Weather Resistance Coating Seamless Pipe widely used in overhead pipelines, service life of more than 20 years. The coating has three layers. At bottom: it is epoxy zinc-rich primer. The middle layer: Epoxy micaceous iron oxide intermediate coating. And topcoat is polyurethane paint. Good corrosion resistance and weather resistance make it widely used in aerial pipeline with more than 20 years’ service life.
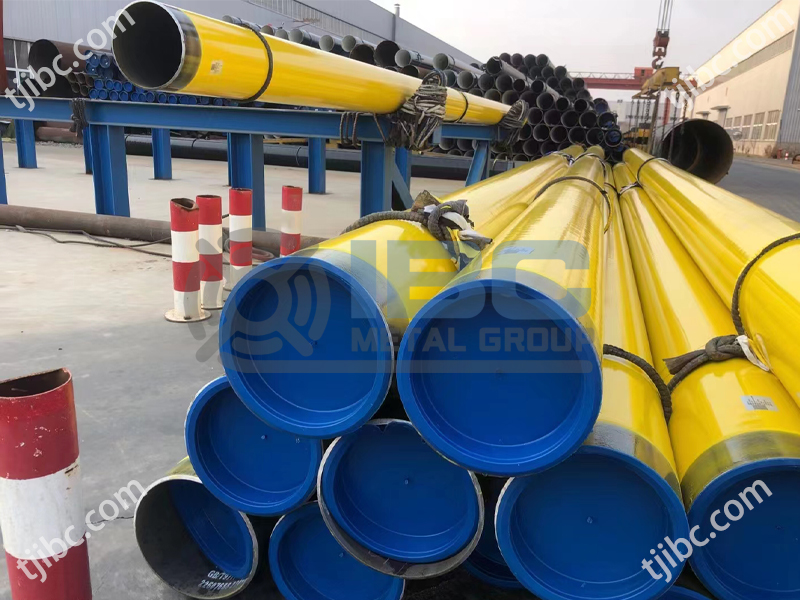
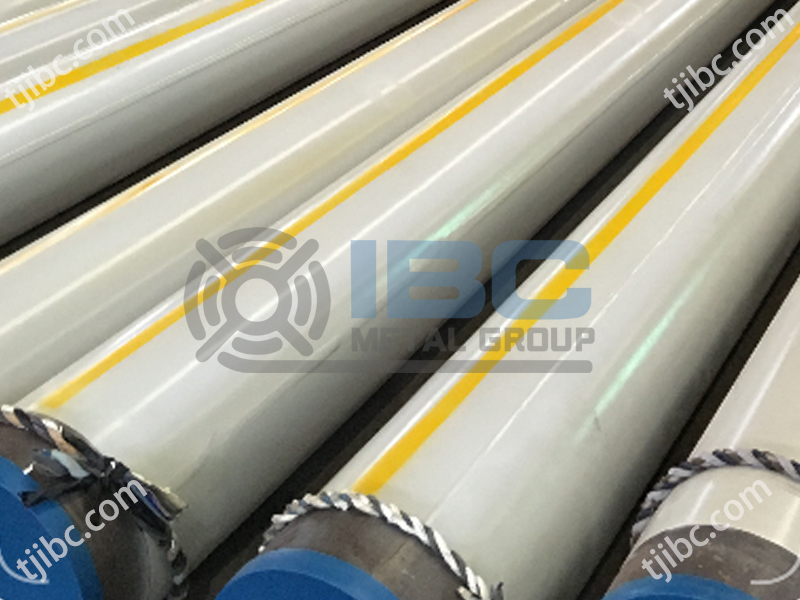
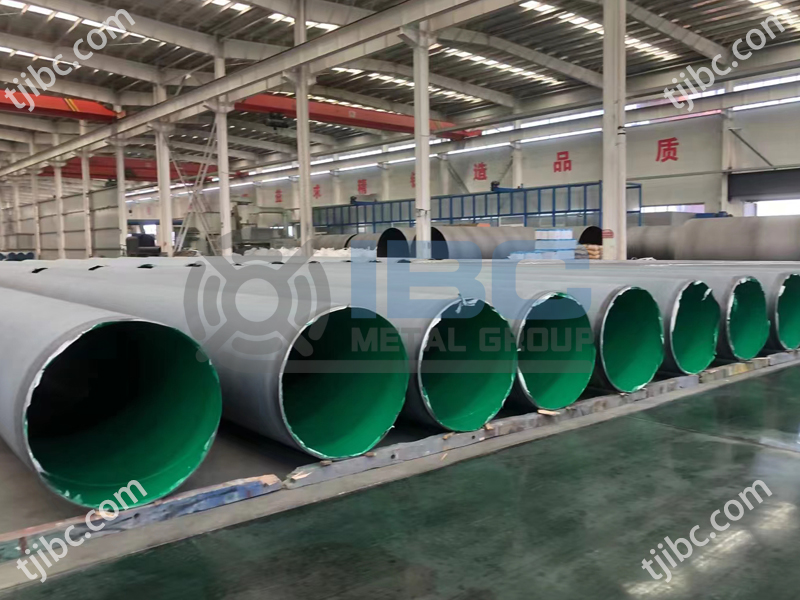
The anti-corrosion coating of seamless steel pipe is a common way to prevent rust. This is achieved by having the surface of the steel pipe, which has been cleaned of rust. Coated with paint to form a barrier between it and corrosive media. There are numerous types of such coatings, whose specifications vary depending on their purpose. Coating technology forms an insulating layer over metal surfaces so as to stop metal. And electrolytes from coming into contact and creating a high resistance that inhibits electrochemical reactions.
Commonly Used for Weather Resistance Coating Seamless Pipe
Epoxy Anti-Corrosion Coating Seamless Pipe
It has the advantages of strong adhesion, acid and alkali resistance, and low shrinkage rate. Which makes epoxy resin anticorrosion coatings widely used for the anticorrosion of pipeline interiors and exteriors. There are disadvantages to the paint film, however, including its easy powderability and poor weather resistance. Water resistance of the coating is poor when the curing treatment is poor. And it becomes easy to whiten and become brittle when the curing treatment is poor.
Asphalt Anti-Corrosion Coating Pipes
Asphalt coating is simple to obtain and inexpensive, offering resistance to acidic and alkaline corrosion at room temperature. Additionally, it dries quickly, features good elasticity and frequently utilized as a waterproof barrier. Composed of hydrocarbons, asphalt is soluble in certain organic solvents yet not invulnerable to oxidation or low temperatures. Products like coal epoxy coal tar pitch, coal tar enamel paint. And petroleum pitch paint modified bitumen paints which aid in improving the film’s hardness, cold-tolerance, and adherence. This covers main use of asphalt coating—protecting underground pipelines from water damage and corrosion—and typically with glass cloth according to requirements.
Urushiol Anti-Corrosion Coating
Urushiol paint made of raw lacquer through dehydration and polycondensation and diluted with organic solvent. Compared with raw lacquer, it has less toxicity and quicker drying. Urushiol paint is resistant to acid, alkali, ammonia and water. It can be used as anti-corrosion paint for ammonia gas, ammonia water, chlorine gas and hydrogen sulfide gas. As well as moisture-proof and anti-corrosion paint for underground pipelines.
Acrylic or Polyurethane Anti-Corrosion Coating
Polyurethane coatings provide acid, alkali, oil, water and abrasion resistance when used as anti-corrosion coatings. There are three types: one-component moisture-curing type, two-component catalyst curing type and hydroxyl curing type. To enhance certain properties, they can be blended with epoxy resin and asphalt. The self-made polyurethane asphalt paint quickly cured and resistant to water, making it ideal for the protection of inner walls of pressure water pipelines at power stations and underground steel pipes at oil fields’ water injection wells.
Olefin Resin Anti-Corrosion Coating
Olefin resin anti-corrosion coatings mainly made of resins containing ethylene or propylene molecular structure as raw materials, plus modified resins, fillers, etc., and have good water resistance, acid resistance, alkali resistance and weather resistance.
Perchloroethylene Resin Anti-Corrosion Coating
Perchloroethylene coating is a kind of coating widely used in chemical pipelines to prevent atmospheric corrosion. The disadvantage is that it has poor adhesion with the pipeline. In order to improve its adhesion, epoxy resin commonly used to modify it. And certain results have been achieved.
Chlorinated Rubber Anti-Corrosion Coating
The chlorinated rubber obtained by the chlorination reaction of natural rubber or synthetic rubber dissolved in an organic solvent to obtain a chlorinated rubber coating. Among its advantages are its resistance to corrosion from diluted acids and alkalis, its permeability resistance, and its flame retardant properties.
High Temperature Anti-Corrosion Coating
High-temperature anti-corrosion coatings are mainly silicone resin heat-resistant coatings. Its operating temperature can reach 500° C. Its advantages include good water resistance, corrosion resistance, and weather resistance. The disadvantages are that the adhesion is poor, the price is high, and the products containing lead powder have to be dried.
Zinc – Rich Anti-Corrosion Coating
Zinc-rich coatings come in two varieties: inorganic and organic. The former made from zinc powder, sodium silicate and a curing agent, while the latter employs resin – primarily epoxy – as well as zinc powder. Both types use cathodic protection to guard against corrosion caused by water, seawater, oil and the marine atmosphere; however, acid or alkali conditions can render them ineffective.
Cement Mortar
To prevent corrosion caused by direct contact between the medium and the pipeline, cement mortar commonly used as lining coating for water supply pipelines. Aside from its economical nature and pollution-free nature, it has a number of modified varieties. Including polymer cement mortar, which applied to pipelines containing hot water, sea water, and sewage, and which inhibit microorganisms and bryophytes from growing.
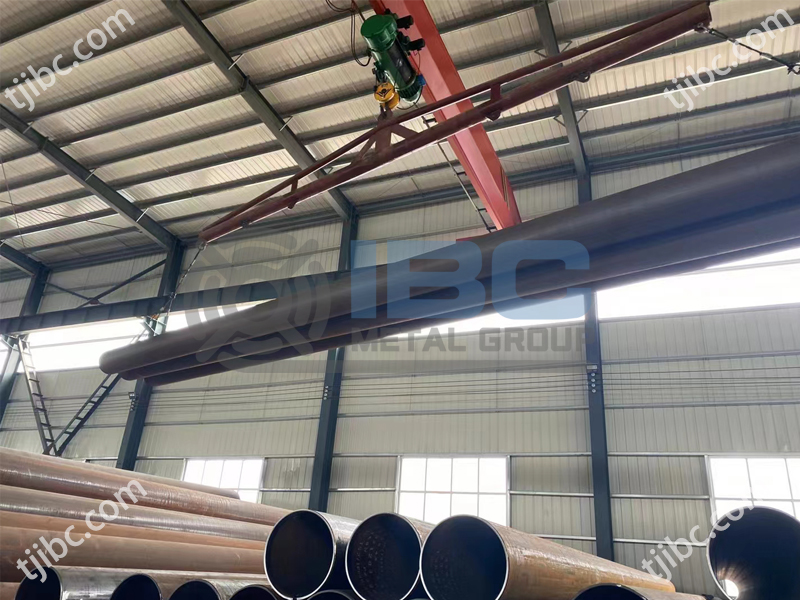