Main Characteristics and Classification of Pressure Vessel Plate
High strength: Pressure vessel plate usually has high yield strength and tensile strength. This ensures that it does not undergo plastic deformation or fracture under high pressures.
Good toughness: under low temperature or impact load, it can still maintain good fracture toughness to prevent brittle fracture.
Excellent corrosion resistance: steel plates of different materials can be selected according to the different media used. Such as stainless steel, low alloy steel, etc., to resist the erosion of the medium.
Good weldability: easy to weld with other metals or the same material to form a strong sealing structure.
Common materials include:
Carbon steel plate (such as Q235B, Q345R)
Low alloy high strength steel plate (such as 16MnDR, 09MnNiDR)
Stainless steel plate (such as 304, 316L)
Composite steel plate (such as base + laminated structure, for special media)
Pressure Vessel Plate Operation Guide
Material selection and purchasing
Clear requirements: According to the design pressure, temperature, media and other requirements of the pressure vessel, determine the required plate material, specifications and quantity.
Supplier selection: Select a qualified and reputable supplier, such as IBC Group. We can ensure that the quality of the board meets the relevant standards.
Quality inspection: The appearance inspection, size measurement and necessary physical and chemical property inspection are carried out when receiving the goods. Ensure that the sheet is free of defects and the performance indicators are up to standard.
Processing and manufacturing
Cutting and forming: Use suitable cutting tools (such as plasma cutting machine, laser cutting machine, etc.) for cutting plates. Workers will also make the desired shape by cold bending, hot bending and other methods.
Welding: Select the appropriate welding methods and materials to ensure that the weld quality meets the design requirements. This avoids the impact of welding defects on the performance of the container.
Heat treatment: According to the material and process requirements, the necessary heat treatment (such as annealing, tempering, etc.). This can improve the mechanical properties of the sheet and the properties of the welded joints.
Detection and test
Non-destructive testing: using ultrasonic testing, X-ray testing and other methods to detect internal defects in welds and plates.
Pressure test: Perform water pressure test or air pressure test to verify the tightness and bearing capacity of the container.
Other tests: as required, such as air tightness test, performance test after heat treatment, etc.
Care and Maintenance
Regular inspection and testing:
Perform regular visual inspection to see if there are signs of cracks, corrosion, deformation or leakage of the container plate.
Use non-destructive testing techniques (such as ultrasonic testing, X-ray testing, magnetic particle testing, etc.) to regularly inspect the inside of the container plate to find hidden defects or damage.
According to the use of the equipment environment and the characteristics of the medium, to develop a suitable detection cycle, and strictly in accordance with the plan.
Anti-corrosion treatment:
For pressure vessel plates exposed to corrosive environment, effective anti-corrosion measures should be taken. Such as coating anticorrosive coating, installing corrosion resistant lining or using corrosion resistant materials such as stainless steel.
Regularly check the integrity and effectiveness of anti-corrosion coatings and repair damaged or failed coatings in a timely manner.
Avoid overload and overvoltage:
Ensure that the pressure vessel is operating within the design pressure and temperature range. Avoid material strength loss and damage caused by overpressure and overtemperature.
Monitor the operating pressure, temperature and liquid level of the container to ensure that it is within a safe range.
Keep clean and dry:
Clean the pressure vessel plate and its surroundings regularly. Prevent the accumulation of impurities such as dust and oil, which affects the heat dissipation of the device and increases the risk of corrosion.
For containers with internal media prone to scale or sediment, workers should regularly clean and drain. This keeps the inside of the container clean.
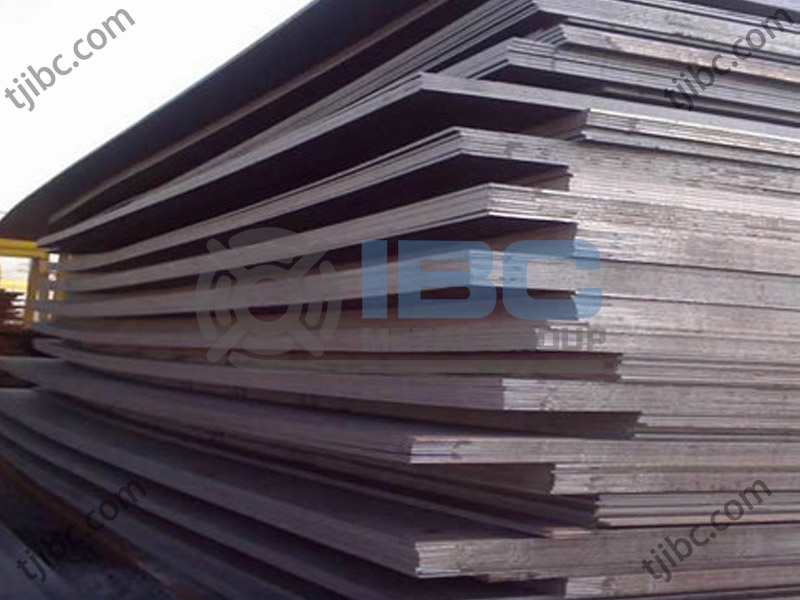
Contact with us today!