Drilling and milling machine is a set of drilling, milling, boring, grinding and other functions in one of the equipment, can process small and medium-sized parts.
The numerical control system can recognize these codes. And it can control the speed of the spindle of the machine tool, the speed of the feed movement, and the automatic clamping of the tool. It can also control the loosening and clamping of the workpiece. So as to complete the whole processing of the workpiece.
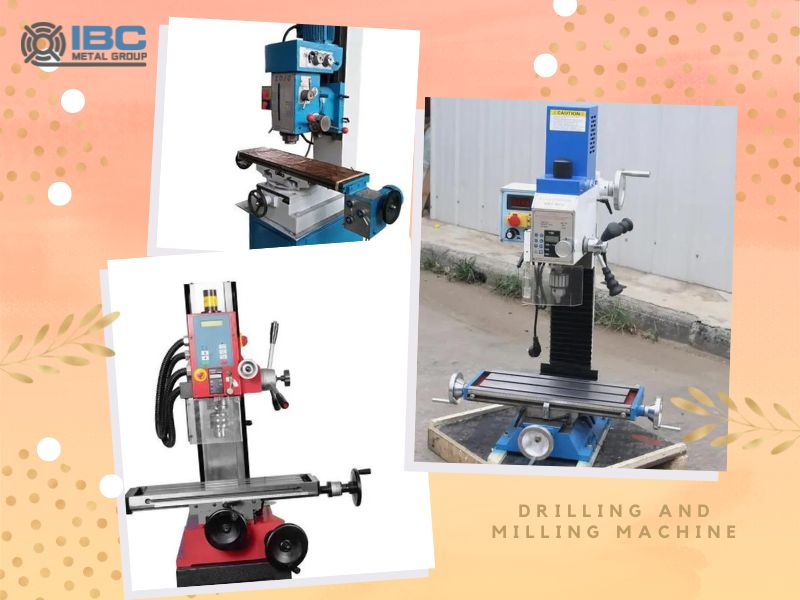
What is a Drilling and Milling Machine
It is mainly composed of four parts: mechanical bed, numerical control unit, G code and servo drive system. Among them, the mechanical bed body includes the bed body, ball screw, linear guide rail and transmission system. G code records a variety of processing information, such as parts processing path, process parameters and tool movement.
And the servo drive system is composed of a servo power supply, a servo driver and a servo motor device, which is responsible for executing the commands of the CNC system.
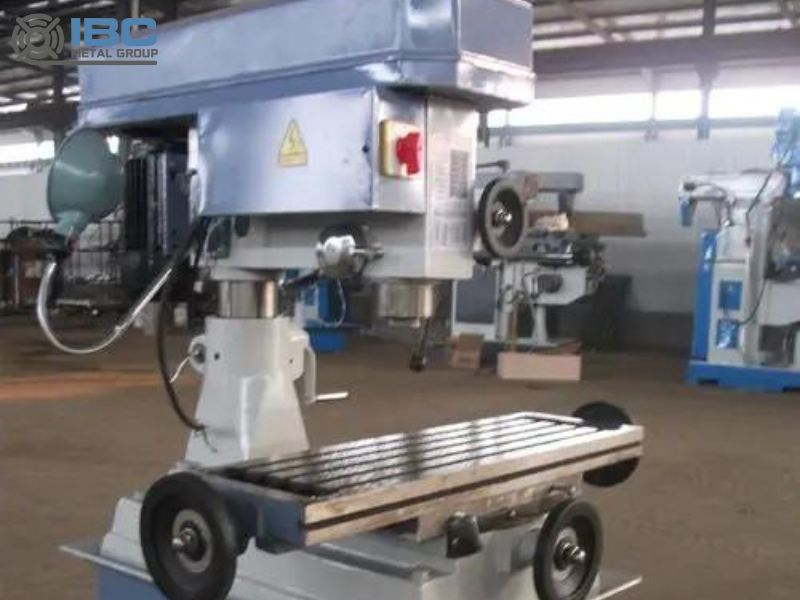
Operation Procedures and Specifications 1
1. Check the state of the machine tool: ensure that the machine is in good working condition. All components are not damaged, and the lubrication system is normal.
2. Workpiece preparation: The worker will put the workpiece to be processed on the work table and fix it firmly with fixtures or other devices. This ensures that the workpiece will not move during machining.
3. Tool selection: Select the right drill, milling cutter or other cutting tool according to the processing requirements, and install it on the spindle.
4. Turn on the power: Need to make sure that the power supply of the machine is on. And then turn on the main power switch.
5. Start the spindle motor: press the start button to make the spindle motor start to rotate. At this time, it is necessary to pay attention to whether the rotation direction of the spindle meets the processing requirements.
6. Adjust parameters: Adjust the speed and feed speed of the spindle according to the material of the workpiece, the diameter of the tool and the processing requirements.
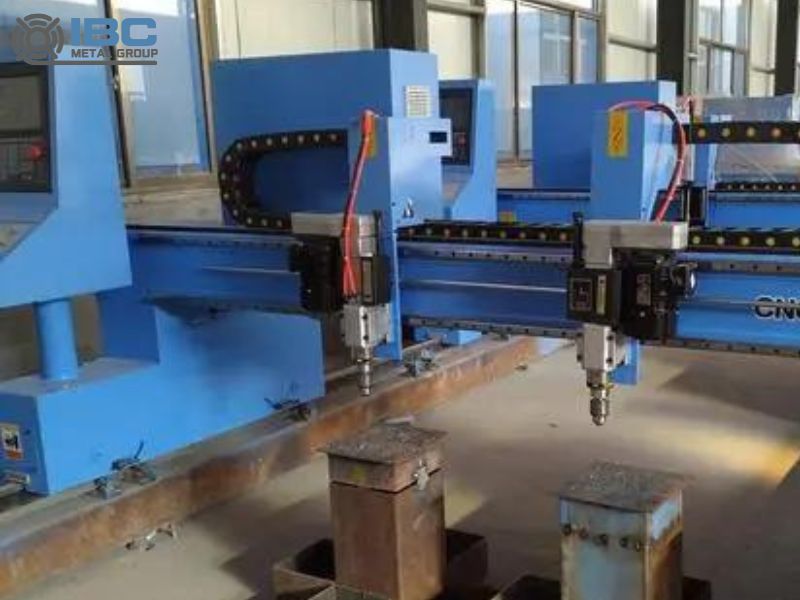
Operation Procedures and Specifications 2
7. The use of cutting fluid: During machining operations such as drilling or milling, workers inject the right amount of cutting oil into the cutting area. This can play a role in cooling and lubrication, improve the service life of the tool and processing quality.
8. Observe the cutting process: In the processing process, pay attention to observe the cutting process, observe the production of chips. And clean up in time to avoid the accumulation of chips affecting the processing effect.
9. Adjust the drilling and milling machine: According to the need, workers can adjust the position and Angle of the workbench to achieve different processing needs.
10. Stop the spindle motor: After the processing is completed, stop the rotation of the spindle motor first and wait for the spindle to stop completely.
11. Turn off the power: After the spindle stops, turn off the main power switch and disconnect the power of the machine.
12. Clean the machine tool: clean the cuttings and debris on the workbench to keep the machine clean.
13. Tool preservation: Store the used tool properly for next use.
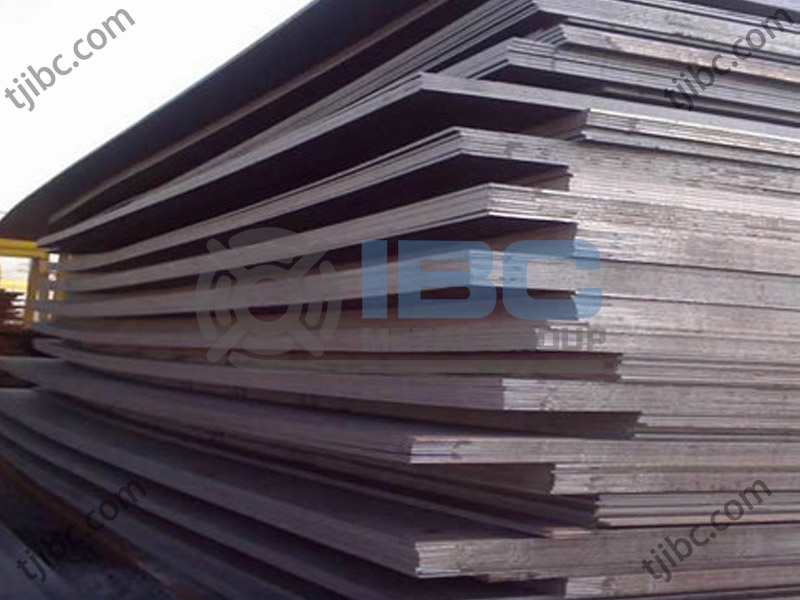
Contact with us today!