Nickel based alloy is a kind of alloy with high strength and certain resistance to oxidation corrosion at 650 ~ 1000℃. It can be subdivided into heat resistant alloy, corrosion resistant alloy, wear resistant alloy, precision alloy and shape memory alloy according to the main properties.
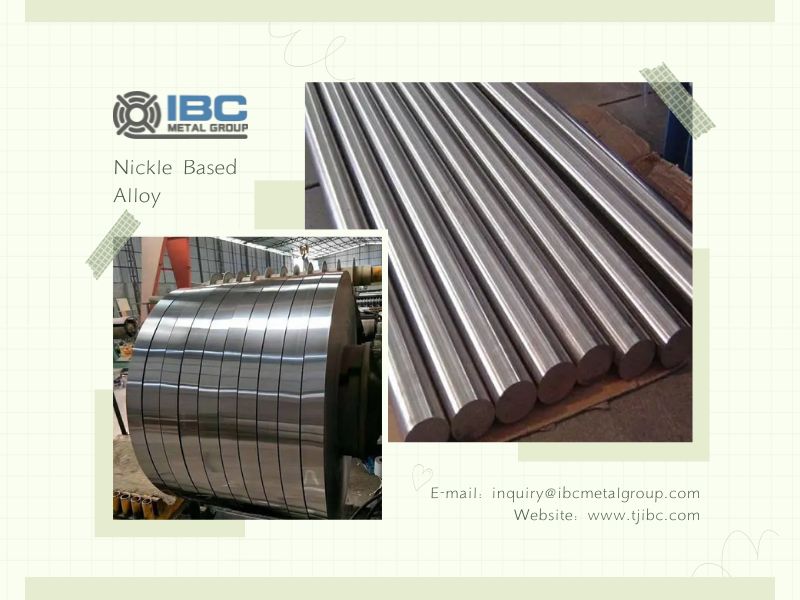
Operating Steps
1. Alloy preparation: The preparation of nickel based alloy is usually done by vacuum melting or powder metallurgy. By precisely controlling the composition ratio of alloying elements, the properties of the alloy meet the design requirements.
2. Heat treatment: After preparation, this steel often needs heat treatment, such as solution treatment, aging treatment, etc., to adjust the microstructure of the alloy and further improve its performance.
3. Forming processing: After heat treatment, various forming processes can be carried out, such as forging, rolling, drawing, etc., to meet the needs of different shapes and sizes.
4. Welding and connection: It can be connected by welding and other ways, and the welding process needs to control factors such as welding temperature, welding speed and welding atmosphere to ensure the quality and performance of the welded joint.
5. Surface treatment: In order to further improve the corrosion resistance and beauty of this alloy, surface treatment can be carried out, such as sandblasting, polishing, electroplating, etc.
6. Quality inspection: In the whole operation process, it needs to be quality inspection. It includes chemical composition analysis, mechanical properties testing, metallographic structure observation, etc. So as to ensure that the properties of the alloy meet the specified standards.
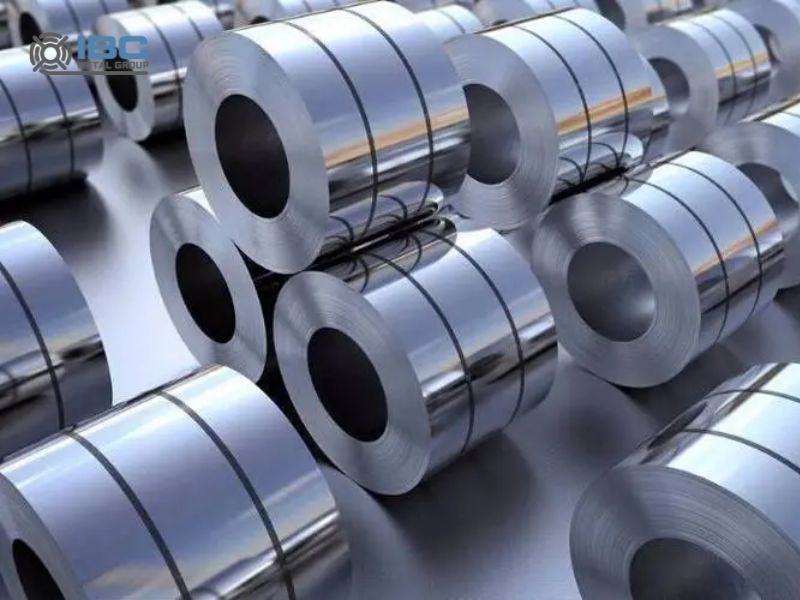
Product Advantages of Nickel Based Alloy
1. Excellent high temperature resistance
Nickel-based alloys can maintain excellent stability and mechanical properties at high temperature. This makes it particularly suitable for manufacturing high-temperature equipment components, such as aircraft engines, gas turbines, and key components in nuclear reactors. In practice, this means that this alloy component is able to maintain its structural integrity and stable performance during long periods of high temperature operation, thus ensuring continuous and efficient operation of the equipment.
2. Good corrosion resistance
It performs well in various corrosive environments, such as acid, alkali, salt and other corrosive media. Therefore, in chemical, petroleum, Marine and other fields, it is the ideal material for the manufacture of corrosion resistant equipment, pipes and valves. In practical applications, it can resist the erosion of corrosive media. It can also extend the service life of the equipment and reduce the frequency of maintenance and replacement.
3. High strength and toughness
It has high strength and good toughness, which makes it perform well under high stress and complex load conditions. In aerospace, automotive manufacturing and other fields, this alloy is often used to make parts that need to withstand high loads and shocks, such as landing gear, wheels and so on. These components are able to withstand extreme mechanical conditions during operation, ensuring the safety and reliability of the equipment.
4. Excellent processing performance
It has good plasticity and weldability, easy to process and form. This gives manufacturers the flexibility to design and produce components and products that meet specific needs. In the operation process, by using the appropriate processing technology and heat treatment technology, it can further optimize its performance and extend its service life.
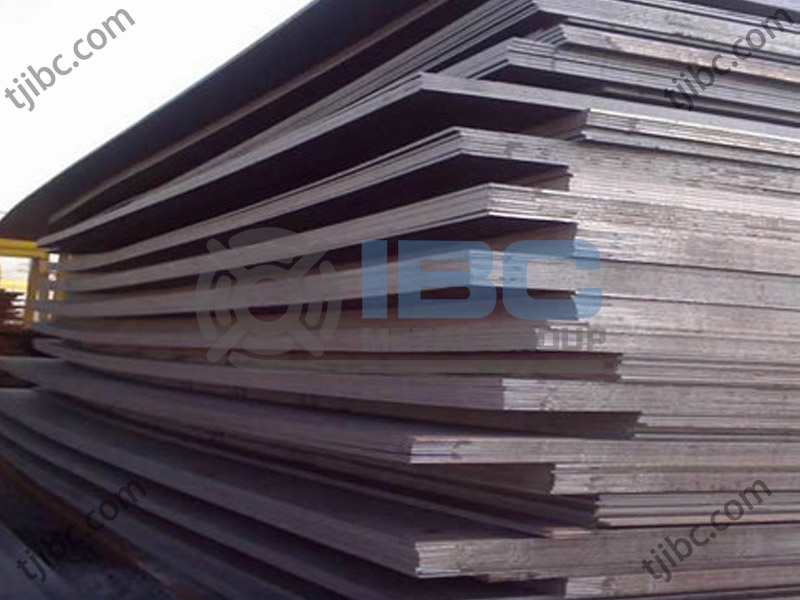
Contact with us today!