Hot rolled steel has become an indispensable metal material in many fields because of its excellent strength and toughness, plasticity and workability, weldability and connectivity, wear resistance and durability. With the continuous progress of technology and the constant change of market demand, its performance and application fields will continue to expand, and make greater contributions to the development of modern industry.
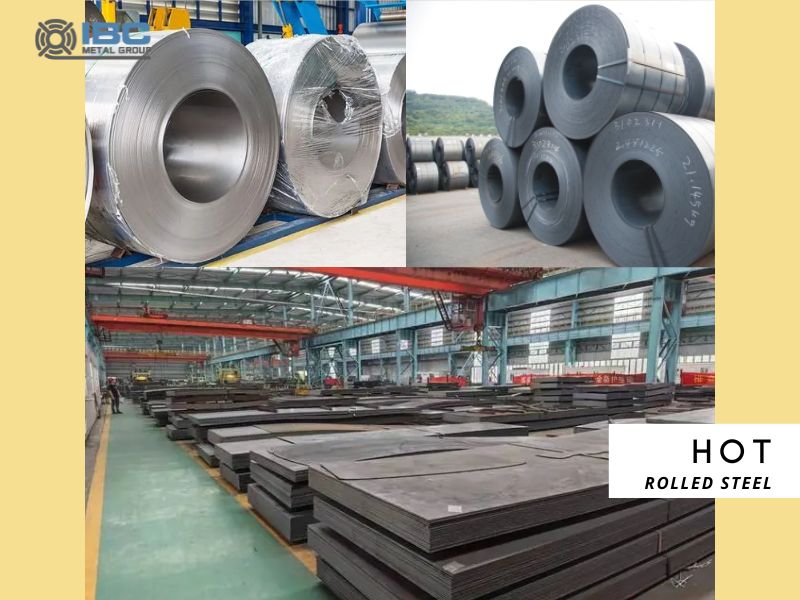
Performance Advantage
1. Plasticity and processability
It has excellent plasticity and processability. In the process of hot rolling, the steel will undergo plastic deformation due to high temperature. This can make its organizational structure more uniform, convenient for subsequent processing and forming. Therefore, workers can carry out cutting, bending, welding and other processes to process it into various shapes and specifications to meet different use needs.
2. Weldability and connectivity
Hot Rolled Steel has good weldability and connectivity. The moderate content of carbon, silicon and other elements in the steel makes the weld quality easy to control. The welding joint strength is high, and it is not easy to crack and other defects. In addition, it also has good connectivity. It can connect bolts, rivets and other materials to achieve structural integrity and stability.
3. Wear resistance and durability
This kind of steel has high wear resistance and durability. After hot rolling treatment, the surface of the steel forms a dense oxide film, which enhances its corrosion resistance. At the same time, its hardness and wear resistance are also relatively high. It can resist a certain amount of wear and impact, extend the service life.
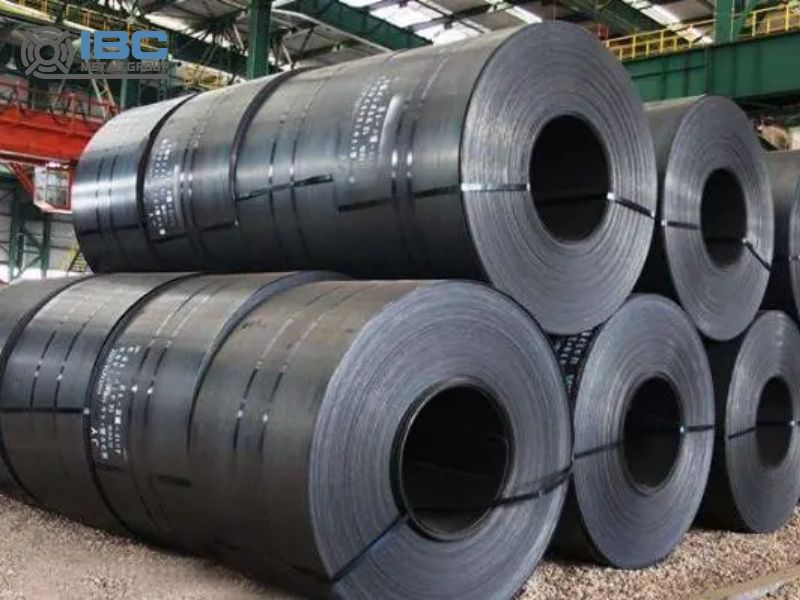
Production Process of Hot Rolled Steel 1
1. Raw material preparation:
The raw material of hot rolled steel is usually molten iron or scrap steel, which is first fed into the steelmaking furnace to be smelted into molten steel.
After refining molten steel, workers adjust its chemical composition to meet predetermined requirements.
2. Heating treatment:
The billet is fed into a heating furnace and heated to a high temperature that is close to melting but does not melt.
The purpose of heating is to make the temperature of the billet evenly distributed. And it can improve the plasticity of the metal, to create conditions for the subsequent rolling process.
3. Rolling process:
Workers will use a mill to roll the heated billets. A rolling mill is a set of rotating rolls with a specific roll shape that, through the gap between them, rolls the billet into the desired shape and size.
During the rolling process, the roll will apply pressure and shear force to the billet, causing it to gradually thin and lengthen, and finally get the hot rolled steel.
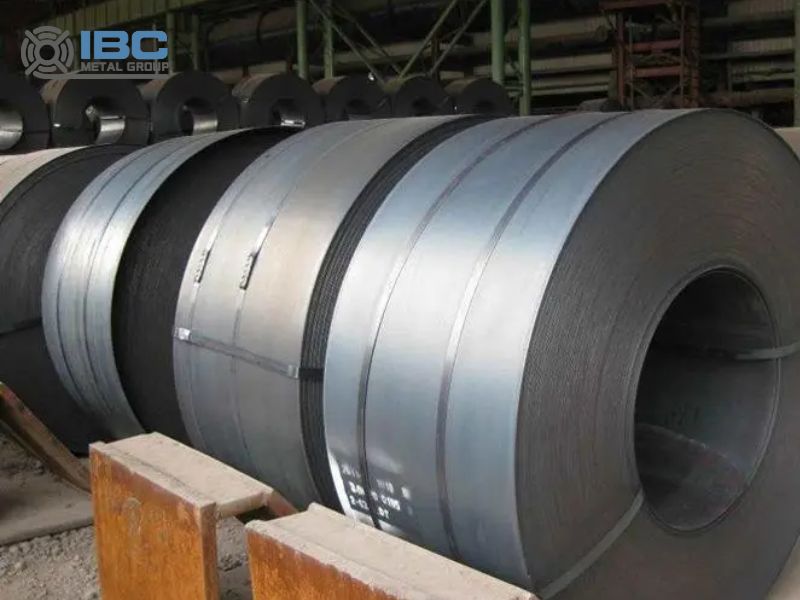
Production Process of Hot Rolled Steel 2
4. Cooling and winding:
The temperature of the rolling steel is still very high, so the worker needs to cool it quickly through the cooling device to prevent the internal structure of the steel from changing.
The cooled steel is usually rolled by a winder to facilitate transportation and subsequent processing.
5. Quality control and testing:
In the production process, workers need to control and test the quality of raw materials, semi-finished products and finished products.
This includes chemical composition analysis, mechanical properties testing, surface quality testing and other links to ensure that the quality of the steel meets the requirements.
6. Post-processing and application:
According to the specific requirements, it may also need to be cut, straightening, pickling, painting and other post-treatment.
This steel is widely used in construction, Bridges, vehicles, machinery, ships and other fields, is an indispensable important material in the manufacturing industry.
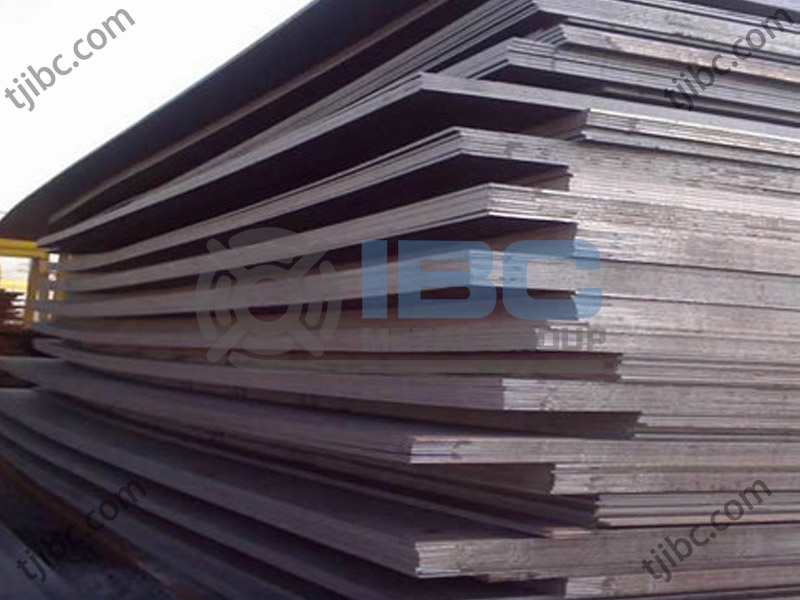
Contact with us today!