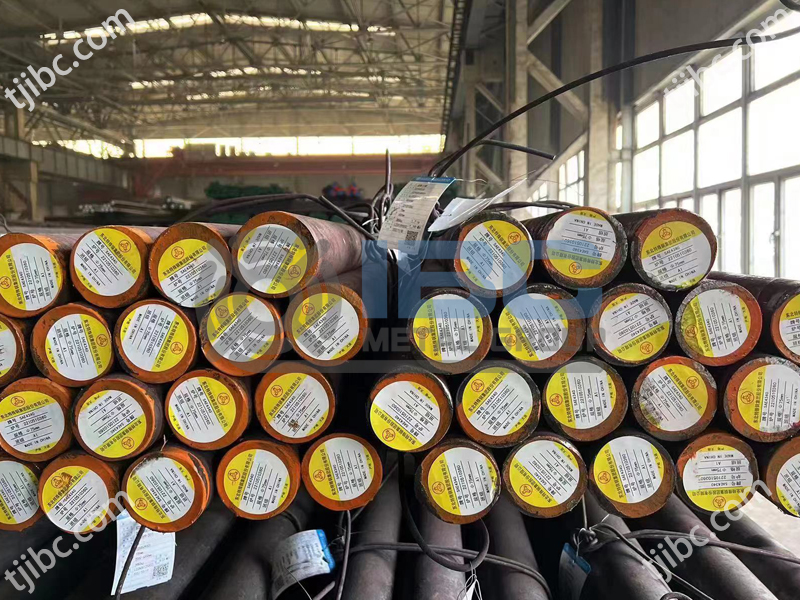
SAE 4340 Alloy Steel Supply Range
- SAE 4340 Steel Round Bar: Diameter 8mm – 3000mm
- 4340 Steel Plate: Thickness 10mm – 1500mm X Width 200mm – 3000mm
- Square SAE 4340 Steel Grade: 20mm – 500mm
- Surface Finish: Black, Rough Machined, Turned or as per given requirements.
Nickel-chromium-molybdenum alloy steel SAE 4340 Steel is known for its toughness and the ability to achieve high strength in the heat-treated condition. It has very good fatigue resistance.
While maintaining good toughness, wear resistance, and fatigue strength levels, this alloy, 4340, can also be heat treated to high strength levels with good atmospheric corrosion resistance.
Our Customers
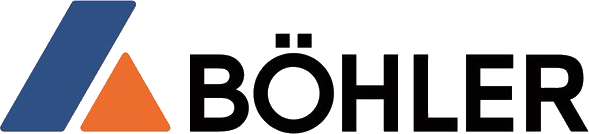
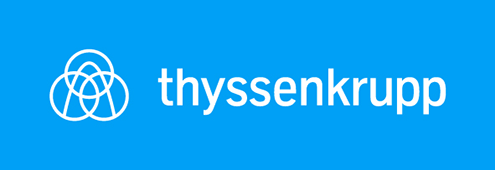
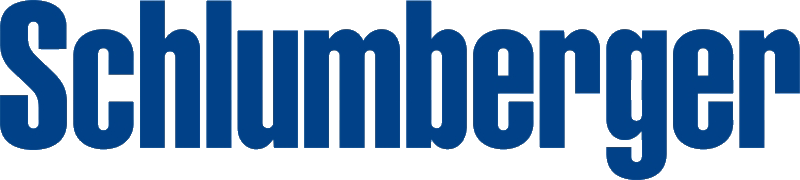
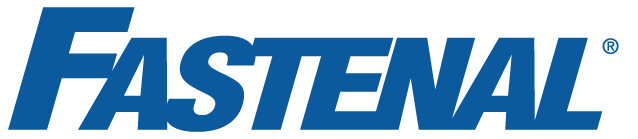
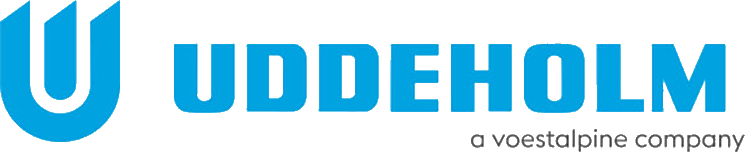
SAE 4340 Steel Bar Specification and Relevant Standards
Country | USA | Britain | Britain | Japan |
Standard | ASTM A29 | EN 10250 | BS 970 | JIS G4103 |
Grades | 4340 | 36CrNiMo4/1.6511 | EN24/817M40 | SNCM 439/SNCM8 |
SAE 4340 Steels And Equivalent Chemical Composition
Standard | Grade | C | Mn | P | S | Si | Ni | Cr | Mo |
ASTM A29 | SAE 4340 | 0.38-0.43 | 0.60-0.80 | 0.035 | 0.040 | 0.15-0.35 | 1.65-2.00 | 0.70-0.90 | 0.20-0.30 |
EN 10250 | 36CrNiMo4/1.6511 | 0.32-0.40 | 0.50-0.80 | 0.035 | 0.035 | ≦0.40 | 0.90-1.20 | 0.90-1.2 | 0.15-0.30 |
BS 970 | EN24/817M40 | 0.36-0.44 | 0.45-0.70 | 0.035 | 0.040 | 0.1-0.40 | 1.3-1.7 | 1.00-1.40 | 0.20-0.35 |
JIS G4103 | SNCM 439/SNCM8 | 0.36-0.43 | 0.60-0.90 | 0.030 | 0.030 | 0.15-0.35 | 1.60-2.00 | 0.60-1.00 | 0.15-0.30 |
SAE 4340 Chemical Composition
The following table shows the chemical composition of AISI 4340 alloy s
C % | Mn % max | P % | S % | Si % | Ni % | Cr % | Mo % |
0.38 – 0.43 | 0.6 – 0.8 | 0.035 max | 0.040 max | 0.15 – 0.3 | 1.65 – 2.0 | 0.7 – 0.9 | 0.2 – 0.3 |
AISI Alloy 4340 Alloy Steel Bar Mechanical Properties
Mechannical Properties (Heat Treated Condition ) | Condition | Ruling section | Tensile Strength | Yield Strength | Elong. | Izod Impact | Brinell Hardness |
mm | MPa | MPa | % | J | |||
T | 250 | 850-1000 | 635 | 13 | 40 | 248-302 | |
T | 150 | 850-1000 | 665 | 13 | 54 | 248-302 | |
U | 100 | 930-1080 | 740 | 12 | 47 | 269-331 | |
V | 63 | 1000-1150 | 835 | 12 | 47 | 293-352 | |
W | 30 | 1080-1230 | 925 | 11 | 41 | 311-375 | |
X | 30 | 1150-1300 | 1005 | 10 | 34 | 341-401 | |
Y | 30 | 1230-1380 | 1080 | 10 | 24 | 363-429 | |
Z | 30 | 1555- | 1125 | 5 | 10 | 444- |
Thermal Properties
Properties | Metric | Imperial |
Thermal expansion co-efficient (20°C/68°F, specimen oil hardened, 600°C (1110°F) temper | 12.3 µm/m°C | 6.83 µin/in°F |
Thermal conductivity (typical steel) | 44.5 W/mK | 309 BTU in/hr.ft².°F |
AISI four-digit numbers distinguish alloy steels from carbon steels. They include a variety of steels whose composition exceeds the limitations imposed on carbon steels for B, C, Mn, Mo, Ni, Si, Cr, and Va. In the heat treated condition, AISI 4340 alloy steel has high toughness and strength. It contains chromium, nickel, and molybdenum. It contains chromium, nickel, and molybdenum.
What is the Difference Between SAE 4340 and AISI 4340?
Let’s make a conclusion first, there is almost no difference between SAE 4340 and AISI 4340. SAE 4340 is from the Society of Automotive Engineers, and AISI 4340 is from the American Iron and Steel Institute.They essentially point to the same meaning of the material, which is the 4340 material in the ASTM A29 standard. It is just that the implementation of the society is different, and the statement is different. Therefore, from the above, it can be seen that “4340”, “AISI 4340” or “SAE 4340”, although written differently, but in most general industrial applications,any of the above is considered equivalent.
AISI 4340 Alloy Steel Applications
AISI 4340 alloy steel is mainly used in power transmission gears and shafts, aircraft landing gear, and other structural parts, commercial and military aircraft, automotive systems, forged hydraulic and other machine tool applications, forged steel crankshafts. AISI 4340 steel is used in most industry sectors for applications requiring higher tensile/yield strength than 4140 steel can provide. Some typical applications such as:
- Aircraft Landing Gear
- Automotive,
- Oil and Gas Drilling,
- Forging,
- Warm and Cold Forming,
- Machine Building,
- Transfer Systems, like power transmission gears and shafts.
General engineering industries and structural use applications, such as: heavy duty shafts, gears, axles, spindles, couplings, pins, chucks, molds etc.
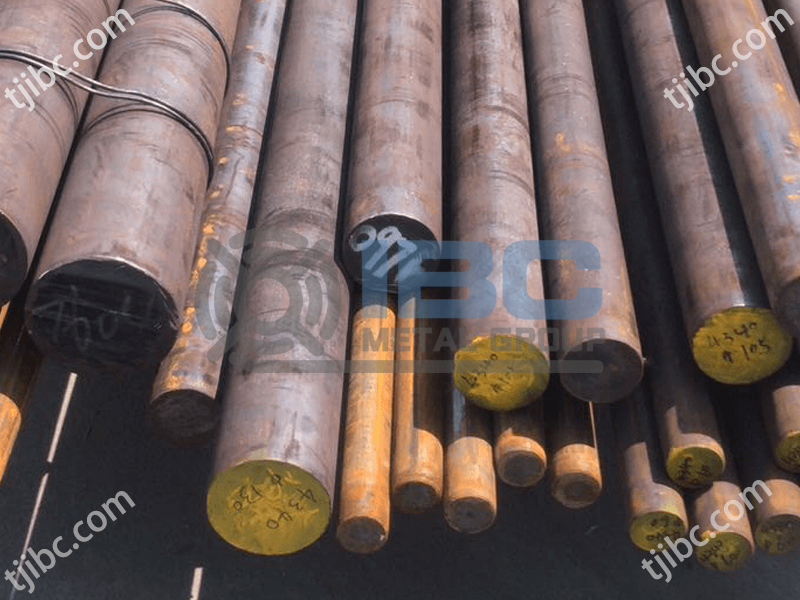
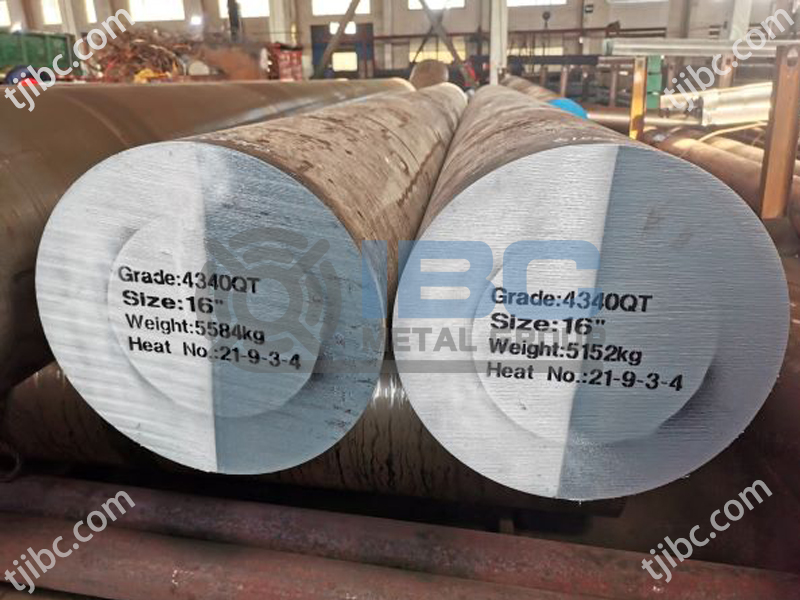
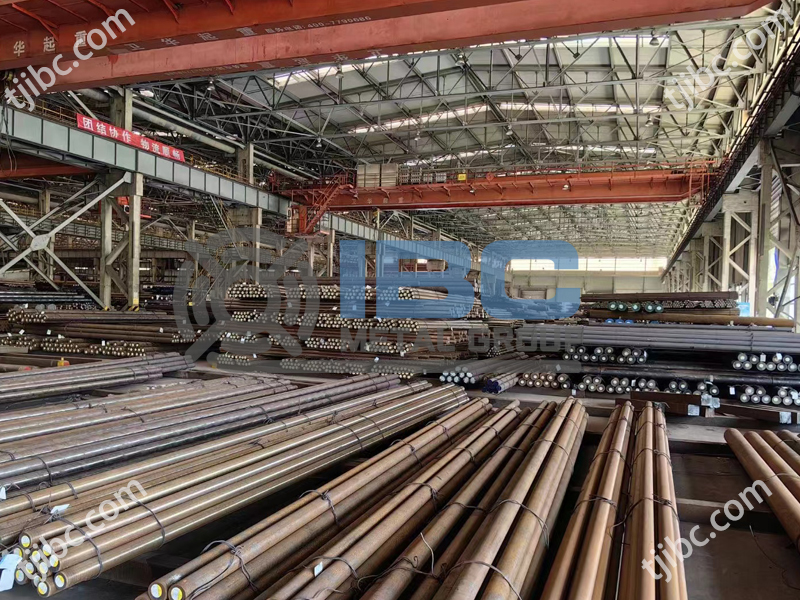
ANSI 4340 Forging
ANSI 4340 alloy steel is forged at 980 to 1233°C.In another way, Forging should be carried out between 2250 and 1800 º F. Parts should be slow cooled after forging in ashes or sand etc.
AISI 4340 Steel Bar Heat Treatment
Heat treatment after forging is carried out to render the steel suitable for machining, and to meet the mechanical property limits specified for the steel’s particular applications. There are several ways to heat treat a given steel part and it is only through practice that the optimum temperature and conditions may be defined. The following information should be taken as a guide only.
4340 Bar Annealing
To obtain a pearlitic structure on certain parts for machining, AISI 4340 alloy steel should annealed at a nominal temperature of 1525 º F (830 º C,) cooling to 1350 º F (730 º C) and furnace cooling to 1130 º F (610 º C) at a rate of 20 º F (11 º C) per hour, then air cooling.
This process, known as full annealing, is very time consuming as it involves slow cooling over the entire temperature range from the austenitizing temperature to a temperature well below that at which transformation is complete. To obtain a spheroidized structure in 4340 grade involves austenitizing at 1380 º F (750 º C,) furnace cooling to 1300 º F (705 º C) then to 1050 º F (565 º C) at a rate of 5 º F (3 º C) per hour. This structure will probably result in better machinability than will the coarse lamellar pearlite structure obtained by the full anneal process.
Normalizing of AISI 4340
This process is defined as heating a steel to a temperature above the ferrite to austenite transformation temperature, then cooling in air to a temperature well below this transformation temperature. The treatment may be carried out on forged products as a conditioning treatment prior to final heat treatment. Normalizing also serves to refine the structure of forgings that might have cooled non-uniformly from their forging operation. The nominal normalizing temperature for 4340 grade is 1500 º F (815 º C,) but production experience may necessitate a temperature either 50 º F (10 º C) above or below this temperature. . As a rule of thumb, when forgings are normalized before, say, carburizing or hardening and tempering, the upper range of normalizing temperatures is used. When normalizing is the final heat treatment, the lower temperature range is used.
Hardening of SAE 4340
AISI 4340 alloy steel can be hardened by cold working or heat treatment. This heat treatment results in the formation of martensite after quenching, resulting in increased hardness and tensile strength. A temperature range of 1500 – 1550 º F (815 – 845 º C) is the normal austenitizing temperature for direct hardening of 4340 grade. Oil quenching is normally used for 4340 as the alloy’s hardenability is suited to this quenching method.
Tempering
AISI 4340 alloy steel should be in the heat treated or normalized and heat treated condition before tempering. Tempering temperatures depend upon the desired strength level. Tempering is carried out to relieve stresses from the hardening process, but primarily to obtain mechanical properties required for the final application. The actual tempering temperature will be chosen to meet the required properties, and in many cases will be a matter of trial and error. This grade 4340 may also be hardened by nitriding or flame or induction hardening.
Machinability
This grade is readily machinable, with either a coarse lamellar pearlitic structure or a spheroidized structure being best advised, depending upon section size and complexity and amount of machining to be carried out. If there is doubt about the suitability of any other structure, then a spheroidizrd structure should be aimed for in heat treatment.
Welding
AISI 4340 alloy steel can be welded using fusion or resistance welding methods. Preheat and post heat weld procedures are followed while welding this steel by established methods. This grade is readily welded in the annealed condition, but welding in the hardened and tempered condition should be avoided where possible because of the effect on mechanical properties. Welding in the nitrided or flame or induction hardened conditions is not recommended. Guidance details for welding include the use of low-hydrogen electrodes and a preheat from 400 – 570 º F (200 – 300 º C,) if possible to be maintained during welding. Parts should be slow cooled after welding in ashes or sand and stress relieved if possible.
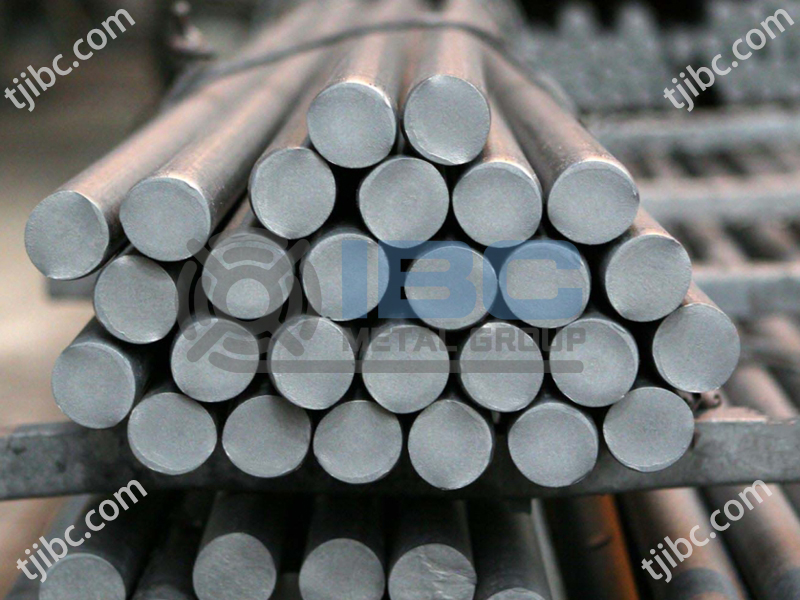
Contact with us today!