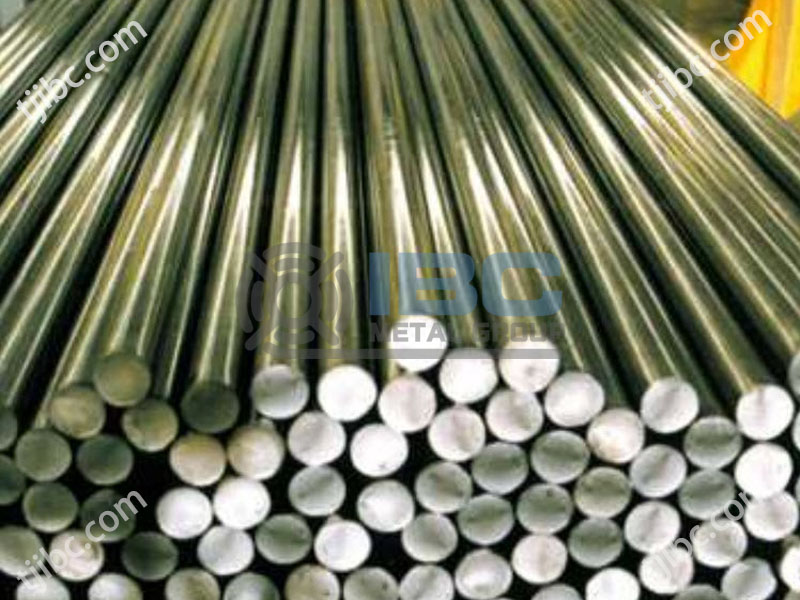
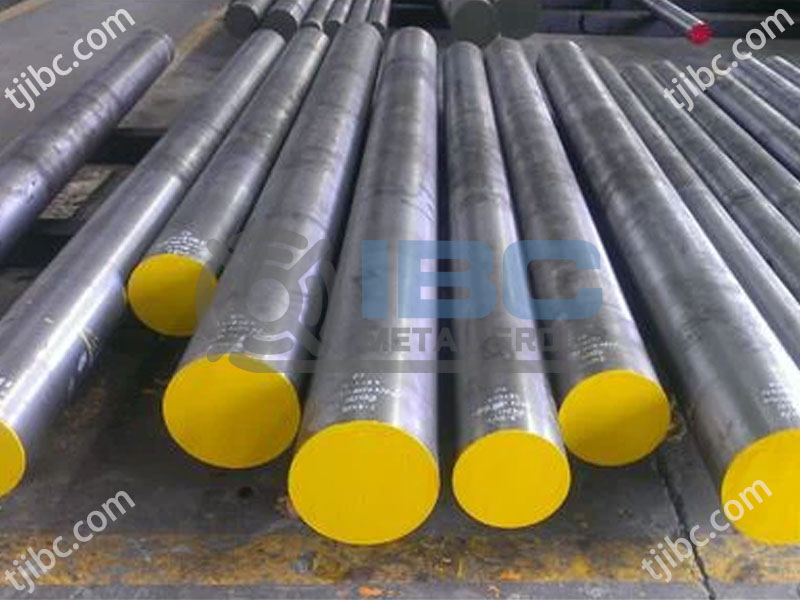
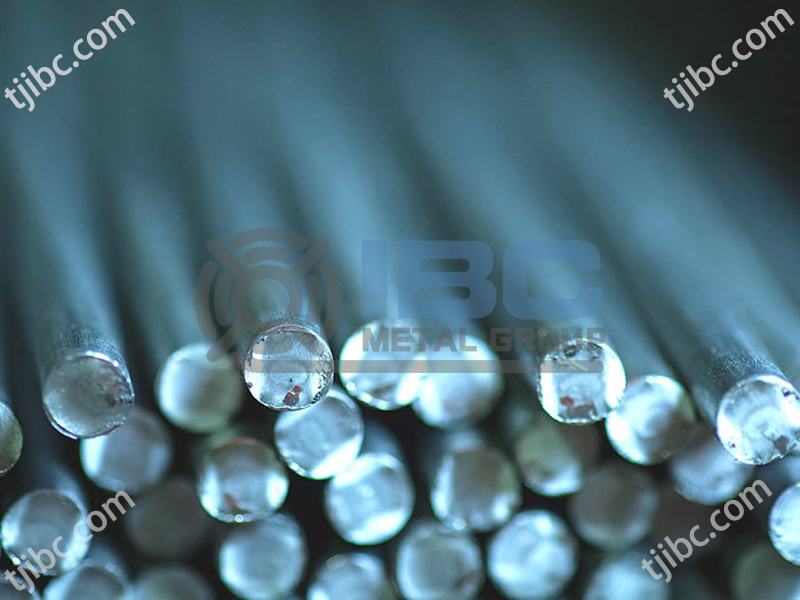
Hot rolled 4340 alloy steel bar is a nickel-chromium-molybdenum medium carbon alloy steel that is known for its toughness. This steel grade also has good ductility and high strength. Hot rolled 4340 bar has good impact, and wear resistance in the hardened condition. This grade is often used because it provides hardenability and strength that other steel grades cannot provide. IBC Metal Group supply many diameters of 4340 hot rolled steel to meet the market demands. We also supply 4340 steel bar to various industries like aerospace, automotive, and tooling.
AISI Alloy 4340 Steel Supply Range
- 4340 Steel Round Bar: diameter 8mm – 3000mm
- AISI 4340 Steel Plate: thickness 10mm – 1500mm x width 200mm – 3000mm
- 4340 Steel Grade Square: 20mm – 500mm
- Surface Finish: Black, Rough Machined, Turned or as per given requirements.
For More Information, Please Send Your Inquiry! Email us today!
What is AISI 4340 Steel?
AISI 4340 steel is a medium carbon, low alloy steel known for its toughness and strength in relatively large sections. It is also one kind of nickel chromium molybdenum steels. 4340 alloy steel is generally supplied hardened and tempered in the tensile range of 930 – 1080 Mpa. Pre hardened and tempered 4340 steels can be further surface hardened by flame or induction hardening and by nitriding.
The 4340 steel has good shock and impact resistance as well as wear and abrasion resistance in the hardened condition. AISI 4340 steel properties offer good ductility in the annealed condition, allowing it to be bent or formed. Fusion and resistance welding is also possible with our 4340 alloy steel.
ASTM 4340 material is often utilized where other alloy steels do not have the hardenability to give the strength required. For highly stressed parts it is excellent choice. AISI 4340 alloy steel can also be machined by all customary methods.
Shapes and Sizes
IBC Metal Group supplies 4340 steel bar in a variety of sizes ranging from 1/2”-15”. The shapes available for this grade include: Rounds
AISI 4340 Alloy Steel Bar Specification and Relevant Standards

4340 Alloy Steel Bar and Equivalent Chemical Composition

Mechanical Property Ranges for Grade 4340
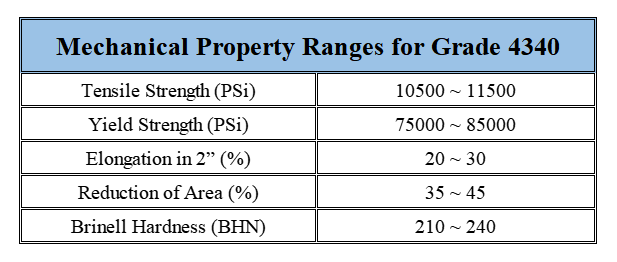
Forging of 4340 Alloy Steel Bar
Preheat the steel 4340 first, heat up to 1150°C – 1200°C maximum for forging, hold until temperature is uniform throughout the section.
Do not forge below 850 °C. 4340 has good forging characteristics but care must be taken when cooling as the steel shows susceptibility to cracking. Following forging operation the work piece should be cooled as slowly as possible. And cooling in in sand or dry lime is recommended etc.
AISI 4340 Alloy Steel Bar Heat Treatment
Stress Relieving
For pre-hardened steel stress relieving is achieved by heating steel 4340 to between 500 to 550°C. Heat to 600 °C – 650 °C, hold until temperature is uniform throughout the section, soak for 1 hour per 25 mm section, and cool in still air.
Annealing
A full anneal may be done at 844°C (1550 F) followed by controlled (furnace) cooling at a rate not faster than 10°C (50 F) per hour down to 315°C (600 F). From 315°C 600 F it may be air cooled.
Tempering
AISI 4340 alloy steel should be in the heat treated or normalized and heat treated condition before tempering. The tempering temperature for depends upon the strength level desired. For strength levels in the 260 – 280 ksi range temper at 232°C (450 F). For strength in the 125 – 200 ksi range temper at 510°C (950 F). And don’t temper the 4340 steels if it is in the 220 – 260 ksi strength range as tempering can result in degradation of impact resistance for this level of strength. Tempering should be avoided if possible within the range 250 °C – 450 °C due to temper brittleness.
Flame or Induction Hardening
As mentioned above, pre-hardened and tempered 4340 steel bars or plates can be further surface hardened by either the flame or induction hardening methods resulting in a case hardness in excess of Rc 50. AISI 4340 steel parts should be heated as quickly as possible to the austenitic temperature range (830 °C – 860 °C) and required case depth followed by an immediate oil or water quenching, depending upon hardness required, workpiece size/shape and quenching arrangements.
Following quenching to hand warm, tempering at 150°C – 200°C will reduce stresses in the case with minimal effect on its hardness. All de-carburised surface material must first be removed to ensure best results.
Nitriding
Hardened and tempered 4340 alloy steel can also be nitrided, giving a surface hardness of up to Rc 60. Heat to 500°C – 530°C and hold for sufficient time (from 10 to 60 hours) to develop the depth of case. Nitriding should be followed by slow cooling (no quench) reducing the problem of distortion. The nitrided grade 4340 materials can therefore be machined to near final size, leaving a small grinding allowance only. The tensile strength of the 4340 steel material core is usually not affected since the nitriding temperature range is generally below the original tempering temperature employed. Surface hardness achievable is 600 to 650HV.
Machinability
Machining is best done with the alloy steel 4340 in the annealed or normalized and tempered condition. It can be readily machined by all conventional methods such as sawing, turning, drilling etc. However in the high strength conditions of 200 ksi or greater the machinability is only from 25% to 10% that of the alloy in the annealed condition.
Applications of 4340 Alloy Steel Bar
Typical applications for this grade include axle shafts, heavy-duty shafting, and mine drilling parts.
AISI 4340 steel is used in most industry sectors for applications requiring higher tensile/yield strength than 4140 steel can provide. Some typical applications such as: Aircraft Landing Gear;Automotive;Oil and Gas Drilling;Forging;Warm and Cold Forming;Machine Building;Transfer Systems, like power transmission gears and shafts. General engineering industries and structural use applications, such as: heavy duty shafts, gears, axles, spindles, couplings, pins, chucks, molds etc.
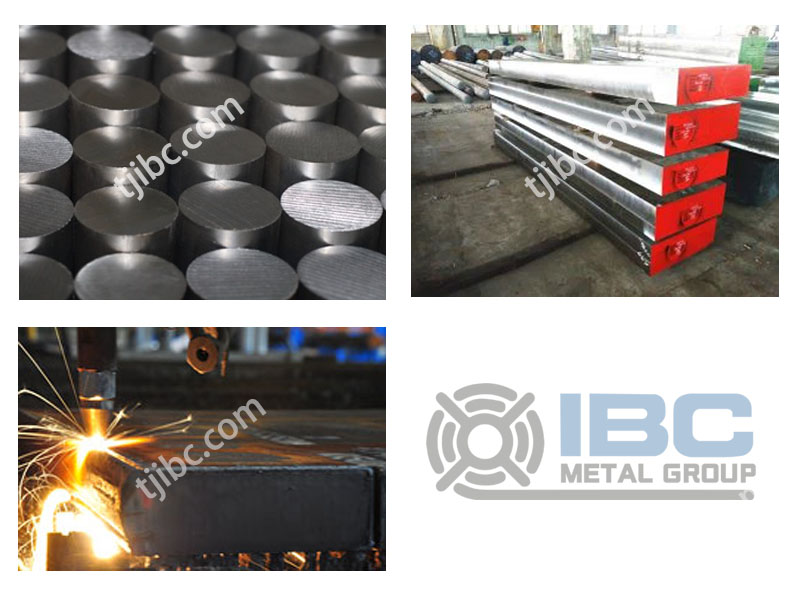
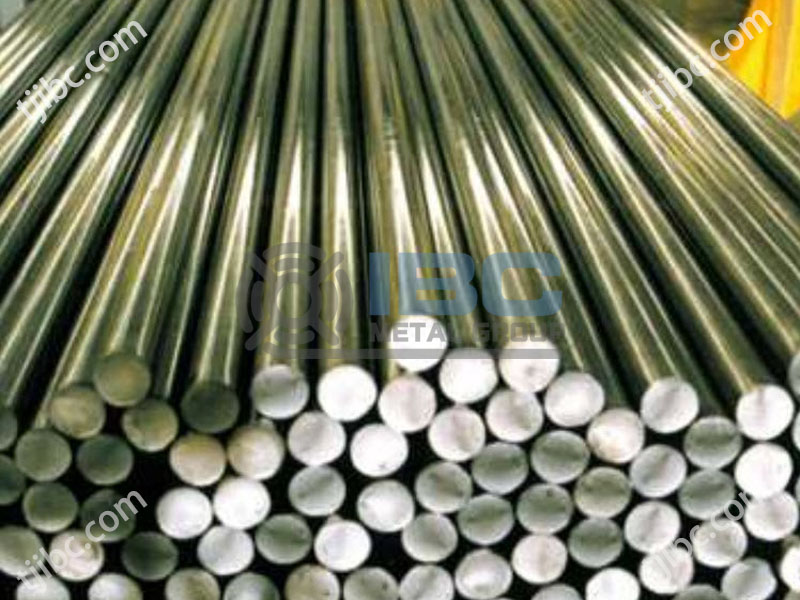
Contact with us Today!