Introduction Of Marine Steel Structure Materials
1. Material characteristics for Marine steel structure
In order to meet the complex and harsh Marine environment, the performance of Marine steel structure materials should have a certain high strength and stiffness, good corrosion resistance and welding performance, and also have a certain economy. Taking offshore platforms and jackets as an example, steel needs to have comprehensive properties such as high strength, high toughness, fatigue resistance, lamellar tear resistance, good weldability, and processability.
2. Common steel for offshore platforms
Steel plate is one of the most used basic steel. It is mainly used for offshore platforms, jacket large diameter pipe coil pipe, and platforms. The prefabrication of the upper composite beam, the reinforcement of the joint part, the laying of the deck, the loading and fixing, hoisting and transportation, and other auxiliary tooling.
Section steel including H-beam, channel steel, Angle steel, square steel, etc., is also a relatively large amount of basic steel. It is mainly used for platform deck beams, jacket anti-sinking plates, operating platform support, ladder support, temporary tools, etc.
Pipe materials include rolled pipe and seamless steel pipe in two forms. The rolled pipe is the main supporting structure of offshore platform and sheath, such as column, crane column, conduit, tensile bar, etc. Seamless steel is a secondary structure, including wall support, torch arm, rest arm, trestle, cable support and support, wellhead guide and support, ladder railing and other structures.
The amount of accessory structures is small. But the types are more miscellaneous, including fasteners (bolts, nuts, gaskets), grille and its fixing system, iron chain, etc.
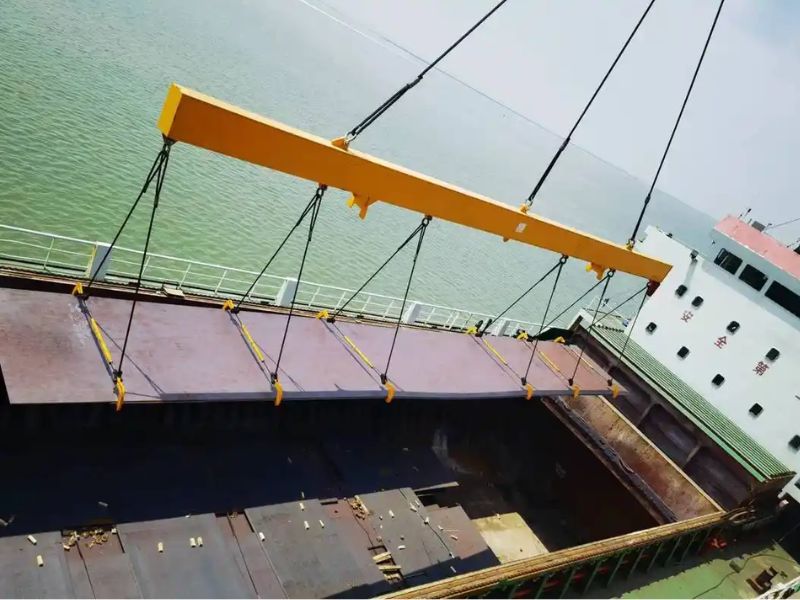
Analysis Of Utilization Rate Of Main Materials In Marine Steel Structure
There are two definitions of steel utilization. One is the construction utilization rate. It is the ratio of the pure component weight to the material used, without considering the steel consumption. The other is the typesetting utilization rate, which is the ratio of the pure component weight to the typesetting weight. The typesetting weight is the weight of steel minus the steel consumption. We can also understand it as the ratio of the actual layout area of steel to the theoretical layout area.
Typesetting utilization rate can more accurately reflect the use of materials. The higher the typesetting utilization rate is, the higher the actual steel utilization rate is. And the greater the material cost savings are.
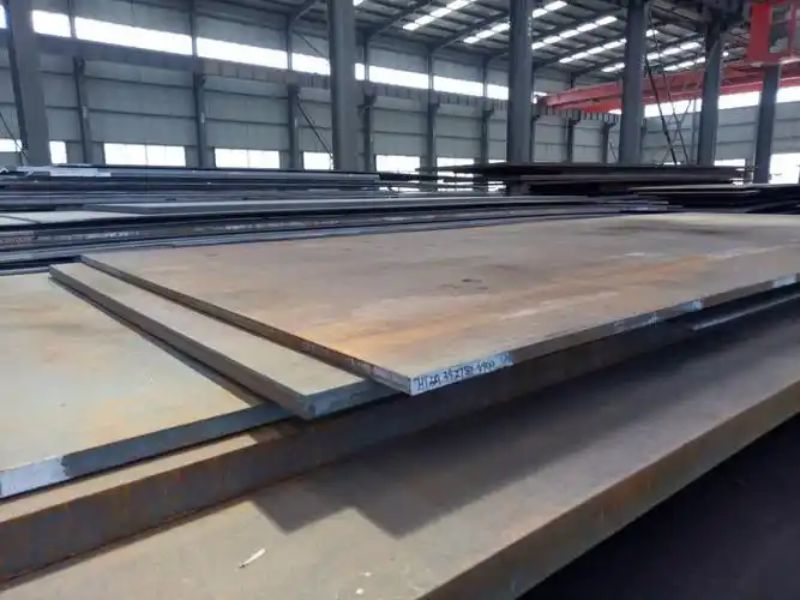
1. Comparative analysis of fixed size layout and non-fixed size layout
Fixed size typesetting is mainly suitable for products or parts with relatively fixed size. And its size or size multiple can match the fixed size specification. It is not suitable for some products or parts that need flexible adjustment or irregular size specifications. Because the material is used, its size is fixed. The advantages of fixed size typesetting are less material specifications, convenient material statistics and management, high efficiency of drawing. But the disadvantages are more waste and low material utilization rate.
Non-fixed size typesetting is mainly suitable for non-standardized, complete drawing materials, sufficient construction period of the project, its structure design is complex, rod
The size of the piece is diverse, and there is no certain rule to follow. The components of each part need to be typesetted according to their actual size, the typesetting is completed. And the materials are purchased according to the actual typesetting size. Its advantage is the first design, after the purchase, high material utilization rate. Its disadvantages are many material specifications, long procurement cycle, difficult on-site statistics management, low efficiency of drawing layout.
To sum up, for the project as a whole, simple fixed size layout or non-fixed size layout is not the best choice. We should take the project characteristics, project duration, site management and other factors into consideration, and adopt the combination of fixed size layout and non-fixed size layout. We should not only ensure the quality, safety, schedule and other requirements of the project, but also control the utilization rate of materials.
2. Manual typography
The traditional way of steel typesetting mainly relies on manual work. According to the previous project experience and understanding of steel specifications, engineers manually set out the bar 1:1 in AUTOCAD and other design software, and then make typesetting. The disadvantage of this typesetting method is that it is highly dependent on the experience of engineers. And only engineers with rich experience can ensure the rationality and economy of typesetting. The typesetting efficiency is low. And it is prone to errors, and the overall utilization rate of steel is also low.
2. Automatic typesetting by computer software
Automatic typesetting means that the computer directly extracts the detailed size information of the rod from the model. And the smart plug-in will be based on the size of the material for intelligent layout. Automatic typesetting can provide the optimal typesetting scheme according to the member parameter information provided by the model. This can not only improve the efficiency of typesetting, but also improve the accuracy of typesetting, the utilization of steel.
This kind of typesetting method needs a lot of data support, reduces the participation of human factors in the typesetting process. And the typesetting results are more objective and accurate. Through the comparative analysis of a completed project, the steel utilization rate of automatic typesetting is significantly higher than that of manual typesetting.
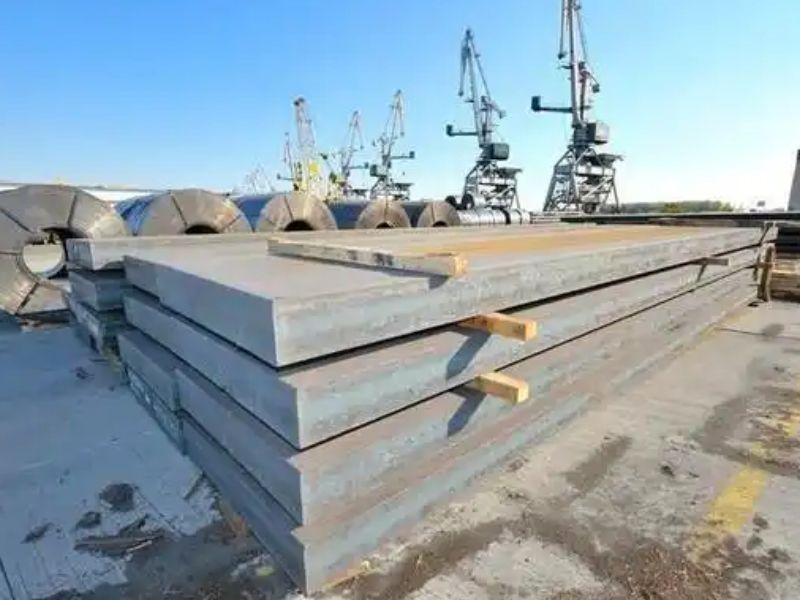
Influencing Factors And Optimization Measures Of Steel Utilization In Offshore Steel Structure
Influencing factors of steel utilization rate
The design of offshore platform, jacket and other structures involves many complex factors. If the structure design is not reasonable, it will increase many uncertain factors, which may lead to the complex and diverse size of the structure design. There are many special structures, which will cause complex size of members, which is not conducive to typesetting and blanking, resulting in material waste and affecting the actual typesetting utilization rate. The materials purchased according to the project requirements have various sizes. And the length and width are subject to the production capacity of the manufacturer. It is necessary to refine and classify the structural members to match the actual material size. The diversity of material specifications will lead to an increase in the difficulty of typesetting and at the same time reduce the material utilization rate.
Measures to improve the utilization rate of steel typesetting
1. Optimize structural design
In the design stage, the construction needs should be fully considered. And the production capacity of each steel manufacturer should be investigated in advance. On this basis, the reasonable structural form and size should be adopted under the premise of meeting the design needs. This method can optimize the specific size of structural members, can better match the raw material size of manufacturers, can reduce the waste of typesetting, improve the utilization rate of steel typesetting.
2. Optimize steel procurement specifications
In the material procurement stage, the structural form is fully considered. We can reasonably determine the layout size, try to achieve the integration of construction and procurement, according to the size of construction layout to buy materials. This method requires design drawings for construction to be determined at the beginning of the project. This has a relatively high demand for drawings and a relatively large demand for technical personnel.
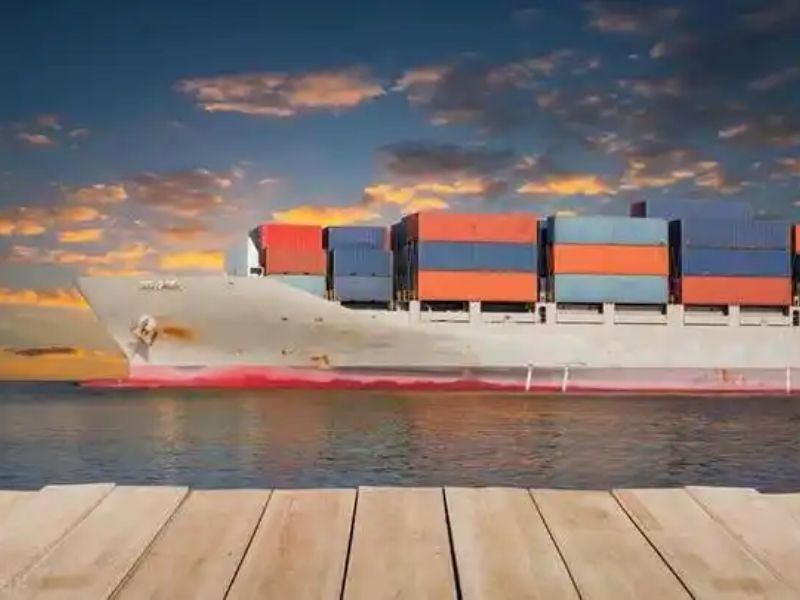
3. Introduce advanced technical typesetting software
Develop advanced modeling software and typesetting software, use digital technology to optimize typesetting design, develop open vision function, intuitive display typesetting effect. This can be more accurate layout design, reduce material waste, improve the utilization rate.
4. Combining cutting-edge technology to improve the utilization of typesetting
3D printing technology: With 3D printing technology, structural components can be manufactured directly on the construction site. This avoids the traditional process of material processing and transportation. By precisely controlling the printing process, customized design and high-precision manufacturing can be realized, thus improving the utilization rate of typesetting.
Intelligent cutting: Combining additive manufacturing technology and intelligent cutting system, precise steel components can be quickly manufactured according to actual requirements. The utilization of typesetting can be improved by reducing material waste in traditional processing.
Big data and machine learning: Using big data analysis and machine learning technology, you can process large-scale data and quickly find the optimal typesetting scheme. By training the model, the typesetting algorithm can be continuously optimized to improve its accuracy and efficiency.
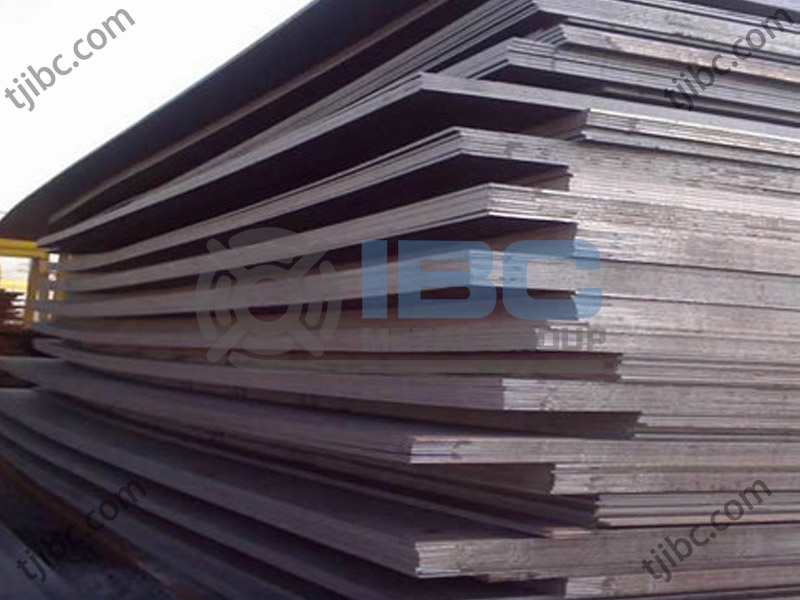
Contact with us today!