Process 1
Raw material preparation: The main raw material of the cold drawn bar is carbon steel or alloy steel. Workers need to ensure that raw materials meet the standards.
Hot rolling: After the raw material is preheated, it enters the hot rolling mill for primary rolling. Hot rolling is the process of heating raw materials to soften them and then rolling them through a roller mill.
Pickling: The surface of the billet after hot rolling may have impurities such as oxide and rust. The factory needs to be pickled. Pickling involves dipping a billet into an acid solution so that it reacts chemically with the oxide on the steel surface. This will remove impurities.
Cold rolling: The billet after pickling goes into the cold rolling mill for rerolling. Cold rolling is to cool the billet to room temperature and then roll it through a roller mill to further increase the strength and hardness of the steel, while making its surface smoother.
Process 2
Straightening: the steel after cold rolling may have some bending or deformation. So workers need to straighten it to restore it to the specified shape and size.
Annealing: Cold rolled steel due to cold processing will produce a certain residual stress, need to be annealed. Annealing is to heat the steel to a certain temperature and then slowly cool it so that the residual stress inside is released, thereby improving the plasticity and toughness of the steel.
Bright treatment: After annealing, the steel is brightened to make its surface smoother and brighter. Polishing usually includes polishing and shot peening.
Testing and packaging: The finished rods need to undergo strict testing. This ensures that its quality meets the standard requirements. Qualified products will be packaged, usually in plastic film packaging or wooden cases. Thus protecting the steel from the external environment.
Applications of Cold Drawn Bar
Mechanical manufacturing: It can manufacture various mechanical parts, such as bolts, nuts, gears, shaft pins and so on. Its high strength and good plasticity allow these parts to remain stable under high loads and complex stresses.
Construction industry: In the field of construction, it can manufacture a variety of structural supports and fixed parts, such as steel bars, supports, hangers, etc. Its structural stability and corrosion resistance allow it to provide reliable support and fixation in building structures.
Automobile manufacturing: Cold-drawn bars occupy an important position in the automobile manufacturing industry. It can manufacture car parts such as wheels, brake system parts and axle pins. Aerospace: In the aerospace sector, it can manufacture a variety of key components, such as aircraft landing gear, rocket engine parts, etc. Their superior performance allows these components to remain stable in extreme environments.
Petroleum and Chemical: In the petroleum and chemical industry, it can manufacture a variety of pressure vessels, pipe supports and fasteners.
Performance of Cold Drawn Bar
High strength: The cold drawing process refines the grain of the steel, thereby improving the strength of the steel.
Good plasticity: This kind of bar in the cold processing process, through straightening and annealing treatment, so that its internal residual stress is released, improve the plasticity and toughness of steel.
High precision: Cold drawing molding process makes the dimensional accuracy and surface quality of steel improved to meet the needs of high-precision parts manufacturing.
Corrosion resistance: Cold drawn bars made of partially alloyed steel have good corrosion resistance and can remain stable in harsh environments.
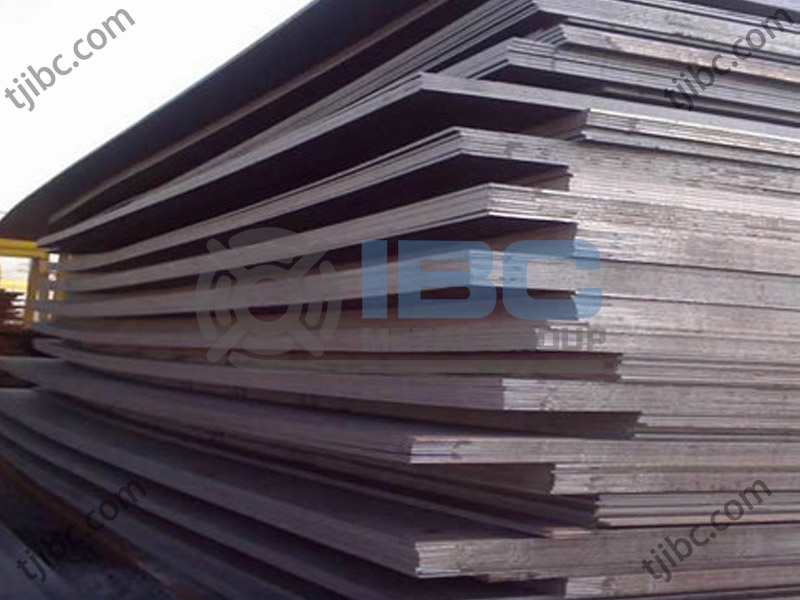
Contact with us today!