ASTM A755 – Standard Specification for Steel Sheet, Metallic Coated by the Hot-Dip Process and Prepainted by the Coil-Coating Process for Exterior Exposed Building Products.
Abstract of ASTM A755 / A755M
This guide covers standard specification for steel sheet metallic coated by the hot-dip process and coil-coated with organic films for exterior exposed building products.
The substrate shall conform to all requirements of the appropriate specification for the steel sheet product. Material classification includes zinc-coated (galvanized), aluminum-zinc alloy-coated, and aluminum coated steel sheets. The recommended minimum coating mass designations for use in exterior exposed building applications shall be indicated.

The properties of the substrate and the organic coating system, combined with the method of forming, shall determine the life expectancy and general appearance of the final product.
1. Firstly, Scope of ASTM A755 / A755M
1.1 This specification covers steel sheet metallic coated by the hot-dip process and coil-coated with organic films for exterior exposed building products. Sheet of this designation is furnished in coils, cut lengths, and formed cut lengths. Building products include corrugated and various types of roll and brake-formed configurations.
1.2 The substrate available in several different metallic-coated steel sheet products as enumerated in 4.1, depending on the requirements of the purchaser.
1.3 Coating systems supplied under this specification consist of a primer coat covered by various types and thicknesses of top coats. The combination of primer and top coat classed as either a two-coat thin-film system or as a two-coat (or more) thick-film system. Typical top-coating materials are: polyester, silicone polyester, acrylic, fluoropolymer, plastisol, or polyurethane.
1.4 This specification is applicable to orders in either inch-pound units (as A755) or SI units [as A755M]. Values in inch-pound units and SI units are not necessarily equivalent. Within the text, SI units shown in brackets. Each system shall be used independently of each other.
1.5 Unless the order specifies the “M” designation (SI units) the product shall furnish to inch-pound units.
1.6 The text of this specification references notes and footnotes that provide explanatory material. These notes and footnotes, excluding those in tables and figures, shall not consider as requirements of this specification.
1.7 This standard does not purport to address all of the safety concerns, if any, associated with its use. It is the responsibility of the user of this standard to establish appropriate safety and health practices and determine the applicability of regulatory limitations prior to use.
2. Secondly, Referenced Documents
2.1 ASTM Standards
- A463/A463M Specification for Steel Sheet, Aluminum Coated, by the Hot-Dip Proces
- A653/A653M Specification for Steel Sheet, Zinc-Coated (Galvanized) or Zinc-Iron Alloy-Coated (Galvannealed) by the Hot-Dip Process
- A792/A792M Specification for Steel Sheet, 55 % Aluminum-Zinc Alloy-Coated by the Hot-Dip Process
- A875/A875M Specification for Steel Sheet, Zinc-5 % Aluminum Alloy-Coated by the Hot-Dip Process
- A902 Terminology Relating to Metallic Coated Steel Products
- A924/A924M Specification for General Requirements for Steel Sheet, Metallic-Coated by the Hot-Dip Process
- A1046/A1046M Specification for Steel Sheet, Zinc Aluminum-MagnesiumAlloy-Coated by the Hot-Dip Process
- A1063/A1063M Specification for Steel Sheet, Twin-Roll Cast, Zinc-Coated (Galvanized) by the Hot-Dip Process
- B117 Practice for Operating Salt Spray (Fog) Apparatus
- D522 Test Methods for Mandrel Bend Test of Attached Organic Coatings
- D523 Test Method for Specular Gloss
- D659 Method for Evaluating Degree of Chalking of Exterior Paints (Withdrawn 1990) 3
- D714 Test Method for Evaluating Degree of Blistering of Paints
- D822 Practice for Filtered Open-Flame Carbon-Arc Exposures of Paint and Related Coatings
- D870 Practice for Testing Water Resistance of Coatings Using Water Immersion
- D1005 Test Method for Measurement of Dry-Film Thickness of Organic Coatings Using Micrometers
- D1654 Test Method for Evaluation of Painted or Coated Specimens Subjected to Corrosive Environments
- D1735 Practice for Testing Water Resistance of Coatings Using Water Fog Apparatus
- D2240 Test Method for Rubber Property—Durometer Hardness
- D2244 Practice for Calculation of Color Tolerances and Color Differences from Instrumentally Measured Color Coordinates
- D2247 Practice for Testing Water Resistance of Coatings in 100 % Relative Humidity
- D2370 Test Method for Tensile Properties of Organic Coatings
- D3359 Test Methods for Measuring Adhesion by Tape Test
- D3363 Test Method for Film Hardness by Pencil Test
- D4145 Test Method for Coating Flexibility of Prepainted Sheet
- D4214 Test Methods for Evaluating the Degree of Chalking of Exterior Paint Films
- G85 Practice for Modified Salt Spray (Fog) Testing
3. Thirdly, Terminology
3.1 Definitions:
3.2 Definitions of Terms Specific to This Standard:
4. Fourthly, Classification of ASTM A755
4.1 The substrate shall conform to all requirements of the appropriate specification for the steel sheet product ordered as follows:
5. Moreover, Ordering Information
5.1 The coated flat sheet covered by this specification produced on continuous lines to decimal thickness only. The thickness of the sheet includes the base steel and the metallic coating. The thickness of the organic system is in addition to the substrate (base steel and metallic coating).
5.2 Orders for material under this specification shall include the following information, as applicable, to describe the required product adequately:
6. Then, Substrate Requirements
6.1 For the purposes of this specification, substrate refers to the steel sheet and metallic coating. The specific requirements for the substrate contained in the specifications listed in 4.1.
7. As following, Organic Coating Requirements
7.1 The application of organic coatings on a continuous coil coating line, when producing products to the requirements of this specification, involves three major steps. These are: the application of a conversion coating, the application of a primer, and the application of one or more topcoats.
7.2 Conversion Coating — A conversion coating is a chemical treatment apply to the metal prior to application of the primer. It design to react with and modify the metal surface to enable chemical bonding to occur between the metal and the primer thus optimizing adhesion and corrosion resistance.
7.3 Primer:
7.4 Topcoat:
7.5 Washcoat or Backercoat:
7.6 Testing Requirements—The properties of the substrate and the organic coating system, combined with the method of forming, determine the life expectancy and general appearance of the final product. Each coating system has different qualities in regard to gloss, flexibility, fading, chalking, resistance to cracking at bends, abrasion resistance, dirt retention, and resistance to varying atmospheric conditions. All of these factors must be considered in any end application. The test methods used to measure some of these parameters – listed in Annex A1 and are normally considered to be mandatory requirements. The test methods listed in Appendix X1 are used to measure other parameters but are generally considered to nonmandatory requirements. The specific requirements for each system must agree upon between the producer and the purchaser.
8. At last, Packaging, Marking, And Loading
8.1 See Specification A924/A924M. In addition, coils will be shipped eye vertical to minimize transit abrasion. Rollformed panels require special packaging. Coil-coat steel – finish material and must treat as such in handling and storage.
8.2 Proper on-site storage of building panels prior to erection has been found to be important in maintaining the integrity of the coating system. Corrosion failure will result when building panels not properly protected from water being trapped during storage prior to installation. Pallets must place off the ground and at a slight angle for effective drainage. In addition, the use of metal covers or the equivalent is an effective way of keeping pallets dry. Do not use plastic bags to protect the coils or pallets.
9. Finally, Keywords in ASTM A755 / A755M-15
9.1 coatings, nonmetallic; coatings, painted; coil-coating process; painted sheet; roofing materials; siding materials; steel sheet
ASTM A755 is standard specification for Prepainted Galvanized Steel Coils. These are not the whole description for astm a755.
If you want to see the whole standard specification, you could contact with us. Of you could download the PDF files here.
Or contact with us:
- Mobile: +86-15222480985
- Tel: +86-22-27168866
- E-mail: sales@ibcmetalgroup.com
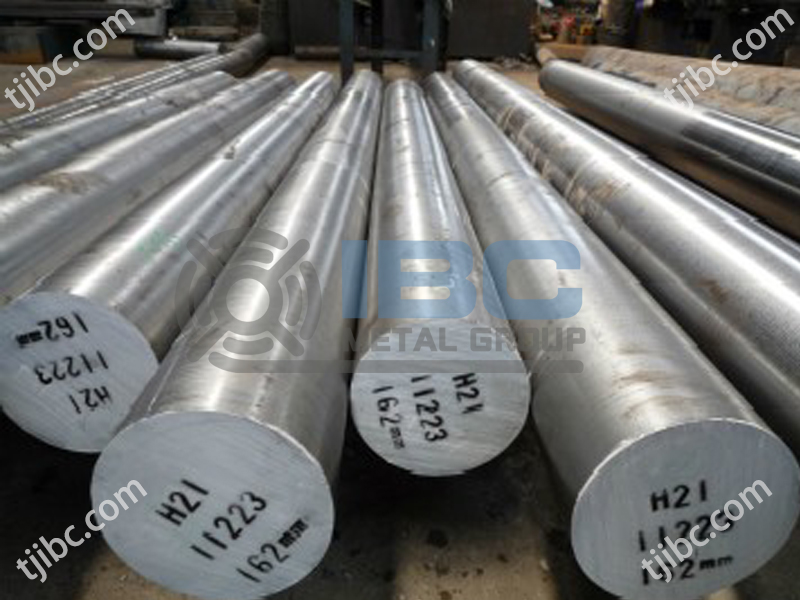
Contact with IBC Metal Group Today!