Structural steel is a type of steel used to build various structures, such as Bridges, buildings, ships, vehicles, etc. It has high strength and good toughness, and can withstand the action of various forces without deformation or fracture.
Its manufacturing process involves several steps. Including lofting, marking, cutting, straightening, edge and end processing, rounding and bending, welding, heat treatment and anti-corrosion treatment. Each step has its own specific purpose and technical requirements to ensure the quality and performance of the final product.
If you want to know more about structural steel, please contact IBC Group!
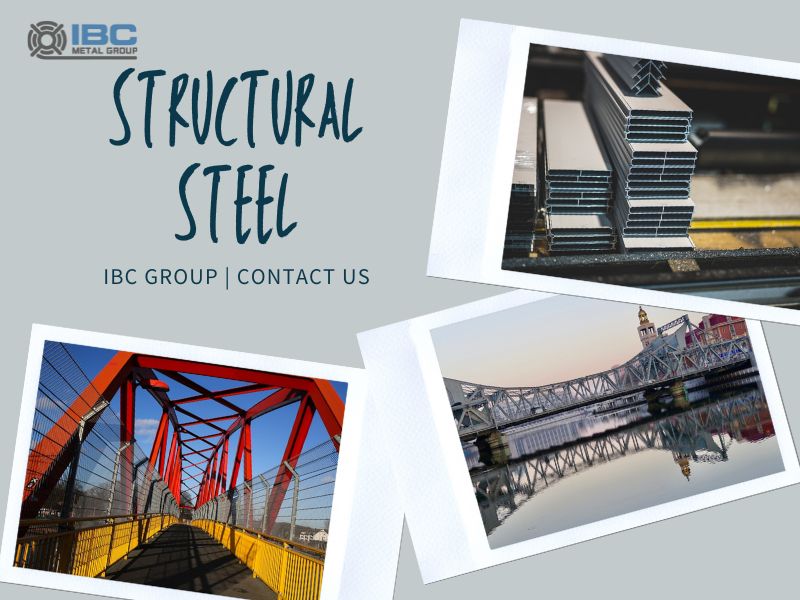
Fabrication Process 1
1. Lofting: Lofting personnel need to understand the construction drawings and technical requirements, and check whether the size and connection of components and components are appropriate. Lofting should be carried out on a flat lofting table, and the real sample should be released at a ratio of 1:1. The material of the sample rod and template must be flat and straight, and various processing symbols, reference lines, and eye hole intermediate symbols must be made according to the construction drawing and component processing requirements.
2. Marking material: check the material, draw cutting, milling, planing, hole making and other processing positions on the material, punch holes, mark the part number and so on. The marking material should pay attention to saving materials, which is conducive to cutting and ensuring the quality of parts.
3. Cutting and cutting: According to the design requirements, the workers will flame cut, plasma cut, laser cut or water cut the raw material.
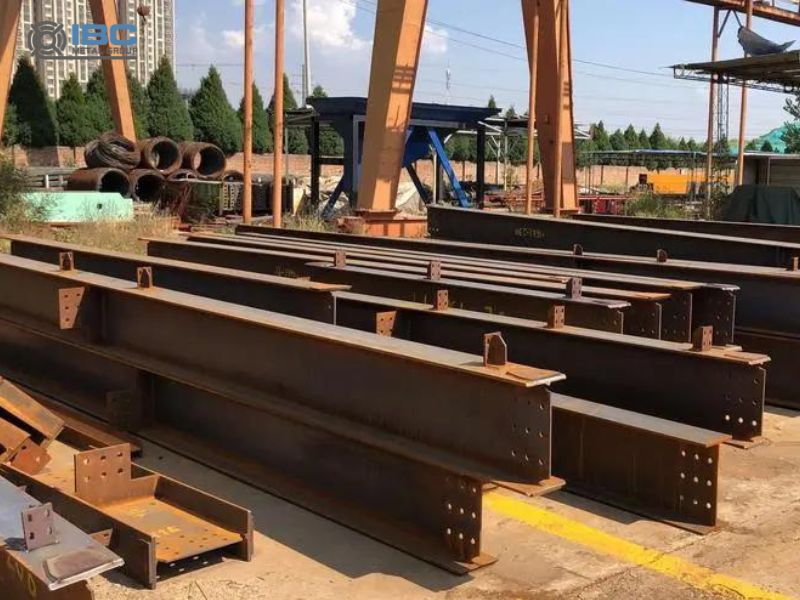
Fabrication Process 2
4. Straightening: Use a steel straightening machine for mechanical correction, or use flame correction and other methods to straighten the steel.
5. Edge and end processing: The use of shoveling, planing, milling, carbon arc gouging, semi-automatic and automatic gas cutting machine, bevel machining and other methods to process the edge and end of the steel.
6. Rounding and bending: According to different specifications of materials, the selection of steel rolling machine, pipe bending machine, bending press and other machinery for rounding and bending.
7. Welding: The components in the steel structure usually need to be welded to join the various components together. Common welding methods include manual arc welding, gas shielded welding (MIG/MAG welding), electroslag welding. The factory can also use automatic welding, robot welding and other high-efficiency and high-precision welding methods.
8. Heat treatment: In some cases, steel structures need to be heat treated to change their organizational structure and properties.
9. Anti-corrosion treatment: Finally, the steel structure is anti-corrosion treatment to increase its service life.
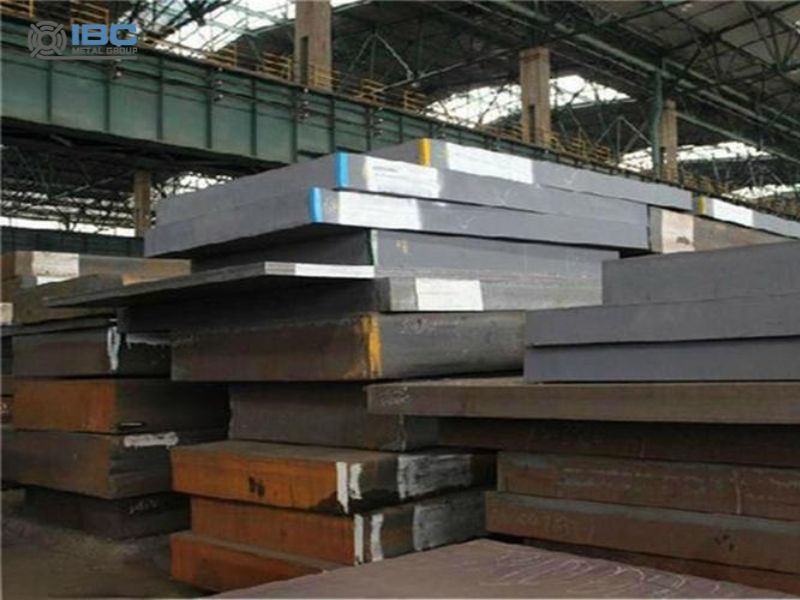
Applications of Structural Steel
1. Construction field: Manufacturing building frames, wall supports and other components. Its advantage is that it can withstand large loads, while the weight is relatively light, making the building more stable and reliable.
2. Bridge field: As a public facility carrying vehicles and pedestrians, Bridges must have the ability to bear large loads. And they also have the characteristics of wind resistance, earthquake resistance, corrosion resistance and so on. Structural steel has become an important material for bridge construction because of its high strength, good rigidity, light weight and strong corrosion resistance.
3. Road field: In road construction, it can manufacture road guardrail, highway suspension bridge and other related facilities. These facilities need to have high carrying capacity and safety performance.
4. Other fields: In addition to the above three fields, this steel has many other applications, such as energy, machinery, aerospace and so on. For example, it can make wind turbine blades and hydraulic crane brackets.
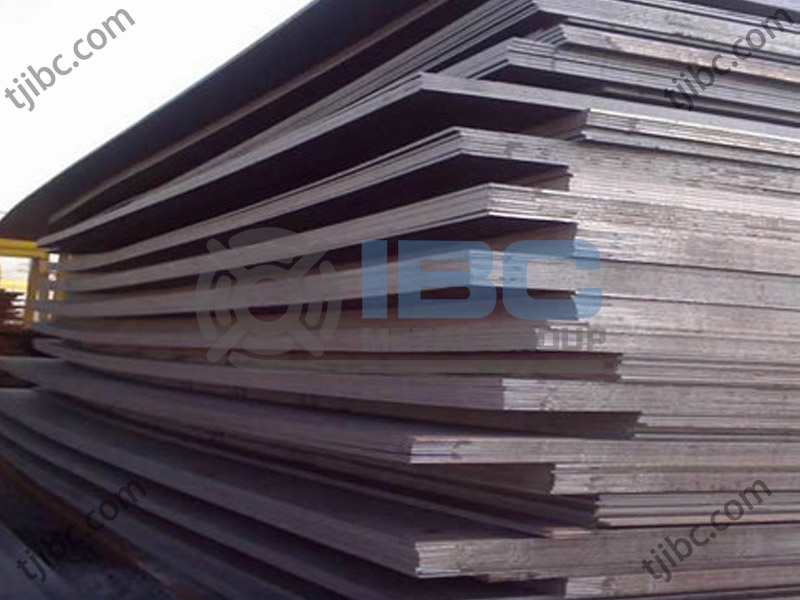
Contact with us today!