When we talk about SSAW Steel Pipe vs. LSAW Steel Pipe, we could learn it start from its name and manufacturing process. Let us take further on LSAW and SSAW pipes.
There are three types of producing processes for high quality steel pipes are being produced:
- SSAW (Spiral Submerged Arc Welded)
- LSAW (Longitudinal Submerged Arc Welding)
- and ERW (Electric Resistance Welding).
LSAW Steel Pipe. The two main types of SAW pipes are longitudinal (single or double straight seam weld, called DSAW). And spiral (SSAW, HSAW, or we call it SAWL). DSAW pipes have a seam weld on both the inside and outside of the pipe. While LSAW pipes have a single seam weld on the outer surface, longitudinal or cross sectional. LSAW pipes produced by molding steel sheets to a cylinder and joining the ends together by welding in a straight line. The LSAW pipe diameter range is normally from 16inch to 60inch (406mm to 1500mm). They have good performances on high pressure resistance, and low-temperature corrosion resistance.
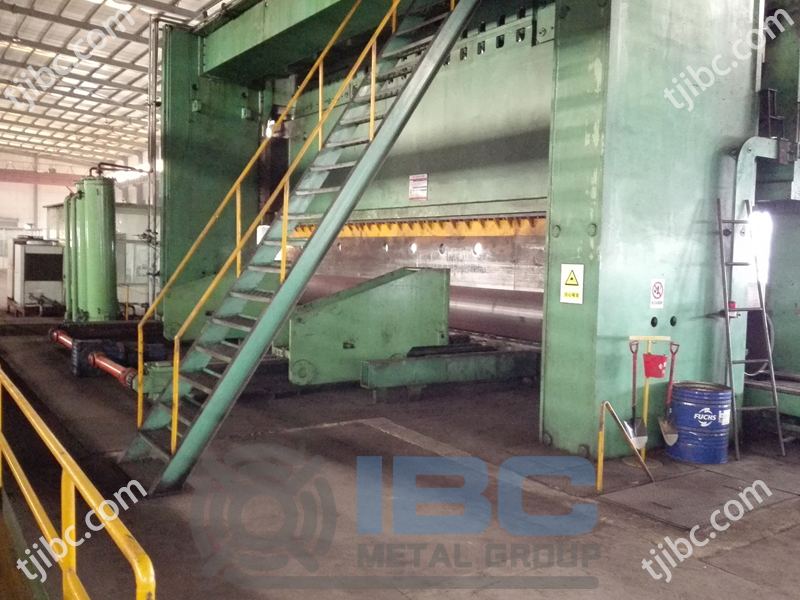
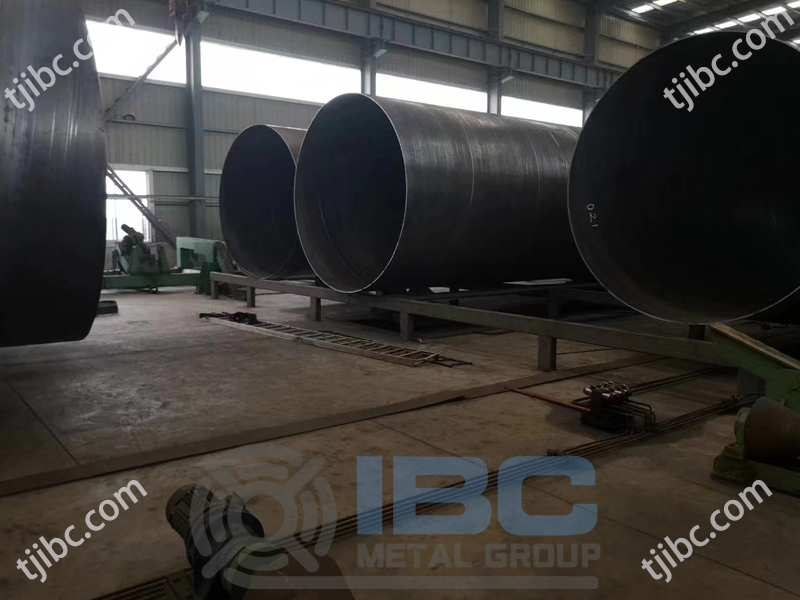
SSAW Steel Pipe. LSAW and SSAW employ the same manufacturing technology – JCOE process. The difference between SSAW pipes and LSAW pipes is that SSAW pipes welded in the helix or spiral position. While LSAW pipes welded in the longitudinal position. The process of making SSAW pipe involves rolling and welding a steel strip in such a way that the pivotal direction is oblique to the pipe center. Making a spiral seam along the weld seam. The SSAW pipe diameter range is generally 8 inch to 120 inch (406mm to 2540mm). One advantage of SSAW is the possibility to obtain different diameter of SSAW pipes from a standard size of steel strip. On the other hand, spiral welding seam length is quite longer than the pipe length. Making it more costly and prone to cracks, air holes, cinder inclusion, partial welding, and more.
ERW Steel Pipes. IBC offers ERW pipes as part of its comprehensive range of steel pipes. In the manufacturing process of ERW pipes, steel coils are first uncoiled, smoothed, cut. And then joined by high-frequency electrical welding (HFI & HFW) in order to form a pipe shape. With a price and performance advantage over seamless pipes, ERW pipes are available in sizes ranging from ½ inches to 20 inches (12mm to 508mm).
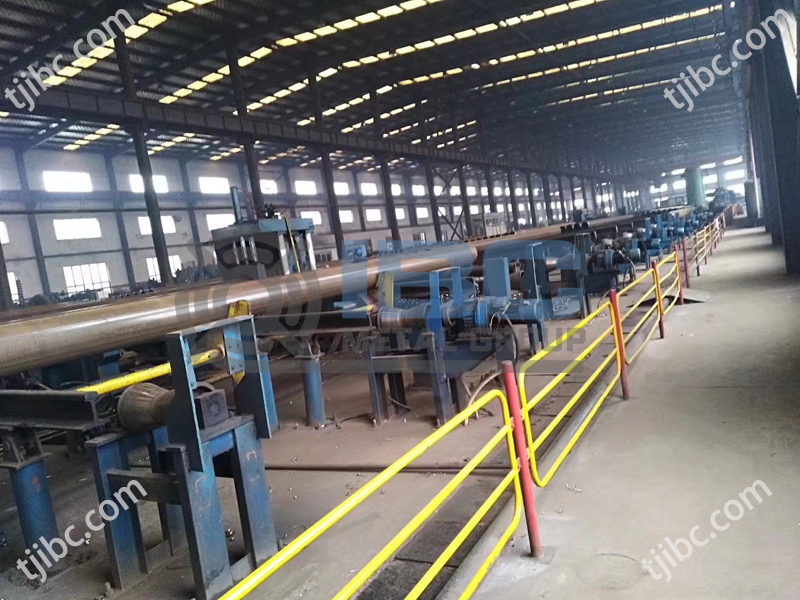
Usage of SSAW Steel Pipe vs. LSAW Steel Pipe
HSAW and SSAW spiral weld pipes mainly used in non-critical applications such as for water distribution. IBC recommends the SSAW pipes as King Piles for its Combination Walls and also as Dredging Pipe. LSAW Pipes demonstrate better performance than SSAW Pipes due to their lower residual stress, uniform expansion process, fewer welding lines and higher geometrical accuracy. Additionally, testing of the quality of LSAW pipes using steel plates is done through non-destructive procedures, while that of SSAW pipes using hot-rolled coils is achieved with destructive methods such as x-rays. This is because the welding process of LSAW pipes allow pre-checks before molding which isn’t possible in SSAWs due to simultaneous molding and welding.
IBC however can supply pipes between 1 inch to 167 inch (21mm up to 4267mm) in diameter and thicknesses between 3/32 inch to 4 inch (2.1mm up to 100mm). Largest diameters and thickness of IBC Steel Pipes manufactured using LSAW which highly recommended for load bearing piles, combination wall piles and other applications. In the oil and gas industry, large-diameter API 5L LSAW pipes used to transport hydrocarbons over long distances efficiently.