Hot work steel is a kind of alloy tool steel. It can manufacture molds that require hot deformation processing of metals under high temperature and high pressure conditions, such as hot forging dies, hot extrusion dies, die casting dies, hot upsetting dies, etc.
Because these molds are exposed to high temperature and high pressure for a long time during operation, this steel requires a specific set of performance characteristics. Including high strength, high hardness, high thermal stability, high thermal strength, thermal fatigue, good toughness and wear resistance.
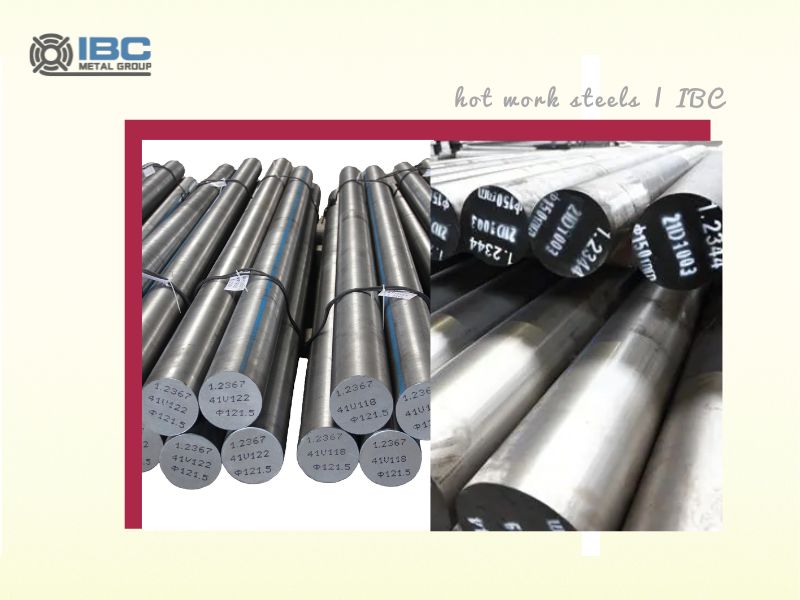
Manufacturing Process Flow
Raw material preparation: Continuous casting billets or ingot are obtained from the steel mill. And these raw materials are sent to the rolling shop to prepare for subsequent hot rolling production.
Heating: The raw material is heated to the appropriate temperature, usually between 1100°C and 1300°C. The purpose of this step is to improve the plasticity of the steel, reduce the rolling force, and reduce the tensile stress. So that it is easier to carry out subsequent rolling and deformation processing. The choice of heating temperature is determined according to the composition and performance requirements of the material.
Roughing: The heated material is fed into a large roughing mill for roughing. The roughing mill usually consists of more than two roller tables. And its main function is to flatten the raw material into a billet with a certain width and thickness.
Medium rolling: The rough rolled billet is then fed to the medium rolling mill for medium rolling. The medium mill is composed of multiple rolls. It can further reduce the thickness of the billet and increase its width.
Finishing rolling: The billet is further fed into a small finishing mill for finishing rolling. The finishing mill usually consists of more roller tables. It reduces the thickness of the billet and makes its surface smoother.
Cooling: The finished steel plate is sent to the cooling equipment for rapid cooling. The purpose of this step is to reduce the temperature of the steel and improve its structure and properties. The cooling method can be air cooling or water cooling, the specific choice depends on the use of steel requirements and actual cooling conditions.
Cutting and leveling: The cooled steel sheet is cut to the desired length and fed to the leveler for surface treatment to ensure a smooth surface.
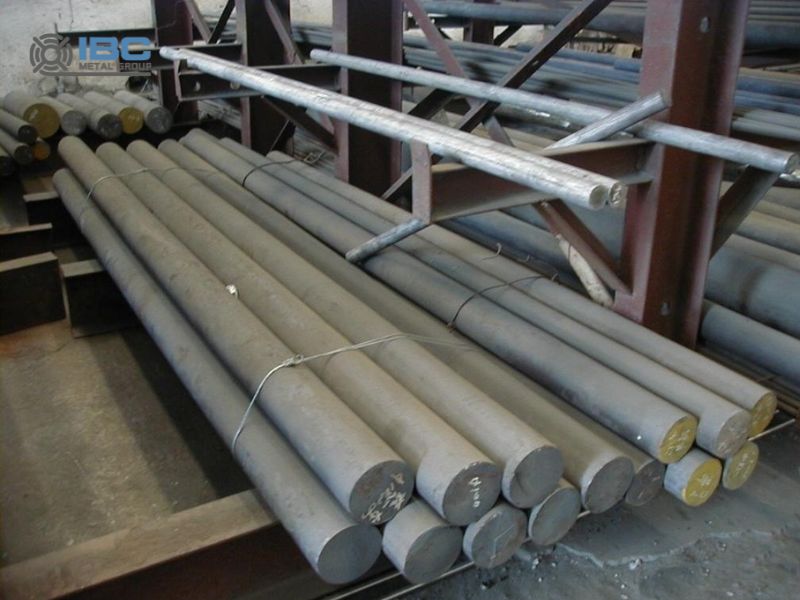
Properties of Hot Work Steel 1
High strength and hardness: It has high strength and hardness. So it can withstand the impact and pressure under high pressure environment. It can ensure the mold is not easy to deformation and damage during the working process. This high strength and hardness ensure the stability and reliability of the mold.
Good thermal stability: it can also maintain stable performance in high temperature environments to avoid deformation or damage due to temperature changes. This feature ensures that the mold can maintain its accuracy and long service life under long working conditions at high temperatures.
Excellent wear resistance: Because the hot work die is often in contact with high temperature metal during the working process and is affected by friction and wear, the die steel is required to have high wear resistance. This wear resistance can reduce the wear of the mold and extend its service life.
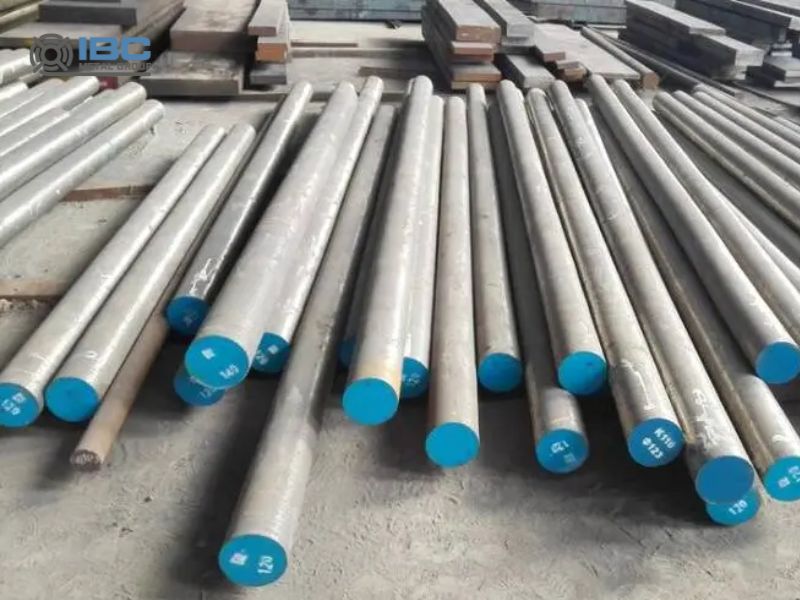
Properties of Hot Work Steel 2
Good heat resistance fatigue: the hot working mold will be repeatedly heated and cooled during the working process. It is easy to produce thermal stress, resulting in the formation of mesh cracks on the surface of the mold. Therefore, this steel needs to have good heat resistance fatigue to resist the influence of this thermal stress and prevent premature fracture of the mold.
High hardenability: In order to ensure uniform mechanical properties of the entire section of the die, the die steel needs to have high hardenability.
Good thermal conductivity: In order to prevent the mold from reducing mechanical properties due to excessive heat accumulation, the die steel needs to have good thermal conductivity to reduce the die surface temperature and reduce the temperature difference inside the mold.
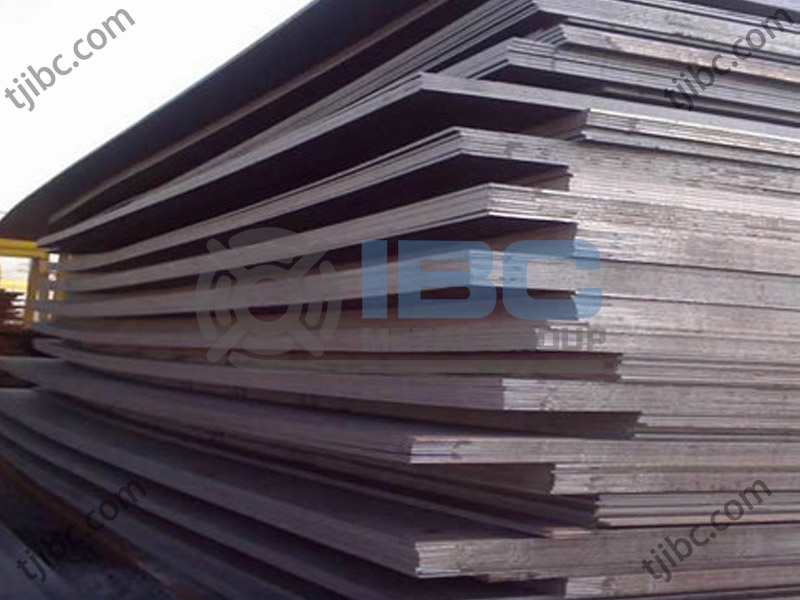
Contact with us today!