Offshore and Marine steel plate is a steel plate material specially used for ships and Marine engineering structures. They have strict requirements in terms of strength, toughness, corrosion resistance, etc., to ensure the safe operation of ships in various sea conditions. It has ordinary steel plate, high strength steel plate, corrosion resistant steel plate, composite steel plate and other types.
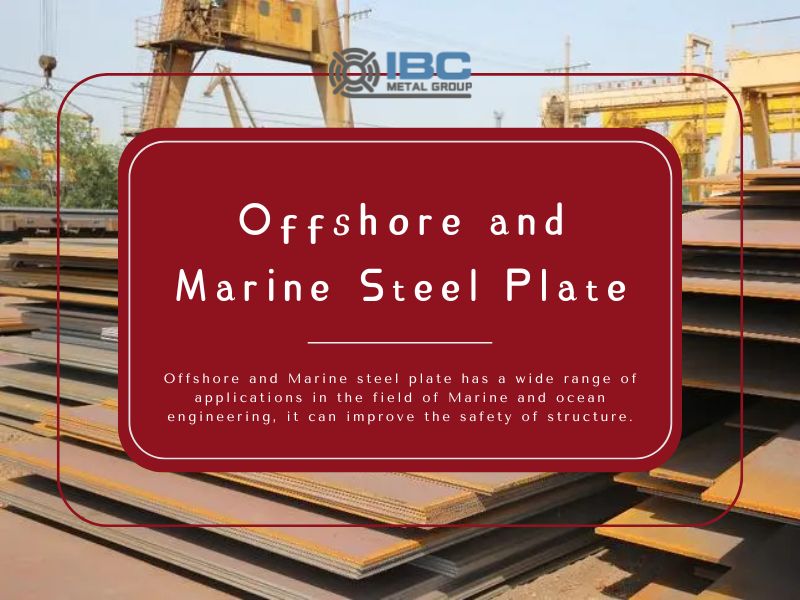
Operation Steps of Marine Steel Plate
1. Material selection: According to the design requirements of the ship and the use of the environment, choose the appropriate type and specification of steel plate. Marine steel plates can be divided into different grades and thicknesses to meet the needs of different parts and functions.
2. Cutting and pretreatment: Workers will use flame cutting, laser cutting or plasma cutting methods. They then cut the steel plate to the required size according to the design drawings. Before cutting, it is also necessary to clean the surface of the steel plate. In addition, remove rust to ensure welding quality and coating adhesion.
3. Forming and bending: through cold bending, hot bending or pressure forming, the steel plate forms the shape required by the hull structure. This often involves complex curves and angles that require precise process control.
4. Welding and assembly: Workers will use welding equipment and technology to weld and assemble the cut steel plate to form the hull structure. The welding process requires strict control of welding parameters and quality to ensure the strength and tightness of the weld.
5. Inspection and testing: non-destructive testing, pressure testing and other quality inspection of the welded hull structure to ensure that it meets the design requirements and safety standards.
6. Surface treatment and anti-corrosion: sandblasting, spraying or galvanizing are performed on the hull surface to improve the anti-corrosion performance and aesthetics of the steel plate. This helps to extend the service life of the vessel and reduce maintenance costs.
7. Installation and commissioning: the finished steel plate parts are installed on the ship for commissioning and trial operation to ensure the overall performance and safety of the ship.
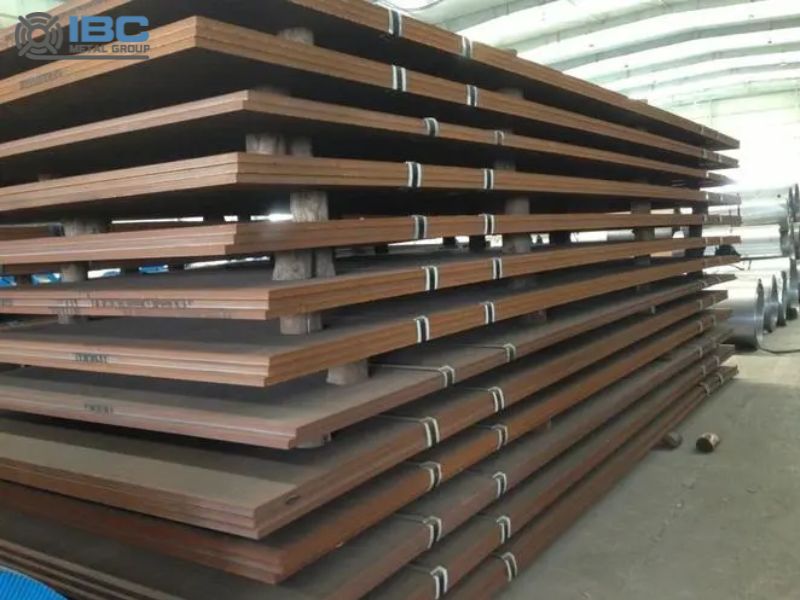
Advantages and Disadvantages
1. High strength: It has higher tensile strength and yield strength than ordinary steel, and can withstand greater loads and pressures.
2. High toughness: It has good impact toughness and low temperature toughness, and can maintain stable performance under extreme conditions.
3. Corrosion resistance: After special anti-corrosion treatment, Marine steel plate has good corrosion resistance, can resist the erosion of seawater and salt spray, extend the service life.
4. Fatigue resistance: it can maintain stable performance under the action of repeated loads and improve the safety and reliability of the structure.
5. Large weight: It usually has a high density. The use of a large number of steel plates will increase the overall weight of the ship. This will not only affect the sailing performance of the ship, but also increase fuel consumption and increase operating costs.
6. Poor heat insulation effect: The heat insulation effect of some steel plates is not ideal. It may lead to high internal temperature of the ship, affecting the comfort of the crew and the normal operation of the equipment.
So, if you want to find a higher quality Marine steel plate, contact IBC Group. We have more perfect products and services. And we can let you experience the real one-stop metal material customization process.
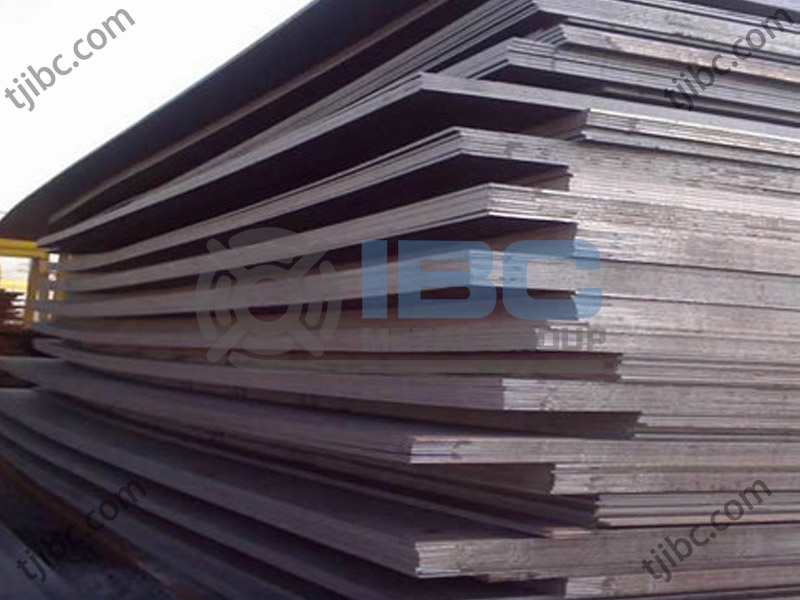
Contact with us today!