ZAM steel coils are characterized by high corrosion resistance and high edge protection. Within a certain range, the increase in the content of aluminum and magnesium inside it will increase its corrosion resistance to several times to dozens of times. Zinc-based corrosion products cover the incision surface to protect the incision. If you have related product needs, please contact IBC Group.
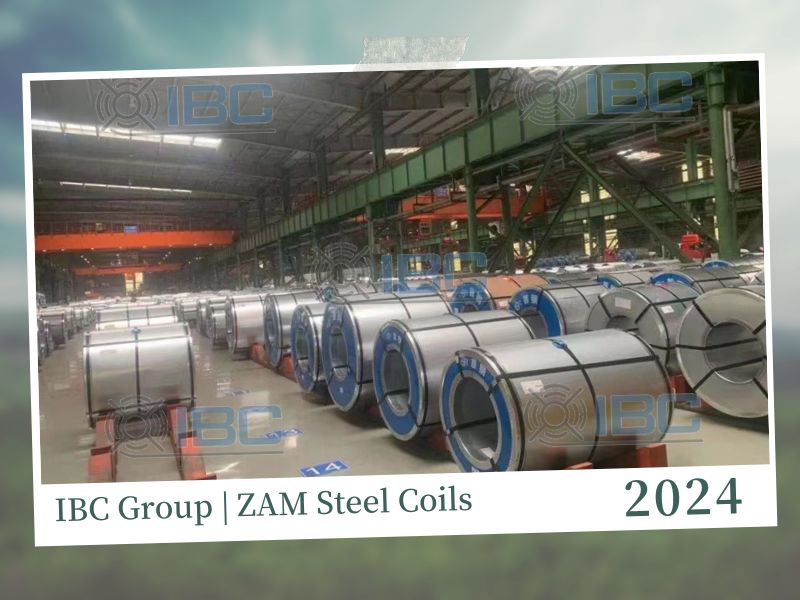
Action of Each Element
1. The role and influence of magnesium
The role of magnesium is first to improve the corrosion resistance.Secondly, a slight addition of 0.1% magnesium in the plating bath can improve the wettability of the strip in the plating solution, reduce the tension on the surface of the plating bath, and reduce the generation of plating defects, because the oxide of magnesium is very undense and basically exists in a very loose form.
This point seems to be somewhat complementary to the characteristics of aluminum, and has a very important significance for the production of high-strength steel with higher alloy content by using a coating with higher aluminum content. However, in the zinc aluminum magnesium plating solution, the content of magnesium is high. And the problem of magnesium oxide is not dense will bring a series of side effects, which has become a major difficulty in the production of hot-dip galvanized aluminum magnesium products.
2, the role and influence of aluminum
First of all, the addition of aluminum on the basis of galvanizing can significantly improve the corrosion resistance and heat resistance, which is also true in the zinc aluminum magnesium coating. Secondly, adding a small amount of aluminum in galvanizing can inhibit the reaction between zinc liquid and iron and reduce the Fe-Zn compound layer. Third, aluminum can inhibit the limitations of magnesium oxidation, aluminum oxide is very dense. It can reduce the impact of magnesium loose oxide if appropriate. So aluminum magnesium oxide can form a film to prevent product defects.
Of these three characteristics, the first has only advantages and no disadvantages, but the second and third are double-edged swords. Like magnesium, aluminum is very high in zinc aluminum magnesium bath. On the one hand, aluminum inhibits the reaction between zinc and iron. But the reaction between aluminum and iron is more intense, which becomes the main contradiction. On the other hand, the problem of easy oxidation of aluminum will also bring a series of problems. And it also become a major problem in the production of zinc, aluminum and magnesium products.
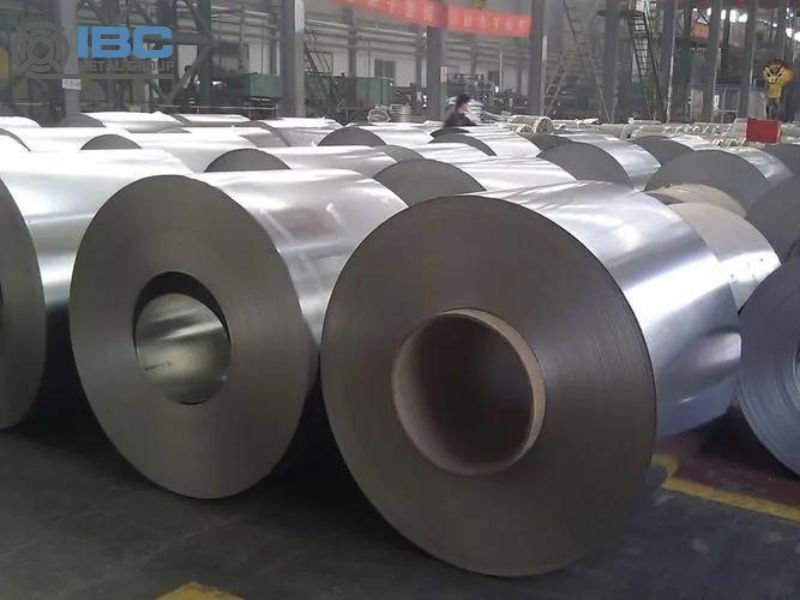
3, the role and influence of silicon
The addition of silicon is mainly to inhibit the reaction of aluminum and iron, reduce the compound layer between the coating and the steel base. And it is to improve the processing performance, which is the same principle as all high aluminum coatings.
As long as aluminum is higher than the eutectic composition of the coating, it is necessary to add silicon. The higher the aluminum content, the more silicon added. The highest aluminum-silicon coating, adding about 10% silicon. Followed by aluminum-zinc-silicon coating, adding about 1.5% of silicon; SD plus 0.2% silicon, ZAM can add 0.1% silicon. In addition, silicon can refine the grain, improve the homogeneity of the structure, and inhibit intergranular oxidation.
4. Role of other elements
Because the composition of zinc aluminum magnesium is very complex, the process performance has become very complex. In order to use zinc, aluminum, magnesium based components to produce qualified products, you can increase a small amount of other elements, improve the thermal plating process performance and performance, known as the fourth element of zinc aluminum magnesium coating composition.
For example: to prevent the oxidation of magnesium, is a problem of zinc aluminum magnesium alloy products, some companies have adopted the method of adding alloying elements in the alloy to inhibit the oxidation of magnesium. Such as POSCO patent method, is to add 0.01% ~ 0.1% gallium and 0.005% ~ 0.1% indium in the alloy. Shougang’s patent is to solve this problem by adding 0.01% ~ 0.1% calcium, barium or 0.01% ~ 0.4% lithium to the alloy. Workers can add titanium and boron to refine the grain and inhibit the formation of Mg2Zn11 tissue. They can also improve the uniformity of the structure by adding rare earths, inhibit intergranular corrosion, and further improve corrosion resistance.
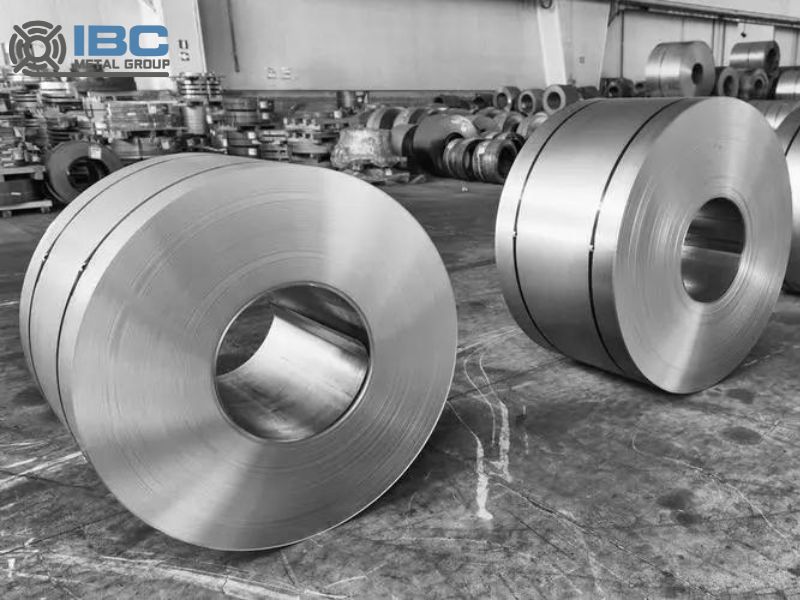
The Development Trend of ZAM Steel Coils
The following occasions are only the use of ZAM steel coils, and other products cannot be replaced:
(1) In outdoor long-term use occasions, such as high-speed guardrail, requiring thicker product specifications and thick surface coating, previously had to use batch galvanizing method. And after the birth of zinc aluminum magnesium, you can use continuous hot-dip galvanizing aluminum magnesium method. Such products also have solar equipment brackets, bridge components and so on;
(2) In the case of roads in Europe and other places that need salt, if other coatings are used to produce car bottom plates, they will soon be corroded. And zinc, aluminum and magnesium plates must be used to manufacture, such cases as seaside villas and other buildings;
(3) Special occasions that require acid resistance, such as farm poultry houses and troughs, poultry feces are acidic. And the project must use zinc aluminum magnesium plate that is more resistant to pickling and corrosion.
In general, the application prospects of this steel are very broad.
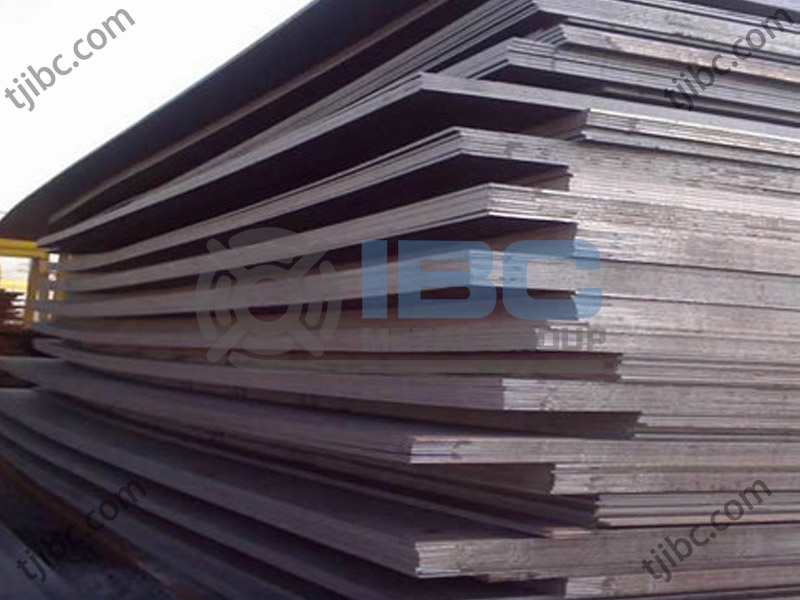
Contact with us today!