Part 1 | Applicaton of Aluminized Zinc Coil
1. Material selection and procurement of Aluminized Zinc Coil
Supplier evaluation: First, automakers need to evaluate and select qualified suppliers. For example, IBC Group can ensure that the material quality meets the standards of the automotive industry and its own design requirements.
Performance requirements: Specify specific performance requirements, such as coating thickness, composition ratio (usually aluminum 55%, zinc 43.5%, silicon 1.5%), tensile strength, elongation and corrosion resistance.
2. Design and engineering application
Parts design: According to the needs of different parts of the car, such as body plate, roof, trunk cover, engine cover, etc., design suitable parts structure.
Anti-corrosion design: Use its high corrosion resistance to optimize the body structure design. Thus reduce the use of anti-corrosion coatings, reduce costs and improve vehicle durability.
Lightweight design: This steel coil has a lighter weight than conventional steel. This can help meet the car’s lightweight goals, improve fuel efficiency or extend the range of electric vehicles.
Part 2
3. Processing and forming
Cutting and stamping: Through high-precision cutting and stamping equipment, the aluminized zinc coil is processed into the shape of parts that meet the needs of automotive manufacturing.
Welding and assembly: Use appropriate welding processes (such as resistance spot welding, laser welding, etc.) to weld parts together with other parts to complete the assembly process.
Surface treatment: If necessary, the surface of the steel coil is further treated. Such as painting or waxing to enhance aesthetic and protective properties.
4. Quality inspection and testing
Coating quality testing: Use professional testing equipment to test the thickness, uniformity and adhesion of the coating. This ensures that it meets quality requirements.
Formability testing: Evaluate the formability and deformability of parts by simulating a formability test under real-world use.
Corrosion resistance test: salt spray test, wet heat cycle test and other corrosion resistance test. This verifies the corrosion resistance of the parts under different environmental conditions.
Part 3 | Future Development Trend of Aluminized Zinc Coil
Future Development Trend
1. Expansion of application range
The wide application of body parts: Because of aluminized zinc coil’s high strength, strong corrosion resistance, high durability advantages, can be manufactured in the automobile body plate material. Such as door, trunk lid, hood, roof, body side panel and other parts. In the future, with the increasing demand for lightweight vehicles, its application in body parts will be more extensive.
The promotion of chassis components: The chassis is an important part of the vehicle structure. Its stability and corrosion resistance are directly related to the driving performance and life of the vehicle. In recent years, its application in the chassis has also become more and more extensive, and this trend will continue in the future.
2. The promotion of technological innovation
Research and development of new coating technology: With the progress of technology, the production process and coating technology of steel coil will continue to innovate. For example, the plant will use more environmentally friendly and efficient coating technology. This can not only improve the corrosion resistance of the coating, but also reduce the environmental pollution in the production process.
Improvement of processing technology: In the automotive manufacturing process, its processing technology will also continue to improve. For example, the use of advanced cold forming technology, hot stamping technology and so on. This can further improve the processing efficiency and forming quality of aluminum-plated zinc coil. In this way, it can meet the requirements of high precision and high strength in automobile manufacturing.
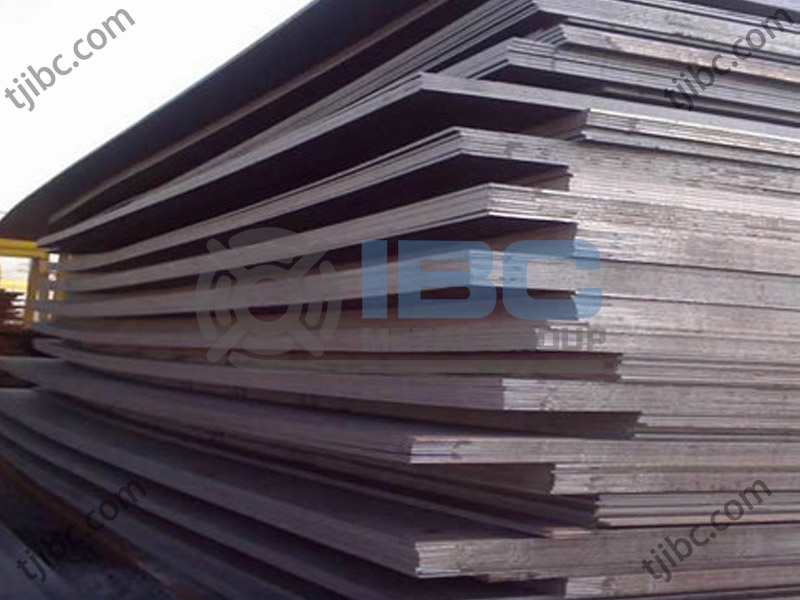
Contact with us today!