Operating Steps
The steel to be processed is placed on the work table and accurately positioned by the positioning device.
Adjust the position and spacing of rollers according to the required bending radius and Angle.
Start the cold bending mechanical equipment. And adjust the speed and cold bending force of the equipment according to the process requirements.
During the operation of the equipment, workers will control the feed of steel through manual control or automatic equipment to ensure the stability and accuracy of the processing process.
The steel is processed step by step, with the initial bending and then the bending corrected until the desired bending shape is achieved.
In the process of processing, it is necessary to pay close attention to the deformation and stress of the steel to avoid excessive processing leading to material rupture or fracture.
After the processing is completed, shut down the equipment for visual inspection and clean up the processing residue and impurities.
Quality inspection of the cold-formed steel to ensure that its dimensions, angles and surface quality meet relevant standards or customer requirements.
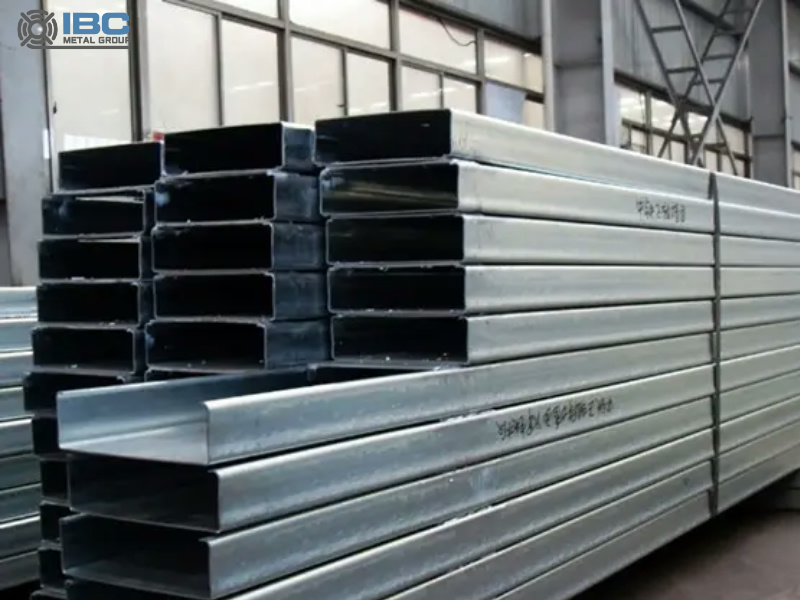
Performance Profile of Cold-Formed Steel
First of all, its section design is economical and reasonable, which can fully save materials. Its section shape can be customized according to actual needs, so as to achieve structural rationalization. So that the section coefficient per unit weight is higher than that of hot rolled section steel. Under the same load conditions, this type of steel can significantly reduce the weight of members and further reduce material consumption.
Secondly, it has a wide variety of varieties. And it can produce various profiles with uniform wall thickness and complex cross-section shapes that are difficult to manufacture with general hot rolling methods. This makes it widely used in various fields, including but not limited to production sectors such as construction, railway vehicles, automobiles and ships, for the production of structural parts and auxiliary parts.
In addition, the surface of the cold-formed steel is smooth, good appearance, and accurate size. Workers can flexibly adjust its length according to needs, all in fixed size or double size supply. This can improve the utilization rate of materials.
In terms of strength utilization, it has significant advantages over hot rolled section steel. Under the same section area, its radius of rotation can be increased by 50% ~ 60%. And the section moment of inertia can be increased by 0.5 ~ 3.0 times. This enables this type of steel to make more reasonable use of material strength and improve the stability and safety of the structure.
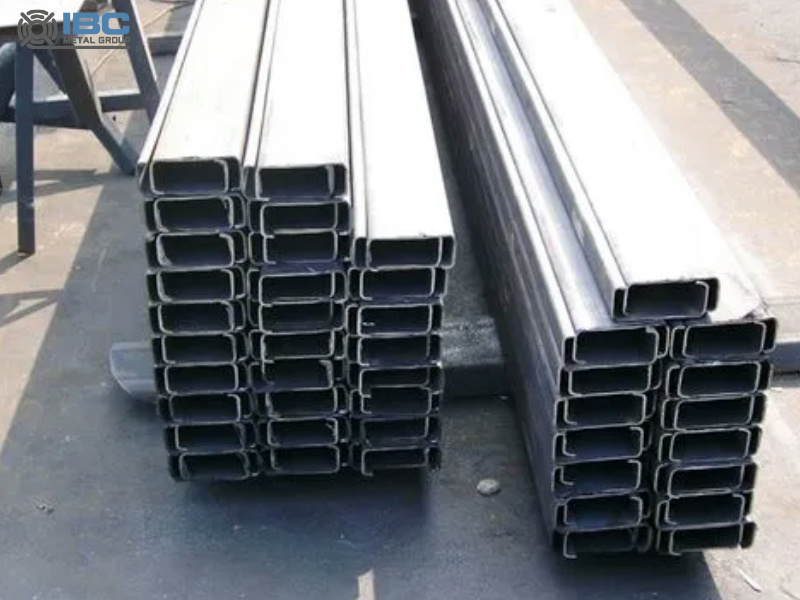
Applications of Cold-Formed Steel
1. Construction field
Its application in the construction field is very common. It is often used in light steel structure, roof truss, floor, wall beam and so on. In addition, the construction of light steel structure system is also inseparable from this kind of steel. Including main load-bearing structures such as walls, roofs, floor frames, beams, columns. And secondary structures such as doors and Windows frames and stairs. Its high strength, excellent plastic deformation ability and light weight characteristics make it have significant advantages in the field of construction. It can meet the design requirements of modern buildings, and make the building structure more stable and safe.
2. Machinery manufacturing field
Cold-formed steel also plays an important role in the field of machinery manufacturing, which can manufacture mechanical parts and equipment such as machine frames, brackets, and spring seats. Its lightweight and flexible characteristics can meet the needs of complex shapes. And the manufacturing process is simple, low cost, high strength and strong durability.
3. Automotive sector
In the automotive industry, it is suitable for the manufacture of car chassis, doors, roofs, front and rear bumpers and other components. Its high strength, light weight and excellent corrosion resistance make cold-formed steel an ideal choice for the automotive industry. And it can improve the stability and safety of the entire vehicle structure.
4. Aerospace
It is also increasingly used in the aerospace field. It can manufacture aerospace devices, such as aircraft wing spars, spacecraft shells, etc. Its high strength and good plastic deformation ability can meet the stringent requirements for material properties and safety in the aerospace field.
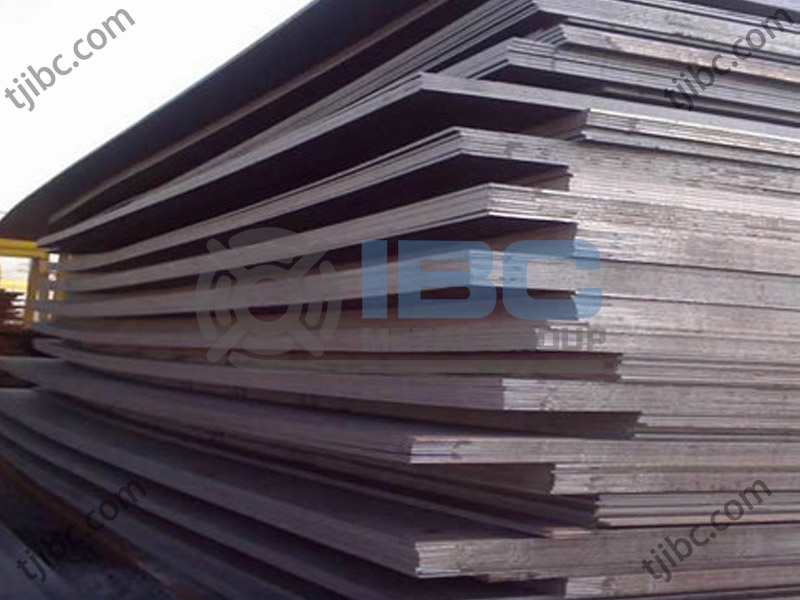
Contact with us today!