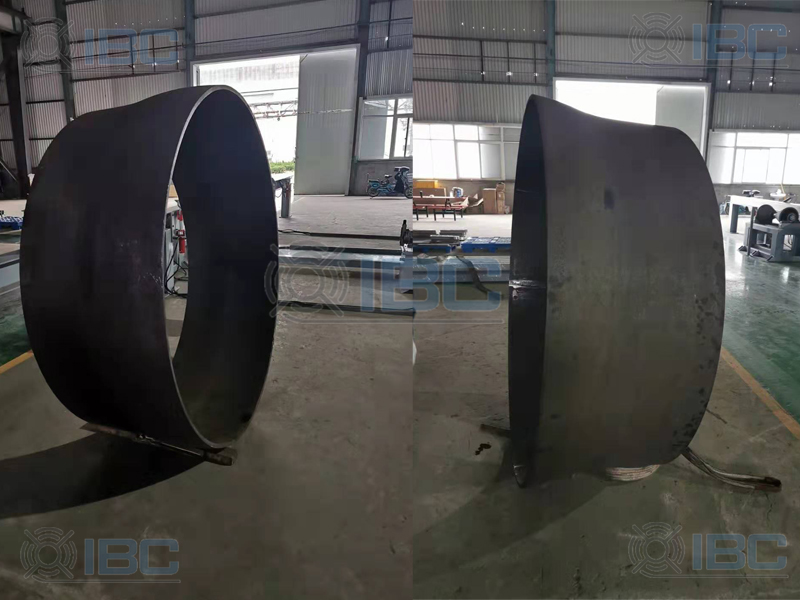
Spherical Socket End Pipe With Air Chamber Supplier
The most common type of joining pipe is a sphere end pipe with an air chamber. In accordance with the relevant standards, the pipes are usually spiral welded. Because they are easy to weld on site, they are relieved with beveled ends made with special equipment. This kinds of Joint provides the possibility of a rotation 10 degrees at the pipeline without the utilization of any special fittings. Steel pipes are welded from outside after proper erections according to the required angle.
Drawing of Spherical Socket End Pipe
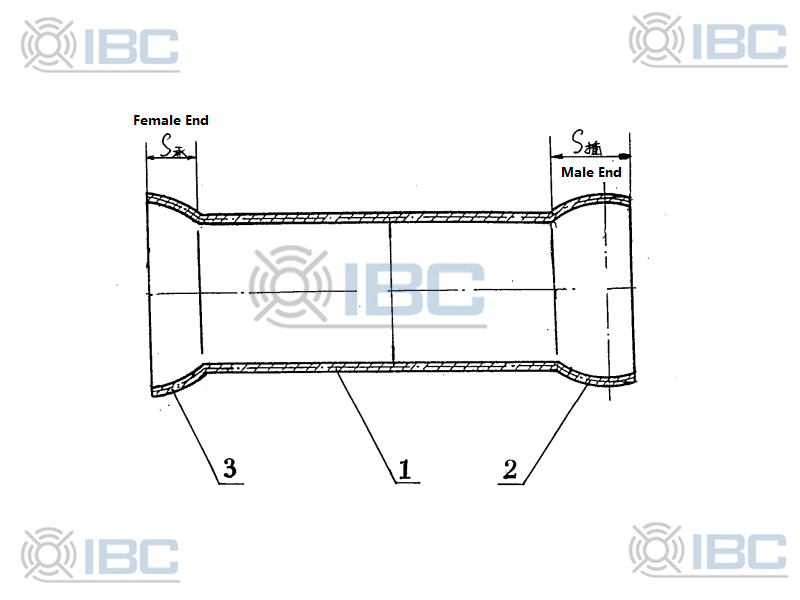
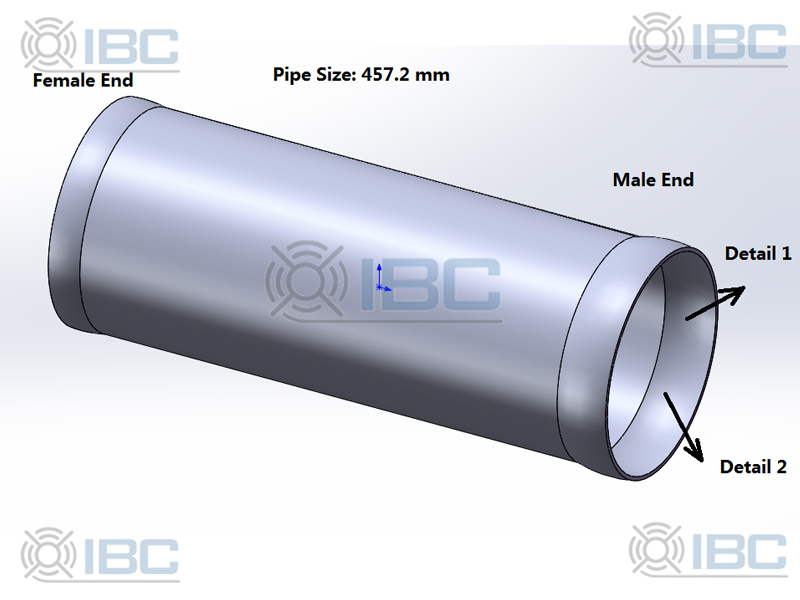
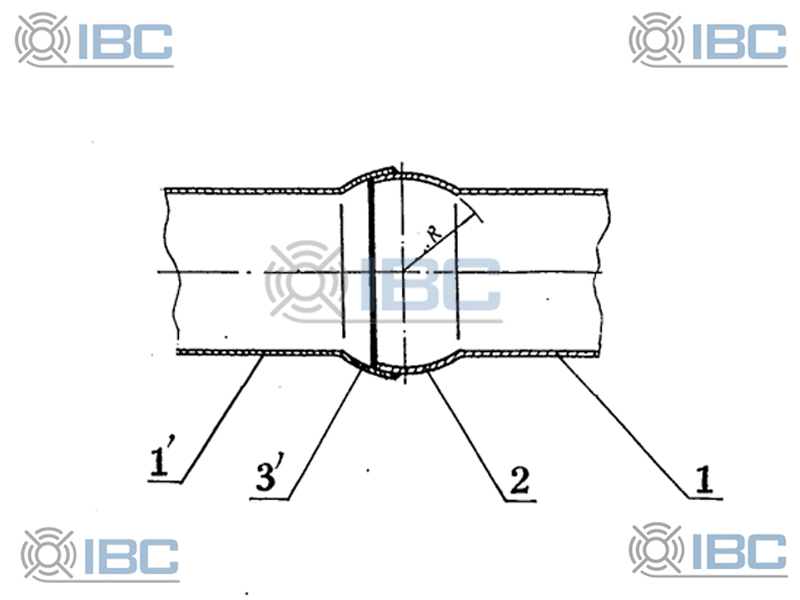
Description of Spherical Pipe Details
Norme tube / Pipe standard | EN 10224 |
Diamètre normalisé / Nominal diameter DN | ISO 6708 |
Diamètre extérieur / External diameter | 457.2 (18-inches) |
Epaisseur / Thickness | 8MM |
Type de conduite / Pipe type | Spiralée / Spiral welded |
Type de joint / Joint type | Joint rotulé / Spherical socket joint |
Usage / Use | Eau de rivière / River water |
Profondeur totale de la tulipe / Total bell depth | 120mm |
Nuance d’acier / Steel grade | L235 |
Tolérance de l’angle d’emboîtement/Tolerance of angle | 0-8° |
Poids revêtu / Coated Weight | According to Requires |
Main Advantages of Spherical Socket End Pipe With Air Chamber
- It is Easy to join pipes together.
- Reducing installation time and costs.
- Only external welding required on site.
- No internal lining repairs are necessary after on-site welding.
Sample of Spherical Socket End Pipe
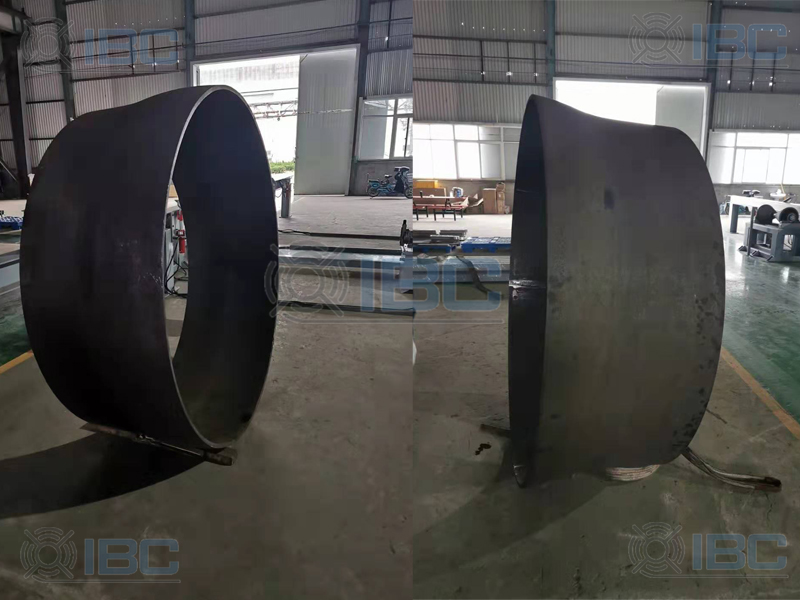
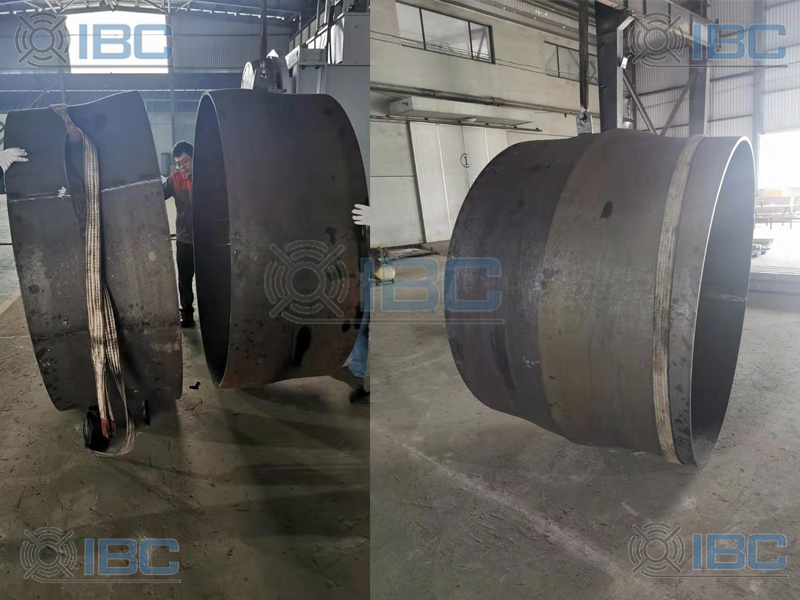
Feature of Socket Weld
The spherical socket which enables the possibility of a rotating 6° to 10° depending on the pipe diameter. Socket weld is easy to install. But it requires approx. 1/16” of the gap at the bottom of the pipe to socket into, to allow thermal expansion. This gap can lead to an over-stress problem that cracks the fillet weld of the fitting. Socket weld is troublesome in corrosive fluid service due to crevice corrosion. And it is easy to corrode due to the discontinuity of the smooth pipe internals.
Butt-weld is the “best” in terms of strength, fatigue. And corrosion resistance, and temperature compliance. However, it is more difficult to fit-up and weld properly, needing skilled welder and much time.
Different Coating For Spherical Socket End Pipe
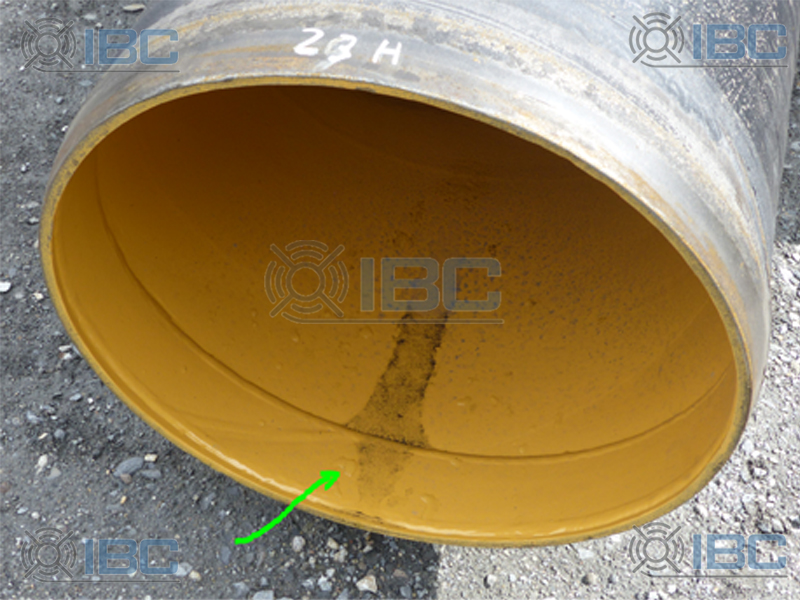
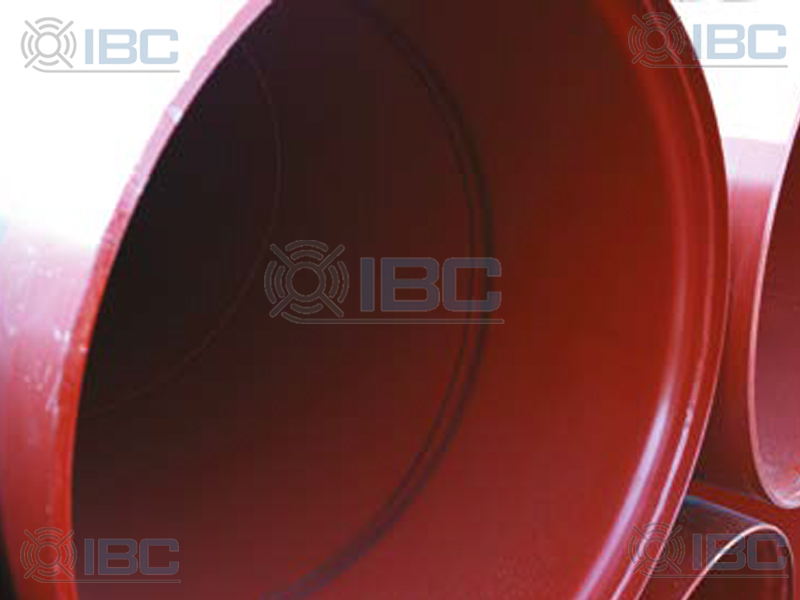
Internal coating – EPOXY according to EN 10339. Surface condition prior to application of the internal coating according to ISO 8501-1/8501-2. SA2.5 or/or SA3.0. Minimum interior coating layer of 250mm. POLYETHYLENE Exterior Coating – Minimum Layer / Minimum Thickness 4mm. We offer a variety of interior and external coatings, and we can customize them to meet your needs. Contact us today to discuss your requirements.
About the “Air Chamber”
You will see the air chamber in the picture white area. The purpose is not to heat and damage the internal coating while the external welding on the building site. We use a steel ring to weld on the pipe end. And to have space which we called “Air chamber”.
Spherical Socket End Pipe Transportation
Transportation of pipes by vessels according to the API 5LW Recommended Practice for Marine Transport by Barges and vessels. Handling and storage procedures are also based on API related customer requirements. Our factory is mainly available for the land, sea and railway transportation due to their proper locations.
We recommended Open Top Container when shipping by sea. If pipes with coating inside and outside, it will easy to have damage with coating during the loading and unloading process. Especially for unloading port. If the facility is not suitable. It will very hard for unloading without damage. If no coating, it will be ok whichever kind of container you prefer. Steel pipes after manufactured completely loaded with special apparatus used for the protection of the pipes and coatings during the loading operation.
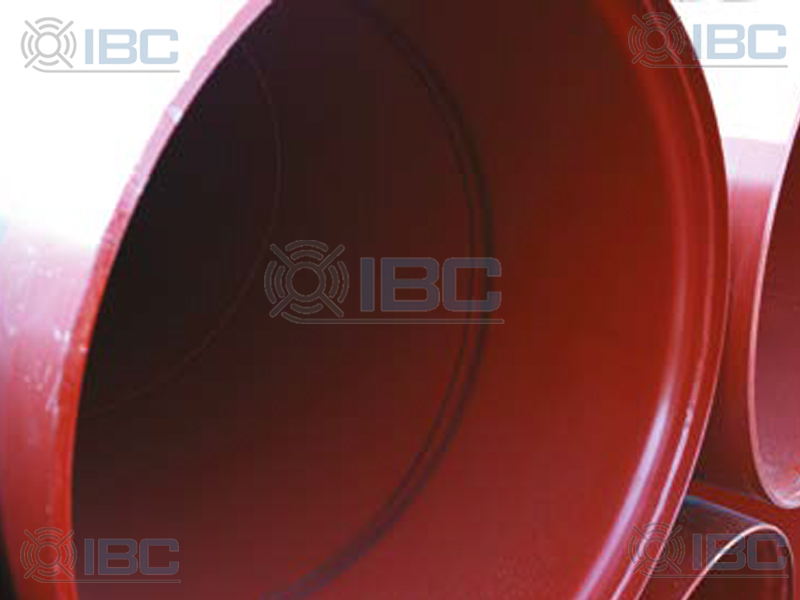
Contact With IBC