Automotive steel is a special type of steel with high strength and excellent mechanical properties. It is widely used in all aspects of automotive manufacturing, including parts such as body, chassis and engine.
This steel usually has a higher yield strength and tensile strength than ordinary steel. And it can withstand greater force and pressure, thereby improving the safety performance of the car. At the same time, this steel also has good toughness and durability. It can effectively reduce the deformation and damage of the body during the collision.
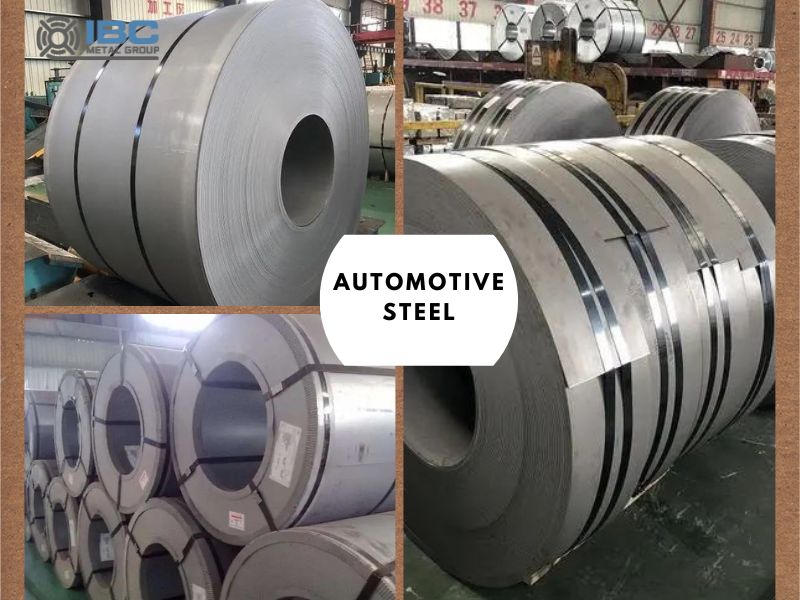
Production Process of Automotive Steel
1. Blast furnace melting: This is the first process. In this process, workers will put scrap steel, fuel, limestone and other raw materials into the blast furnace according to the production process requirements. Workers then heat the raw material in the blast furnace to melting temperatures to melt it into liquid iron. Then, the iron oxide added to the blast furnace is reduced to iron atoms, while a certain amount of heat energy is released. In addition, it is necessary to remove sulfur from the hot metal by gas reaction or blowing. This can reduce the sulfur content of iron and improve the quality of iron. Finally, workers add a certain amount of limestone to the reaction to break down compounds such as phosphate and iron phosphate. This reduces the phosphorus content of the iron.
2. Converter steelmaking: Transfer the liquid iron produced by the blast furnace to the converter. And then add a certain amount of scrap steel and other materials for steelmaking.
3. Continuous casting production: A continuous casting machine pours refined liquid steel to form steel plates of a certain size.
4. Rolling: The continuous cast steel plate is rolled into thin steel plates of different specifications by the rolling mill.
5. Pickling: pickling the rolled steel plate to remove the surface of the oxide scale.
6. Finishing: finishing the steel plate after pickling, such as trimming, leveling, cutting, etc., to meet the requirements of automobile manufacturing.
7. Galvanizing: The finished steel plate is galvanized to improve its corrosion resistance.
8. Welding: The galvanized steel plate is welded into auto parts according to the requirements of automobile manufacturing.
9. Painting: Paint the auto parts after welding to improve their corrosion resistance and appearance quality.
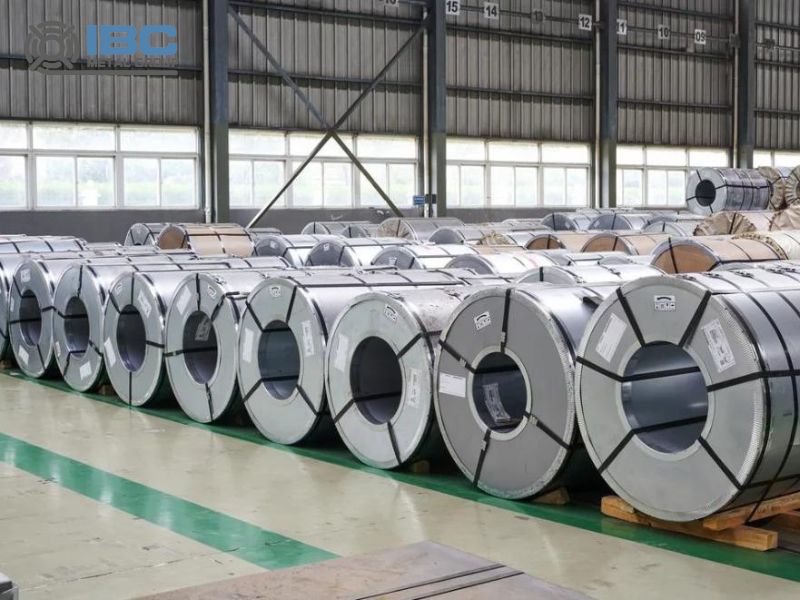
Performance Introduction 1
1. Phosphorus high-strength steel: This steel increases its strength by adding an appropriate amount of phosphorus to ultra-low carbon steel or low carbon steel. It not only has high strength and good cold forming performance, but also has good impact resistance and fatigue resistance. Therefore, phosphated high-strength steel is often used in the manufacture of automotive covering parts or structural parts, such as bumpers, fenders and so on.
2. Isotropic high-strength steel: The steel has uniform tensile formability. So it is very suitable for the production of automobile exterior covering parts. Its advantage is that it can reduce the deformation of parts in the manufacturing process. This can improve the accuracy and stability of the parts.
3. High strength gap-free atomic steel: By optimizing the chemical composition, this steel can obtain high strength and excellent cold forming properties. It is suitable for deep stamping manufacturing of complex components, such as door inner panels, spare tire compartments, etc.
Performance Introduction 2
4. High-strength low-alloy steel: by adding microalloying elements such as titanium and vanadium to the steel for strengthening, while refining the grain to improve strength. While maintaining high strength, this steel also has good welding performance and corrosion resistance, so it is widely used in automobile body structural parts.
5. Advanced High Strength steel (AHSS) : This type of steel has higher strength and better performance, and is a key material for automotive lightweight and improve crash safety. Advanced high strength steels include biphase steel, martensitic steel, phase change induced plastic steel, complex phase steel, etc. They have excellent strong plastic bonding, good collision characteristics and higher fatigue life, and are mostly used in body structural parts, such as A-pillar, B-pillar and so on.
6. Low carbon steel: low carbon automotive steel mainly refers to low carbon aluminum sedation steel or no gap atomic steel (IF steel), with low yield strength and high elongation after breaking, excellent plastic processing properties make it an ideal material for the production of complex parts. It is often used in the stamping of deep drawing and super deep drawing products such as door inner plate and wheel cover plate.
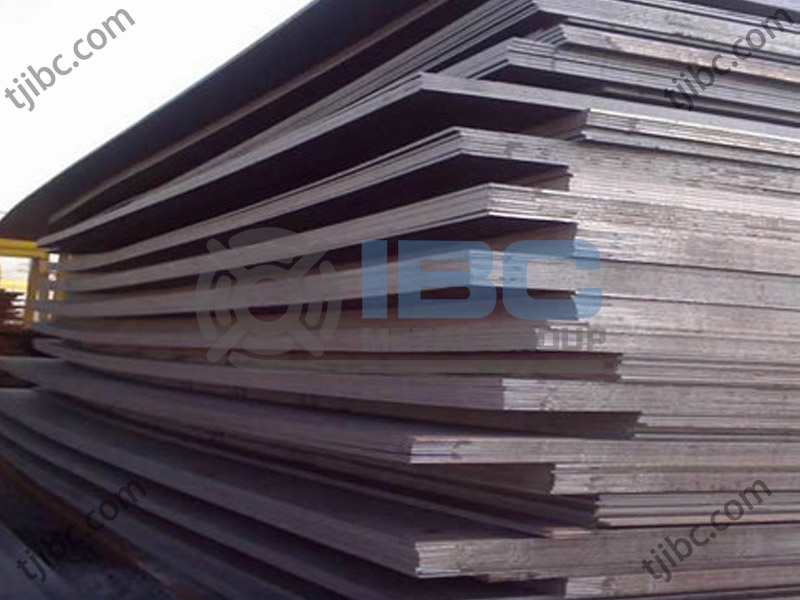
Contact with us today!