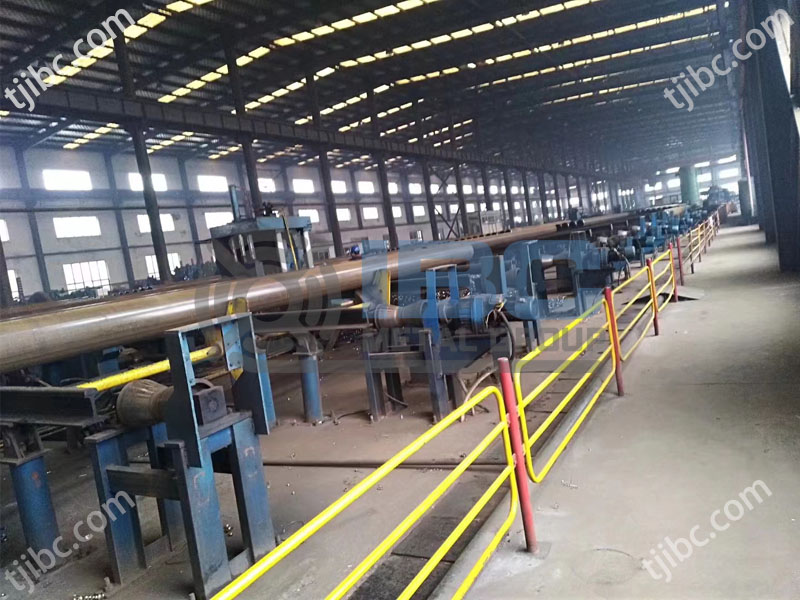
21.3mm ERW Steel Pipe Manufacturer
21.3mm ERW steel pipe is the smallest standard size of ERW Steel Pipe. But we could also manufacture smaller sizes for your projects use. Steel plate welding into a round pipe is classified as high frequency resistance welded pipes (ERW welded pipes), straight seam arc welded pipes (LSAW welded pipes), and spiral welded pipes. A wire pipe, also called pipe pipe, is relatively thick, and can also be used as a water gas pipe. Pipeline pipe, also known as wire pipe, is thin and can only threaded.
ERW stands for “high frequency resistance welding steel tube”, which differs from traditional welding process, as the weld line derived from melting the base material of the steel belt body; yielding a stronger mechanical strength. Boasting high production efficiency and low cost, this process promotes material saving and automation; making it widely adopted in aviation, aerospace, energy, electronics, automotive, light industry and other industrial domains – one of the imperative welding processes.
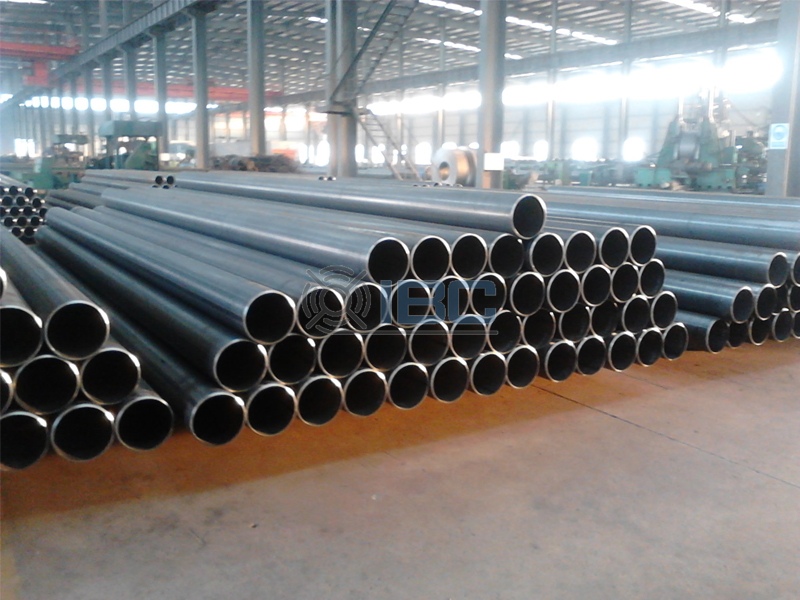
ERW Steel Pipe Specification:
- Diameter: 21.3mm
- Wall Thickness: 3.5mm
- Lengh: 12M
- Steel Grade: Grade B
- Surface: Fusion bond Epoxy coating, Coal Tar Epoxy, 3PE, Vanish Coating, Bitumen Coating, Black Oil coating as per customer’s requirement
- Standard: API5L, ASTM A53 GR.B, ASTM A178, ASTM A500/501, ASTM A691, ASTM A252, ASTM A672, EN 10217; API SPEC 5L ISO 3183 GB/T 9711.1 GB/T 9711.2 GB/T 9711.3
- Ends: Square Ends (straight cut, saw cut) Beveled Ends
Supply Range of ERW Steel PIpe
- Diameter: 21.3mm – 660mm
- Wall Thickness: 1.0mm ~ 16.00mm
- Lengh: 0.5M ~ 12.0M or Customized.
- Standard: API5L, ASTM A53 GR.B, ASTM A178, ASTM A500/501, ASTM A691, ASTM A252, ASTM A672, EN 10217; API SPEC 5L ISO 3183 GB/T 9711.1 GB/T 9711.2 GB/T 9711.3
- Surface: Fusion bond Epoxy coating, Coal Tar Epoxy, 3PE, Vanish Coating, Bitumen Coating, Black Oil coating as per customer’s requirement
- Ends: Square Ends (straight cut, saw cut) Beveled Ends
ERW Steel Pipe Producing Process
Precision welded tubes created using the High Frequency Induction Welding Process, better known as ERW. The slits from the small coils are cut to the desired size and brought to Steel Tubes Manufacturing Mills. Loaded onto Pay off Reels, they pass through a looping cage and a series of forming rolls which bend the strip into its tubular shape with edges touching.
Heat then applied to these edges up to the required Welding Temperature via High Frequency Induction before it Flash removed on both the interior and exterior surfaces with Scarfing Tools. The pipe passes through a coolant tank to cool down, followed by a sizing section where its outer diameter is maintained and straightened using Turk Heads. From here, it moves onto the cut off carriage for cutting without stopping the mill and rolls out on a conveyor, stopping at the end when it’s ejected into collection pockets.
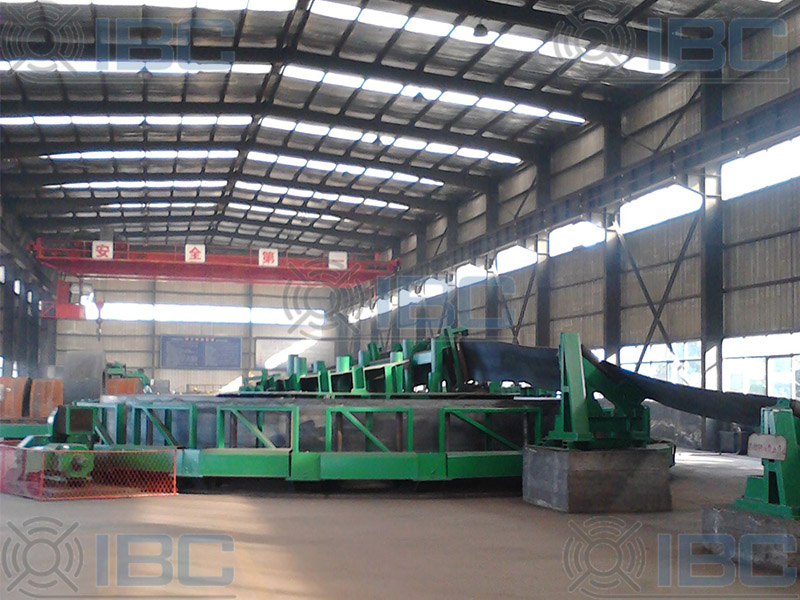
Contact with us today!