Classification of Flange Could According to Different Aspects. Such As Ability to Withstand Temperatures and Pressures. Piping flanges come in various types to cater for the varying service conditions they must endure. Critical considerations when selecting the type of flange include corrosion resistance and erosion resistance, pressure temperature rating (Class), number of welds needed, physical size, and cost. The most common are Welding Neck, Slip-on, Socket Weld, Lap Joint, Threaded and Blind. Other varieties engineers may find are male and female, and tongue and groove styles. Additionally, there are Orifice, Expander, Reducing and Long Welding Neck types that appear more rarely. Attachment is done through screwing on ends or welding them or even lapping (metal to metal contact).
Classification of Flange Based on Ability to Withstand Temperatures and Pressures
This is designated using a number and either the “#”, “lb”, or “class” suffix. These suffixes are interchangeable but will differ based on the region or vendor. Common classifications include: 150#; 300#; 600#; 900#; 1500#; 2500#. Exact pressure and temperature tolerances will vary by materials used, flange design, and flange size. The only constant is that in all cases, pressure ratings decrease as temperatures rise.
Common Flange Types and Characteristics
As already described before, the most used flange types ASME B16.5 are.. Welding Neck, Slip On, Socket Weld, Lap Joint, Threaded and Blind flange. Below you will find a short description and definition of each type, completed with an detailed image.
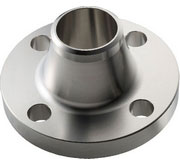
Welding Neck Flange
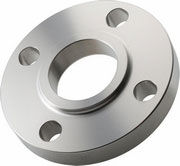
Slip On Flange
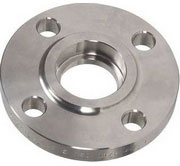
Socket Weld Flange
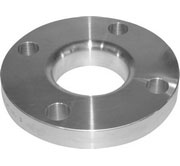
Weld Lap Joint fl
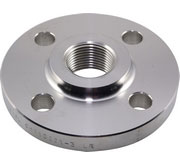
Threaded Flange
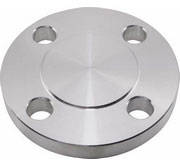
Blind Flange
Flanges are not a one-type-fits-all sort of solution. Sizing aside, matching the ideal flange design to your piping system and intended usage will help to ensure reliable operation, a long service life, and optimal pricing. Here’s a look at the most common flange types available.
Threaded Flanges
Also known as a screwed flange, this style has a thread inside the flange bore which fits with the matching male thread on the pipe or fitting. The threaded connection means you can avoid welding in many use cases. Simply match the threading to the pipes you wish to connect.
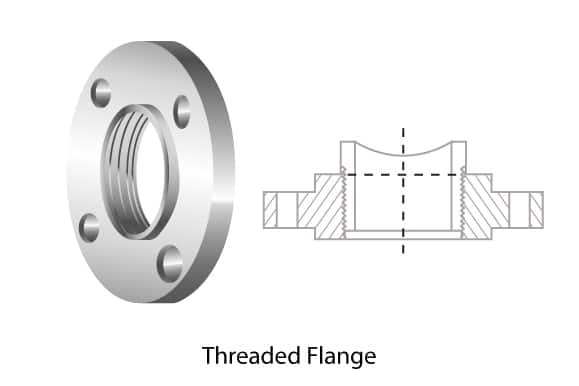
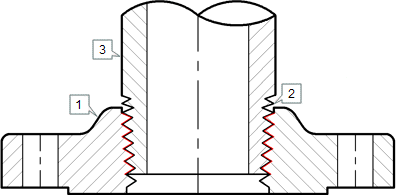
Socket-Weld Flanges
Ideal for smaller pipe diameters in low-temperature and low-pressure scenarios, socket-weld flanges feature a connection in which you place the pipe into the flange and then secure the connection with a single multi-pass fillet weld. This makes this style simpler to install than other welded flange types while avoiding the limitations associated with threaded ends.
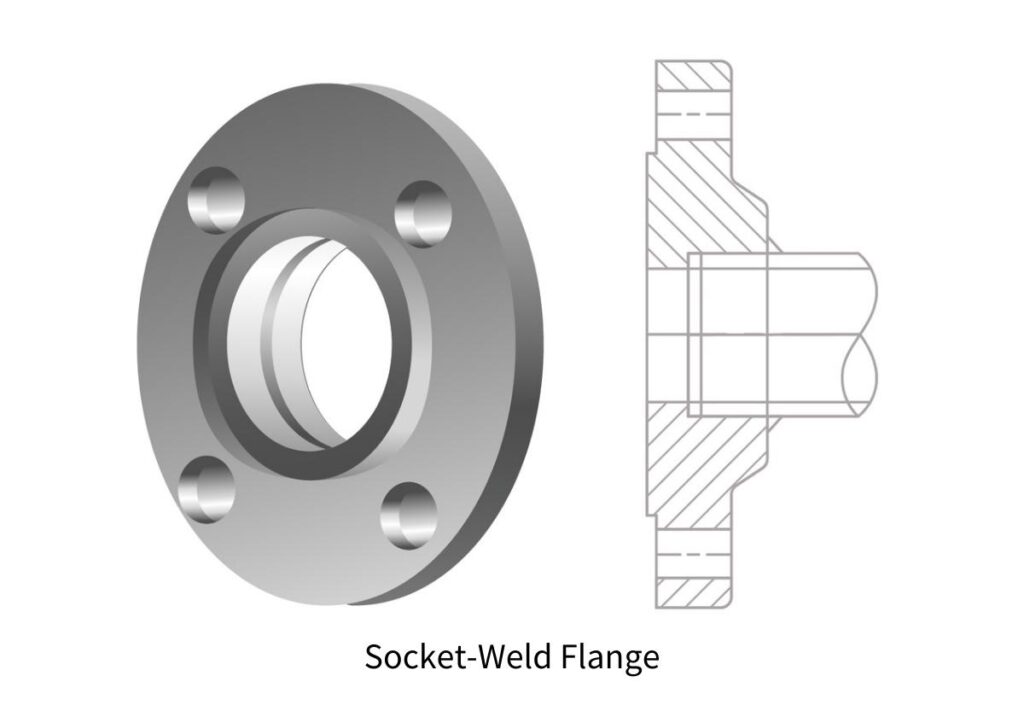
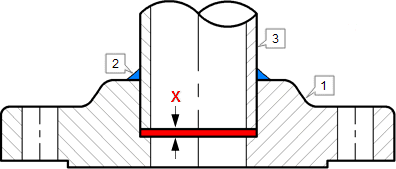
Slip-On Flanges
Slip-on flanges are very common and are available in a large range of sizes to accommodate systems with higher flow rates and throughput. Simply match the flange to the outer diameter of the pipe you intend to connect. Installation is slightly more technical as you’ll need fillet weld both sides to secure the flange to the pipe.
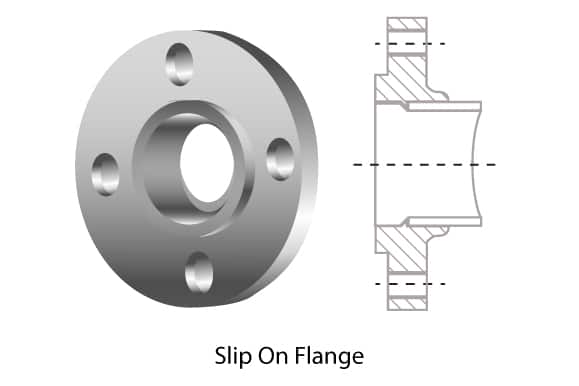
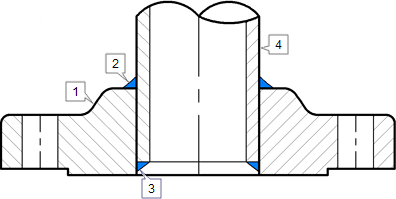
Lap Joint Flanges
Featuring a two-piece design, lap joint flanges require butt welding of the stub end to the pipe or fitting with the use of a backing flange to create the flanged connection. This design makes this style popular for use in systems with limited physical space or systems which require frequent dismantling and maintenance.
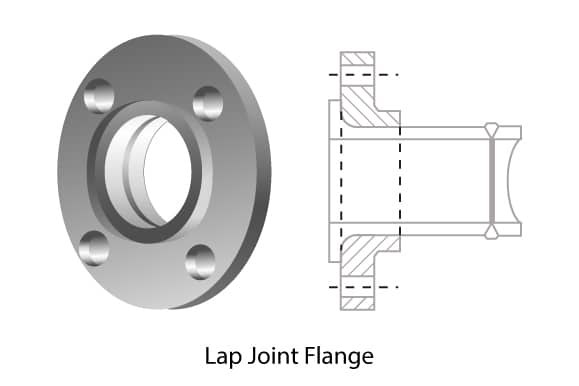
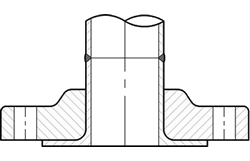
Weld Neck Flanges
Like lap joint flanges, weld neck flanges require butt welding for installation. However, their integrity, performance in systems with multiple repeat bends, and the ability to use them in high-pressure and high-temperature systems make them a leading choice for process piping.
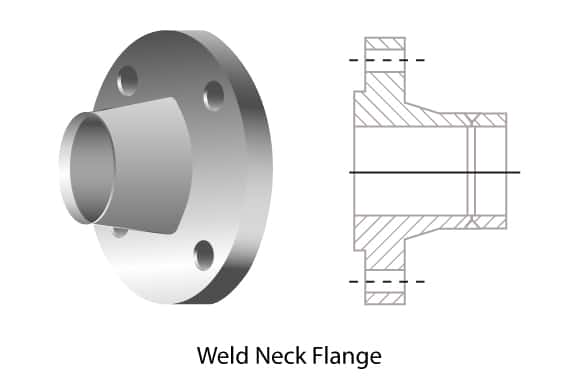
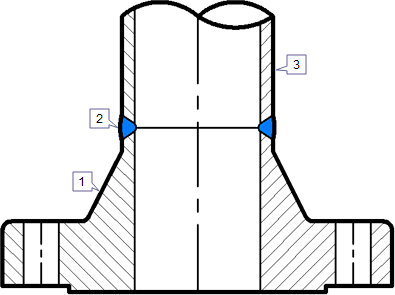
Blind Flanges
Used for terminating or isolating piping systems, blind flanges are essentially boltable blank discs. When installed properly and combined with the correct gaskets, they can achieve an outstanding seal which is easy to remove when needed.
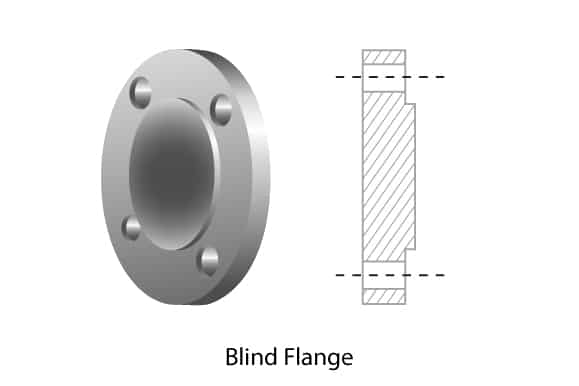
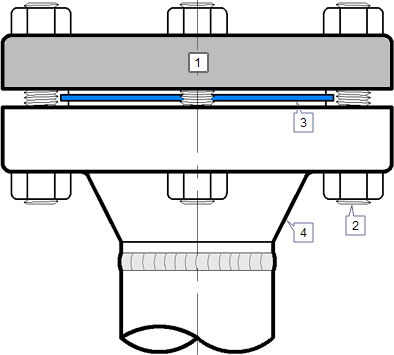
Speciality Flanges
The flange types listed above are the most common. However, there is a range of additional specialized flange types available to suit a range of uses and environments. Other options include nipoflanges, weldoflanges, expanding flanges, orifice, long weld neck and reducing flanges.
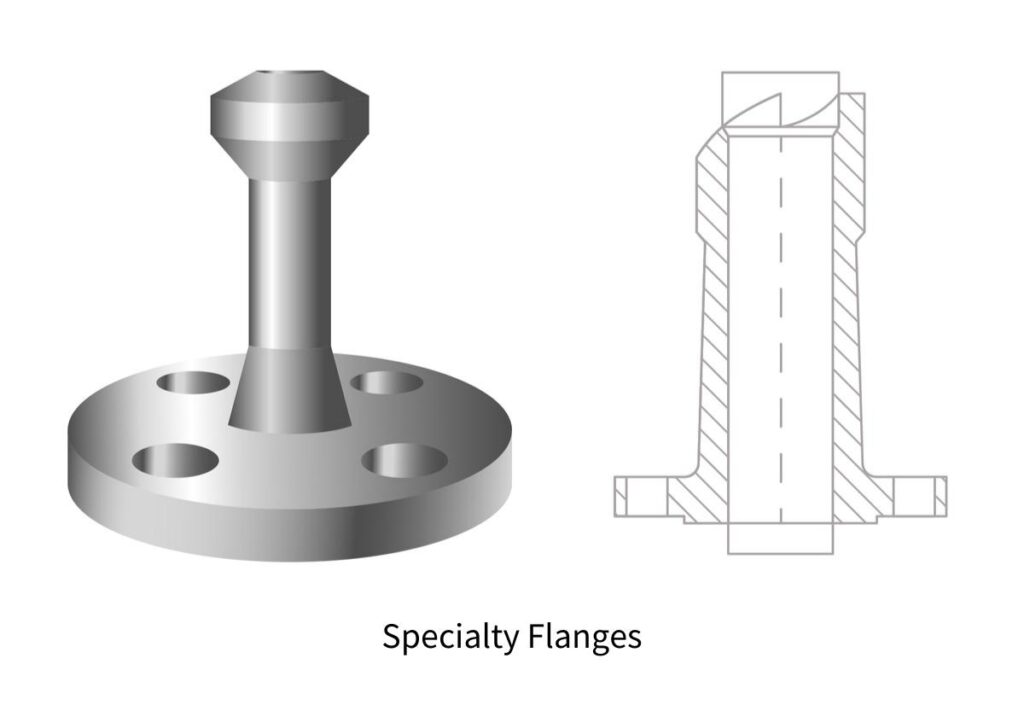
Classification of Flange According to Machinery Industry
Flanges are the interconnected parts between the shaft and the shaft, which are used to connect pipe ends. Below is the classification of flange according to the machinery (JB) industry industry standard, national (GB) standard, chemical industry (HG) industry standard, petrochemical (SH) industry standard, let’s take a look.
1. According to the machinery (JB) industry standard: integral flange, butt welding flange, plate flat welding flange, butt welding ring plate loose flange, flat welding ring plate loose flange, flanging ring plate loose flange, flange cover.
2. According to the national (GB) standard, it is divided into: integral flange, threaded flange, butt welding flange, flat welding flange with neck, socket welding flange with neck, butt welding ring with neck loose flange, plate flat flange Welding flange, butt welding ring plate loose flange, flat welding ring plate loose flange, flanging ring plate loose flange, flange cover.
3. According to the chemical industry (HG) industry standard: integral flange (IF), threaded flange (Th), plate flat welding flange (PL), neck butt welding flange (WN), neck flat welding flange (SO), socket welding flange (SW), butt welding ring loose flange (PJ/SE), flat welding ring loose flange (PJ/RJ), lining flange cover (BL(S)), Flange cover (BL).
4. According to the petrochemical (SH) industry standard: threaded flange (PT), butt welding flange (WN), flat welding flange (SO), socket welding flange (SW), loose flange (LJ) , Flange cover (not shown).
Overview Classification of Flange
The following table provides some important information about flange types. The table includes ASME standards, but alternative international and national standards are also available (DIN, EN, etc.). However, ASME is the most widely recognized piping standards organization, which is why its standards have been cited.
A flange type’s sealing face is indicated in the ‘Faces’ column in the following table. The table should be regarded as a general overview table, with specific information to be found in relevant standards. However, there may be exceptions to the rule depending on the type of flange.
Flange Type | NPS (inch) | ASME Class | Faces | Joint Integrity | Weld | ASME Standards |
Welding Neck Flange | All | All | All | High | One butt weld | B16.5, B31.3 |
Slip-on Flange | Many | Generally, ≤ 600 | FF, RF | Medium | One or two fillet welds | B16.5, B31.3 |
Socket Weld Flange | Generally, ≤ ½ to 2.Max ≤ 4 | ≤ 600 | FF, RF | Medium | One fillet weld. | B16.5, B31.3 |
Lap Joint Ring Flange | Not used for small sizes. | NA | FF | NA | None | B16.5, B31.3 |
Stub End of Lap Joint Flange | 150 to 2500 | FF, RF, RTJ | High | One butt weld | B16.9, B31.3 | |
Threaded Flange | Generally, ≤ ½ to 2.Max ≤ 4 | ≤ 300 | FF, RF | Low | None | B1.20.1, B31.3 |
Blind Flange | All | All | All | NA | None | B16.5, B31.3 |
How Do Pipe Flanges Work?
A flange is the second most commonly used joining method after welding for connecting pipe systems with equipment, valves, and other components of virtually any processing system. By making it easier to disassemble and access system components, using flanges allows for greater flexibility when maintaining piping systems. A typical flanged connection is comprised of three parts:
- Pipe Flanges
- Gasket
- Bolting
Most of the time, gaskets and bolts are made from the same materials as the piping components you wish to connect, or approved materials. Stainless steel flanges are some of the most common. It is, however, important to match the flanges to your needs since they come in a variety of materials. As well as Monel and Inconel, other common flange materials include Chrome Moly, Inconel, and many others depending on your application.
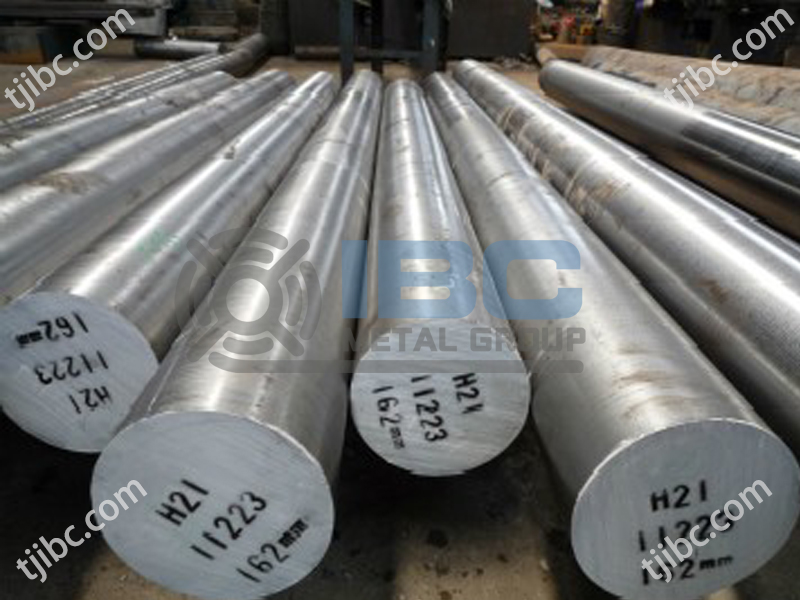
Contact with IBC Metal Group Today!