Copper alloy steel has many advantages such as high strength, good thermal conductivity and corrosion resistance. This material takes full advantage of the excellent strength of steel plates and the good thermal conductivity of copper alloys, providing an ideal solution for a variety of applications.
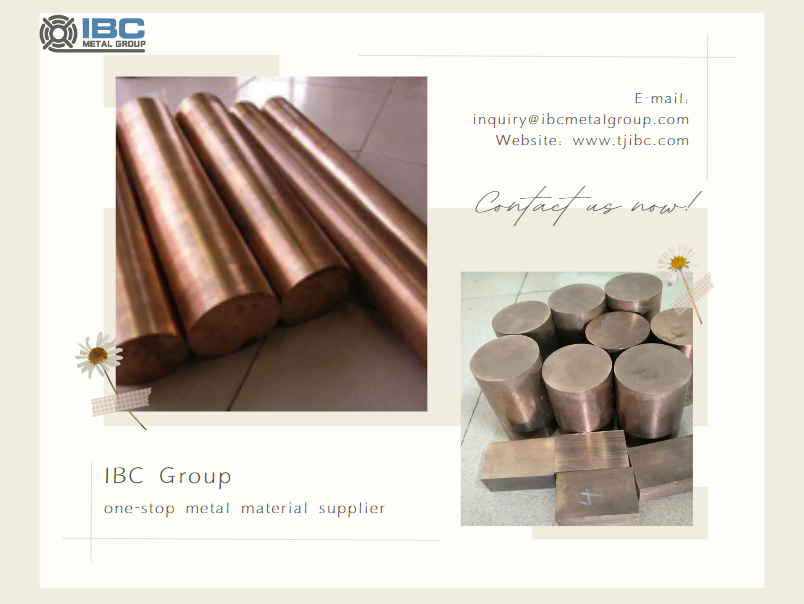
Advantages of Copper Alloy Steel
1. Good thermal conductivity: compared with ordinary steel, this steel has better thermal conductivity, making it perform well in occasions requiring efficient heat conduction.
2. Strong corrosion resistance: under high temperature and high pressure environment, it can still maintain good corrosion resistance, thus extending the service life of the equipment.
3. Good shaping and machinability: Its material is flexible, easy to process into a variety of complex shapes of components, to meet the needs of complex structural modeling.
4. Good oxidation resistance: it can effectively prevent the heat conduction material from being eroded by oxidation, so as to keep the performance of the equipment stable.
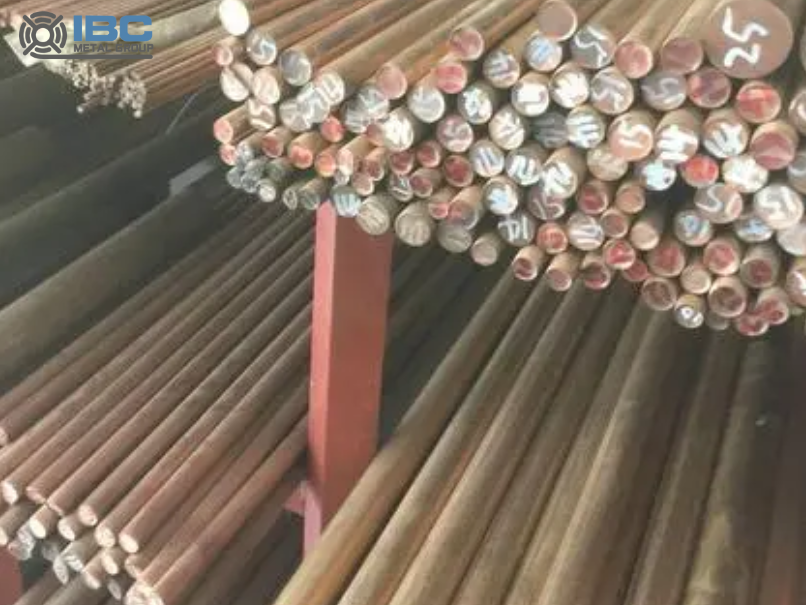
Production Process 1
1. Preparation and matching of raw materials
The production of copper alloy steel first needs to prepare suitable raw materials, mainly including copper, iron and other alloying elements (such as zinc, tin, nickel, etc.). The quality of raw materials directly affects the quality of final products. In the preparation process, it is necessary to accurately weigh various raw materials according to the predetermined ratio to ensure that the alloy composition meets the design requirements.
2. Melting and temperature control
The prepared raw material is placed in a melting furnace and melted by heating. In the melting process, the temperature in the furnace needs to be strictly controlled to ensure that the raw material is fully melted and not over-oxidized. At the same time, it is necessary to pay close attention to changes in the melting process and adjust the temperature and melting time in time to obtain a uniform alloy melt.
3. Add and stir alloying elements
During the smelting process, the required alloying elements are added according to the formula requirements. When adding, ensure that the element is evenly distributed in the liquid to avoid local concentrations that are too high or too low. At the same time, the composition of the molten liquid is more uniform by stirring. It is conducive to the formation of uniform alloy structure.
4. Test and adjust before casting
Before casting, the alloy molten liquid needs to be tested, including composition analysis, temperature measurement, etc. According to the test results, necessary adjustments are made to the molten liquid to ensure that the alloy composition and temperature meet the casting requirements.
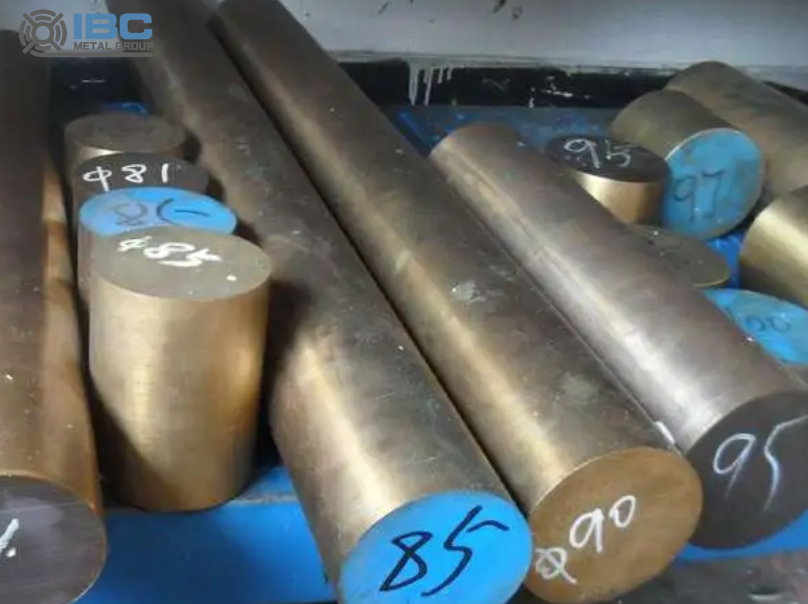
Production Process 2
5. Mold preparation and preheating
Before casting, it is necessary to prepare a suitable mold and preheat the mold. Preheating can eliminate water and gas in the mold and reduce pores and inclusions generated during the casting process. At the same time, preheating can also increase the temperature of the mold. It is conducive to the rapid solidification of the alloy melt in the mold.
6. Casting and cooling process
The adjusted alloy melt is poured into the preheated mold for casting. When casting, the speed should be kept moderate to avoid splashing and curling. After the casting is completed, the mold needs to be placed on the cooling equipment for natural or forced cooling, so that the alloy gradually solidifies and forms.
7. Follow-up treatment and testing
Follow-up procedures such as demoulding and cleaning are required for cooling alloy steel parts. For larger workpieces, heat treatment, machining and other steps may also be required to achieve a predetermined shape and performance. In the process of processing, it is necessary to pay close attention to the quality changes of the workpiece, and conduct quality testing in time to ensure that the product meets the design requirements.
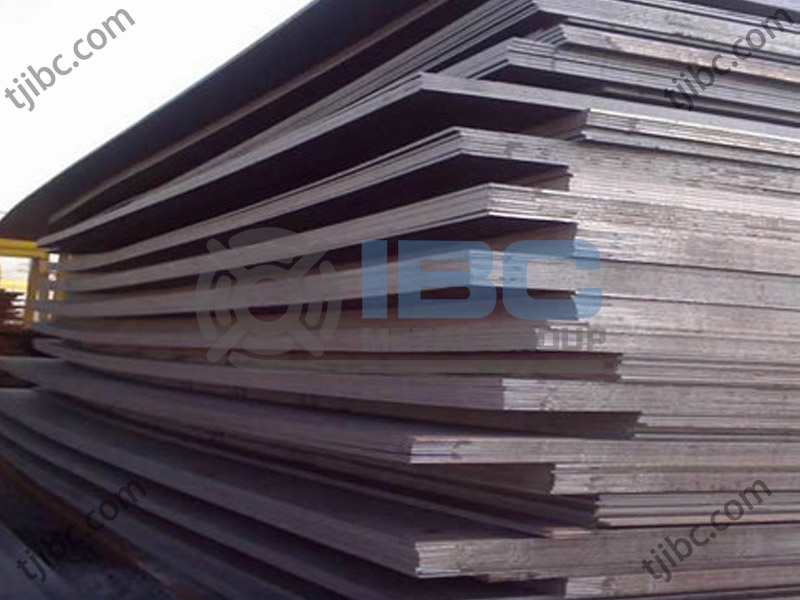
Contact with us today!