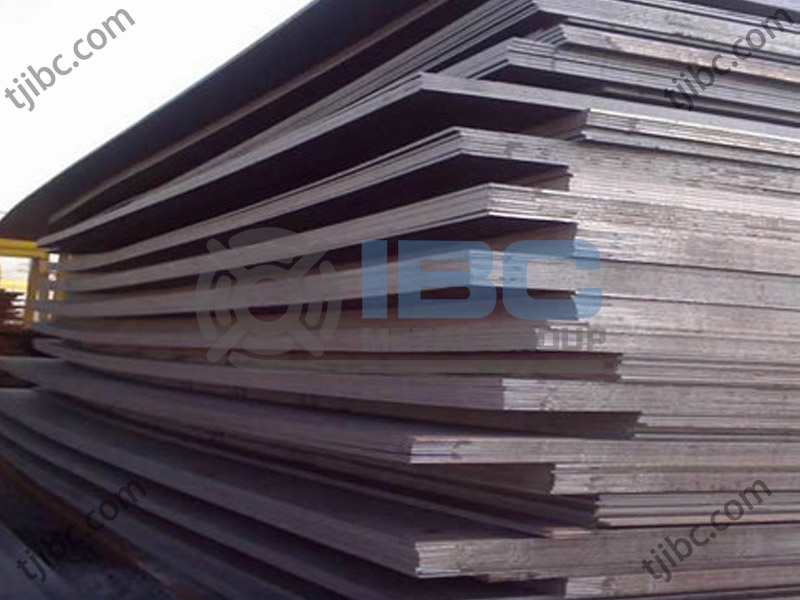
Contact with us today!