Tunnel Segment Bolt Types
1. Arc hexagon head connection bolt
Head shape: The head of the bolt is designed to be an arc hexagon shape. This design not only facilitates the use of wrenches and other tools for tightening operation, but also disperses stress to a certain extent and improves the bearing capacity of tunnel segment bolts.
Connection performance: it usually has high strength and toughness. That can meet the connection requirements of tunnel segments under complex geological conditions.
Scope of application: mainly used for longitudinal and transverse connection of tunnel segments to ensure close coordination and stability between segments.

2. Arc hexagon head connecting bolt
The circular hexagon head connection bolt is similar to the previous bolt in terms of head shape, but there are some differences:
Head shape difference: Its head shape is more rounded. This design makes the bolts smoother during tightening and reduces friction and resistance.
Connection effect: Due to the optimization of the head shape, it can better adapt to the tiny gap between segments in the connection process. And it can also improve the tightness and stability of the connection.
Application scenario: It is especially suitable for tunnel projects that require high connection accuracy and stability, such as subway tunnels and expressway tunnels.

3. Circular studs
Structure features: Both ends of circular arc double head bolt have bolt head. This design enables the bolts to be tightened simultaneously from both ends during the connection process. It improves the connection efficiency.
Connection strength: since both ends can be stressed, it can disperse more stress in the connection process, thus improving the strength and stability of the connection.
Ease of use: Its design makes it easy to connect in small Spaces or complex environments, improving construction efficiency.
Scope of application: Mainly used for tunnel segment connection scenarios requiring high strength connection and fast installation, such as large water conservancy projects, mine tunnels, etc.

Process Flow Of Tunnel Segment Bolt
1. Material procurement: first of all, it is necessary to purchase seamless steel pipes of suitable size, most of which are made of Q235 or Q345. And the specific models are selected according to customer requirements.
2. Cutting and processing: the seamless steel pipe should be cut according to the requirements of the drawings, and the flat head chamfering, and then the processing of internal threads. This step may involve the use of high speed machining technology to machining large pitch extended threaded casing, especially for the casing with deep screw teeth.
3. Welding: The worker welds the threaded casing with the square steel sheet.

4. Surface treatment: after welding, shot blasting and rust removal treatment, and then sent to the galvanizing plant for zinc infiltration and anti-corrosion treatment. Generally, the thickness of zinc layer is not less than 50um. And the thickness of zinc infiltration layer can also be increased according to customer requirements.
5. Quality inspection: sampling inspection, breaking tensile test, ensure to meet customer mechanical performance requirements.
6. Packaging and delivery: packaging and delivery according to customer requirements.
Operation Of Tunnel Segment Bolts
In tunnel engineering, the operation of tunnel segment bolt mainly involves the installation and fastening of segment. Here is a brief process:
1. Segment selection and installation location determination: according to the tunnel line type and propulsion instructions, determine the segment selection and installation location.
2. Segment installation: start from the bottom of the tunnel, successively install adjacent blocks, and finally install the top block. Before installing the sealing block, lubricate the water stop strip.

3. Advance cylinder jacking: after the segment is installed in place, extend the corresponding position of advance cylinder jacking segment in time. The jacking force should be greater than the force required to stabilize the segment.
4. Secondary tightening: after the segment ring is detached from the shield tail, tighten the bolts twice to ensure that the connection is firm.
It should be noted that during segment installation, non-segment installers are not allowed to enter the segment installation area to ensure construction safety.
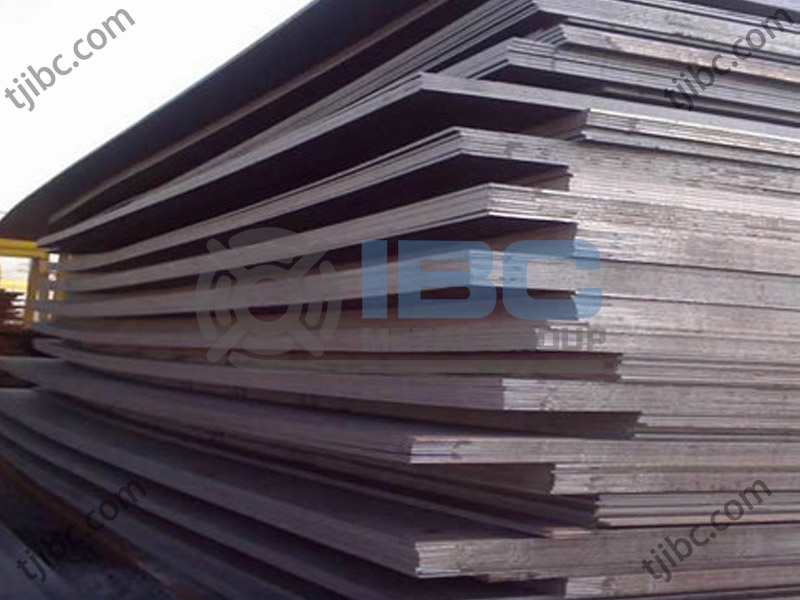
Contact with us today!